Resolving fire suppression system failures
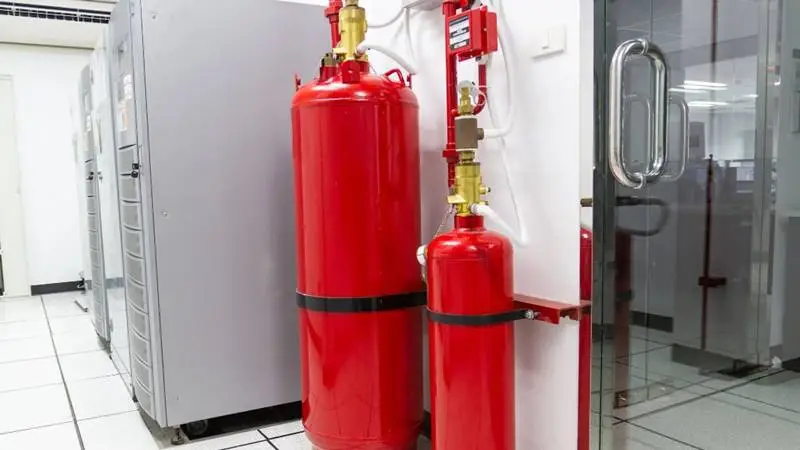
The Critical Importance of Fire Suppression Systems in Laboratories
In the realm of scientific research and development, laboratories stand as the epicenter of innovation, where groundbreaking discoveries are made and technological advancements are forged. These specialized environments, however, harbor inherent risks, particularly the potential for fire outbreaks. The presence of flammable materials, volatile chemicals, and intricate electrical systems creates a complex interplay of factors that can lead to catastrophic consequences if not adequately addressed. This is where the paramount importance of fire suppression systems comes into play, serving as a critical safety measure to mitigate the risks associated with fire hazards in laboratories.
Fire suppression systems, meticulously designed and engineered, are the first line of defense against the devastating effects of fire. They act as a vital safety net, safeguarding both human life and valuable research assets. These systems are not merely passive components; they are dynamic and responsive, capable of detecting the early signs of a fire and initiating a rapid and effective response. Their effectiveness hinges on a complex interplay of sensors, actuators, and control mechanisms, all working in concert to contain and extinguish a fire before it can escalate into a major disaster.
The consequences of fire suppression system failures can be dire, ranging from minor disruptions to catastrophic losses. A malfunctioning system can leave a laboratory vulnerable to the ravages of fire, jeopardizing the safety of personnel, compromising valuable research data, and causing significant financial damage. In the worst-case scenario, a fire can lead to the complete destruction of a laboratory, setting back research progress by years and potentially causing irreparable harm to the scientific community.
The need for reliable and robust fire suppression systems in laboratories is undeniable. These systems are not simply a regulatory requirement; they are a fundamental pillar of laboratory safety. Their effectiveness is directly proportional to the level of care and attention given to their maintenance, inspection, and testing. Regular maintenance ensures that the system is in optimal working condition, capable of responding effectively to any fire emergency. Inspections and testing provide a comprehensive evaluation of the system's functionality, identifying potential weaknesses and addressing them before they can lead to catastrophic failures.
The scientific community, encompassing lab technicians, project managers, procurement managers, and C-suites, bears a collective responsibility for ensuring the integrity and functionality of fire suppression systems. It is imperative that all stakeholders understand the critical role these systems play in safeguarding laboratories and the invaluable research conducted within them. This understanding should translate into a proactive approach to fire safety, prioritizing regular maintenance, inspections, and testing, and fostering a culture of vigilance and preparedness.
This article delves into the complexities of fire suppression system failures, exploring the underlying causes, the potential consequences, and the best practices for preventing and mitigating these failures. By shedding light on the critical aspects of fire suppression system maintenance and troubleshooting, this article aims to empower laboratory professionals with the knowledge and tools necessary to ensure the safety and security of their research environments.
The journey to resolving fire suppression system failures begins with a thorough understanding of the system's design, operation, and potential vulnerabilities. This article serves as a guide, providing insights into the intricate workings of fire suppression systems and equipping readers with the knowledge to identify, diagnose, and address potential issues before they escalate into major problems.
By embracing a proactive approach to fire safety, laboratory professionals can significantly reduce the risk of fire suppression system failures, ensuring the safety of their personnel, the integrity of their research, and the continued advancement of scientific knowledge.
Understanding the Importance of Fire Suppression Systems in Laboratories
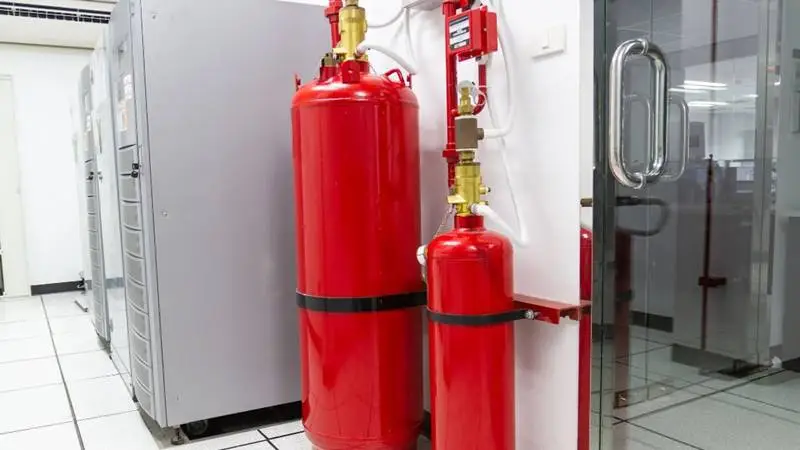
Laboratories, with their inherent presence of flammable materials, volatile chemicals, and intricate equipment, are inherently susceptible to fire hazards. The consequences of a fire in a laboratory setting can be catastrophic, ranging from equipment damage and data loss to potential injuries and even fatalities. This underscores the paramount importance of robust fire suppression systems in safeguarding laboratories and ensuring the safety of personnel and valuable assets.
Fire suppression systems are engineered to detect and extinguish fires rapidly, minimizing the potential for damage and injury. These systems are typically designed to activate automatically upon detecting a fire, deploying a fire suppressant agent to control and extinguish the flames. The effectiveness of these systems hinges on their proper installation, regular maintenance, and prompt response in the event of a fire.
However, despite the critical role of fire suppression systems in laboratory safety, instances of system failures are not uncommon. These failures can stem from various factors, including malfunctioning components, inadequate maintenance, improper installation, or even environmental conditions. When a fire suppression system fails to function as intended, it can have dire consequences, potentially leading to uncontrolled fires and significant losses.
Delving into the Causes of Fire Suppression System Failures
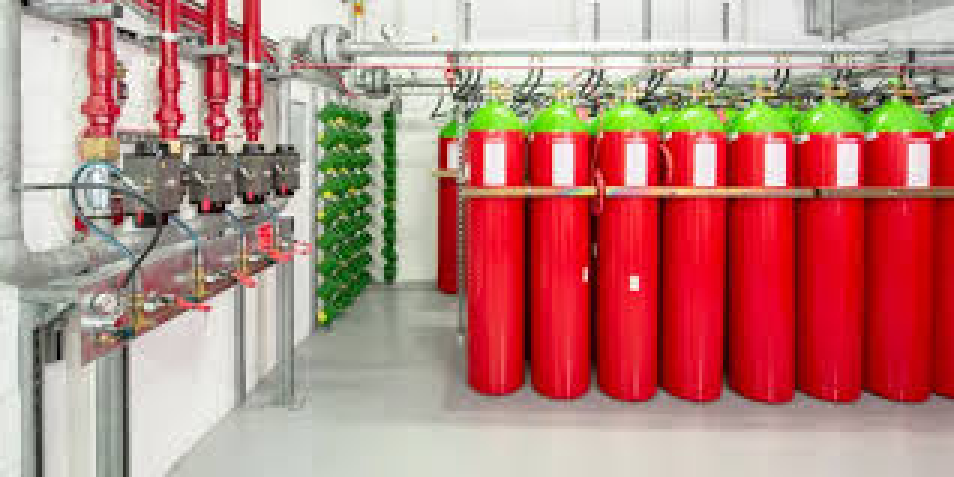
To effectively address fire suppression system failures, it is essential to understand the underlying causes. These failures can be broadly categorized into three primary areas:
1. Mechanical Failures
Mechanical failures encompass issues related to the physical components of the fire suppression system. These can include:
- Malfunctioning Detectors: Fire detectors, the eyes of the system, are responsible for sensing the presence of fire. Faulty detectors, whether due to age, environmental factors, or improper installation, can fail to detect a fire, rendering the system ineffective.
- Defective Suppression Agent Delivery System: The system responsible for delivering the fire suppressant agent, including pipes, valves, and nozzles, can experience malfunctions. These malfunctions can range from leaks and blockages to faulty valves and nozzle malfunctions, hindering the effective deployment of the suppressant agent.
- Corrosion and Wear: Over time, the components of the fire suppression system can experience corrosion and wear due to exposure to chemicals, humidity, or other environmental factors. This degradation can compromise the integrity of the system, leading to malfunctions and failures.
- Improper Installation: Incorrect installation of the fire suppression system, including improper placement of detectors, inadequate pipe sizing, or faulty connections, can significantly impact the system's performance and increase the risk of failures.
2. Environmental Factors
Environmental factors can also contribute to fire suppression system failures. These include:
- Temperature Extremes: Extreme temperatures, both high and low, can affect the performance of fire suppression system components. For instance, excessive heat can damage detectors and other sensitive components, while freezing temperatures can cause pipes to freeze and burst, disrupting the system's functionality.
- Humidity and Moisture: High humidity levels can lead to corrosion and condensation, affecting the performance of electrical components and sensors. Moisture can also interfere with the proper functioning of detectors and other sensitive equipment.
- Dust and Debris: Accumulation of dust and debris on detectors and other system components can obstruct their operation, hindering their ability to detect fire and activate the suppression system.
- Chemical Exposure: Exposure to certain chemicals, particularly corrosive or volatile substances, can damage the components of the fire suppression system, leading to malfunctions and failures.
3. Human Error
Human error plays a significant role in fire suppression system failures. These errors can include:
- Inadequate Maintenance: Regular maintenance is crucial for ensuring the proper functioning of fire suppression systems. Neglecting maintenance schedules, skipping inspections, or failing to address identified issues can lead to system failures and compromised safety.
- Improper Operation: Misunderstanding the operation of the fire suppression system, including the activation procedures and the use of manual controls, can lead to unintended consequences and system failures.
- Lack of Training: Insufficient training for laboratory personnel on fire safety procedures, including the operation of fire suppression systems, can result in improper responses during emergencies, potentially exacerbating the situation.
- Modifications and Alterations: Unauthorized modifications or alterations to the fire suppression system, without proper engineering oversight, can compromise the system's integrity and increase the risk of failures.
The Impact of Fire Suppression System Failures
The consequences of fire suppression system failures can be severe, impacting various aspects of laboratory operations and safety:
- Property Damage: A failed fire suppression system can lead to uncontrolled fires, resulting in significant damage to laboratory equipment, infrastructure, and valuable research materials. This damage can disrupt research activities, delay projects, and incur substantial financial losses.
- Data Loss: Laboratories often house sensitive data, including research findings, experimental results, and patient records. A fire can destroy this data, leading to irreplaceable losses and hindering future research efforts.
- Personal Injury and Fatalities: Uncontrolled fires pose a serious threat to laboratory personnel, potentially leading to injuries, burns, and even fatalities. The absence of a functioning fire suppression system can exacerbate the risks associated with fire hazards.
- Environmental Contamination: Laboratories often handle hazardous materials, and a fire can release these materials into the environment, posing risks to human health and the ecosystem.
- Reputational Damage: A fire incident, particularly one involving a failed fire suppression system, can damage the reputation of the laboratory and the institution it represents, impacting public trust and funding opportunities.
Navigating the Troubleshooting Process for Fire Suppression System Failures
When a fire suppression system fails to function as intended, it is crucial to initiate a thorough troubleshooting process to identify the root cause of the failure and implement corrective measures. This process typically involves the following steps:
1. Initial Assessment
The initial assessment involves gathering information about the failure event, including the time and date of the failure, the specific components involved, and any observed symptoms or behaviors. This information can provide valuable insights into the potential causes of the failure.
2. Visual Inspection
A visual inspection of the fire suppression system is essential to identify any visible signs of damage, corrosion, or wear. This inspection should cover all components of the system, including detectors, pipes, valves, nozzles, and control panels.
3. Functional Testing
Functional testing involves simulating fire conditions to assess the performance of the fire suppression system. This testing can involve activating the system manually or using specialized equipment to generate simulated fire conditions. The results of the functional testing can help identify any malfunctions or deficiencies in the system's operation.
4. Data Analysis
Analyzing data from the fire suppression system, such as alarm logs, sensor readings, and system performance records, can provide valuable insights into the cause of the failure. This data can help identify patterns, trends, and potential contributing factors.
5. Expert Consultation
In complex cases, it may be necessary to consult with fire suppression system experts, such as certified technicians or engineers, to assist with troubleshooting and diagnosis. These experts can provide specialized knowledge and experience in identifying and resolving complex system failures.
Implementing Corrective Measures
Once the root cause of the fire suppression system failure has been identified, it is essential to implement corrective measures to address the issue and prevent future failures. These measures may include:
- Repair or Replacement of Defective Components: Defective components, such as malfunctioning detectors, damaged pipes, or faulty valves, should be repaired or replaced with new, compatible parts.
- Maintenance and Inspection: Regular maintenance and inspection schedules should be established and strictly adhered to. This includes cleaning, testing, and inspecting all components of the fire suppression system to ensure their proper functioning.
- Environmental Control: Measures should be taken to control environmental factors that can affect the performance of the fire suppression system. This may include controlling temperature and humidity levels, minimizing dust and debris accumulation, and protecting the system from chemical exposure.
- Training and Education: Laboratory personnel should receive comprehensive training on fire safety procedures, including the operation of fire suppression systems. This training should cover the proper use of the system, emergency response protocols, and the importance of regular maintenance.
- System Upgrades: In some cases, it may be necessary to upgrade the fire suppression system to meet current safety standards or to address specific vulnerabilities identified during troubleshooting.
Ensuring the Reliability and Effectiveness of Fire Suppression Systems
The reliability and effectiveness of fire suppression systems are paramount to laboratory safety. By understanding the causes of system failures, implementing thorough troubleshooting procedures, and taking proactive measures to prevent future failures, laboratories can significantly enhance their safety and mitigate the risks associated with fire hazards.
Regular maintenance, comprehensive training, and a commitment to safety are essential for ensuring the proper functioning of fire suppression systems. By prioritizing these aspects, laboratories can create a safer environment for their personnel, protect valuable assets, and maintain the integrity of their research activities.
Preventing Future Failures: A Proactive Approach to Fire Suppression System Reliability
The journey towards ensuring the consistent reliability of your laboratory's fire suppression system doesn't end with troubleshooting and resolving immediate issues. It demands a proactive approach, one that anticipates potential problems and implements preventative measures to minimize the risk of future failures. This proactive approach is crucial for safeguarding your valuable research, equipment, and most importantly, the safety of your personnel.
The first step in this proactive approach is to establish a comprehensive maintenance schedule. Regular inspections, testing, and servicing of all components of the fire suppression system are essential. This includes, but is not limited to:
- Regular Inspections: Visual inspections of the system's components, including piping, valves, nozzles, and detectors, should be conducted at least annually. These inspections should identify any signs of corrosion, damage, or wear and tear that could compromise the system's functionality.
- Functional Testing: Periodic functional testing of the entire system is crucial to ensure its ability to respond effectively in an emergency. This involves simulating a fire event and verifying that all components, including the fire suppression agent release, operate as intended. The frequency of these tests should be determined based on the specific system and local regulations.
- Maintenance and Servicing: Regular maintenance and servicing of the system's components are essential to prevent wear and tear and ensure optimal performance. This includes cleaning, lubrication, and replacement of worn-out parts. A qualified technician should perform these tasks according to the manufacturer's recommendations.
Beyond regular maintenance, it's also important to implement a comprehensive training program for your laboratory personnel. This training should cover the following aspects:
- Fire Safety Awareness: All personnel should be educated on the importance of fire safety and the potential hazards associated with their work. This includes understanding the proper use of fire extinguishers, evacuation procedures, and the location of emergency exits.
- Fire Suppression System Operation: Training on the operation of the fire suppression system is crucial. This includes understanding the system's activation mechanisms, the types of fire suppression agents used, and the potential hazards associated with their release. Personnel should also be trained on how to identify and report any potential issues with the system.
- Emergency Response Procedures: Training on emergency response procedures is essential to ensure a coordinated and effective response in the event of a fire. This includes evacuation procedures, communication protocols, and the roles and responsibilities of different personnel during an emergency.
In addition to maintenance and training, it's also important to consider the following factors to further enhance the reliability of your fire suppression system:
- Environmental Considerations: The environment in which the fire suppression system operates can significantly impact its performance. Factors such as temperature, humidity, and the presence of corrosive substances can degrade the system's components over time. Regular monitoring of these environmental factors and adjustments to the system's maintenance schedule as needed can help mitigate these risks.
- System Design and Installation: The design and installation of the fire suppression system are crucial for its effectiveness. Proper design considerations, including the selection of appropriate fire suppression agents, the placement of detectors and nozzles, and the size and capacity of the system, are essential for ensuring adequate coverage and protection. Regular review of the system's design and installation by a qualified engineer can help identify any potential weaknesses or areas for improvement.
- Regular Audits and Inspections: Regular audits and inspections by a qualified third-party can provide an independent assessment of the fire suppression system's performance and identify any potential issues that may have been overlooked during routine maintenance. These audits should be conducted at least annually and should include a comprehensive review of the system's design, installation, maintenance records, and operational procedures.
By implementing these proactive measures, you can significantly reduce the risk of fire suppression system failures and ensure the safety and security of your laboratory. Remember, a reliable fire suppression system is not a luxury; it's an essential investment in the safety of your personnel, the protection of your valuable research, and the continuity of your operations.
IT Tech understands the critical role of fire suppression systems in safeguarding your laboratory environment. We offer a comprehensive range of fire suppression equipment and consumables, including:
- Fire Suppression Agents: We provide a wide selection of fire suppression agents, including clean agents, water-based systems, and foam systems, to meet the specific requirements of your laboratory environment.
- Fire Suppression Systems: We offer a variety of fire suppression systems, including pre-engineered systems, custom-designed systems, and modular systems, to ensure optimal protection for your laboratory.
- Fire Suppression System Components: We provide a complete range of fire suppression system components, including detectors, nozzles, valves, piping, and control panels, to ensure the seamless integration and operation of your system.
- Maintenance and Servicing: We offer comprehensive maintenance and servicing programs for your fire suppression system, ensuring its optimal performance and reliability.
To ensure the safety and security of your laboratory, contact IT Tech today. Our team of experts can help you select the right fire suppression system for your specific needs and provide comprehensive support throughout the entire process, from design and installation to maintenance and servicing. Don't wait until a fire occurs; take proactive steps to protect your laboratory and ensure the safety of your personnel. Submit an enquiry today and let IT Tech help you build a safer and more secure laboratory environment.
Subscribe to our newsletter
Stay updated with IT-Tech Insights
Related posts
Check out other IT- Tech Scientific Resources
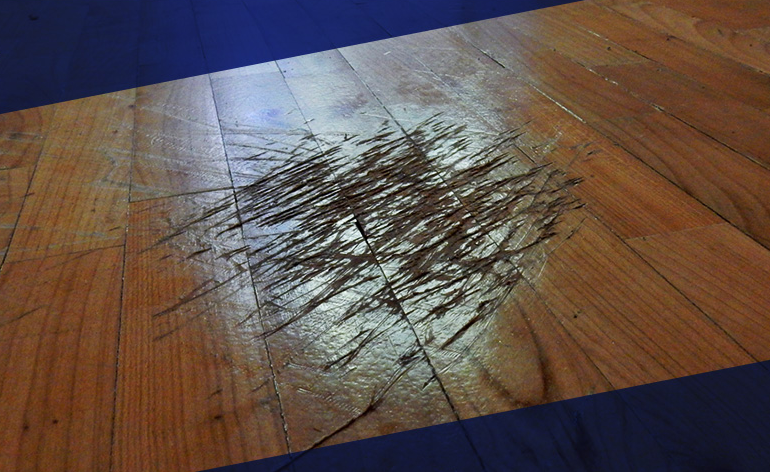
troubleshooting-lab-flooring-and-surface-damage
Lab flooring and surfaces are subjected to constant wear and tear from chemicals, spills, heavy equipment, and foot traffic. This can lead to damage that affects the safety and functionality of your lab. This article will guide you through the process of troubleshooting common flooring and surface damage, including identifying the causes, assessing the severity, and choosing the appropriate repair or replacement solutions. We'll cover topics such as cracks, stains, scratches, and delamination, providing practical tips and advice to help you maintain a safe and efficient lab environment.
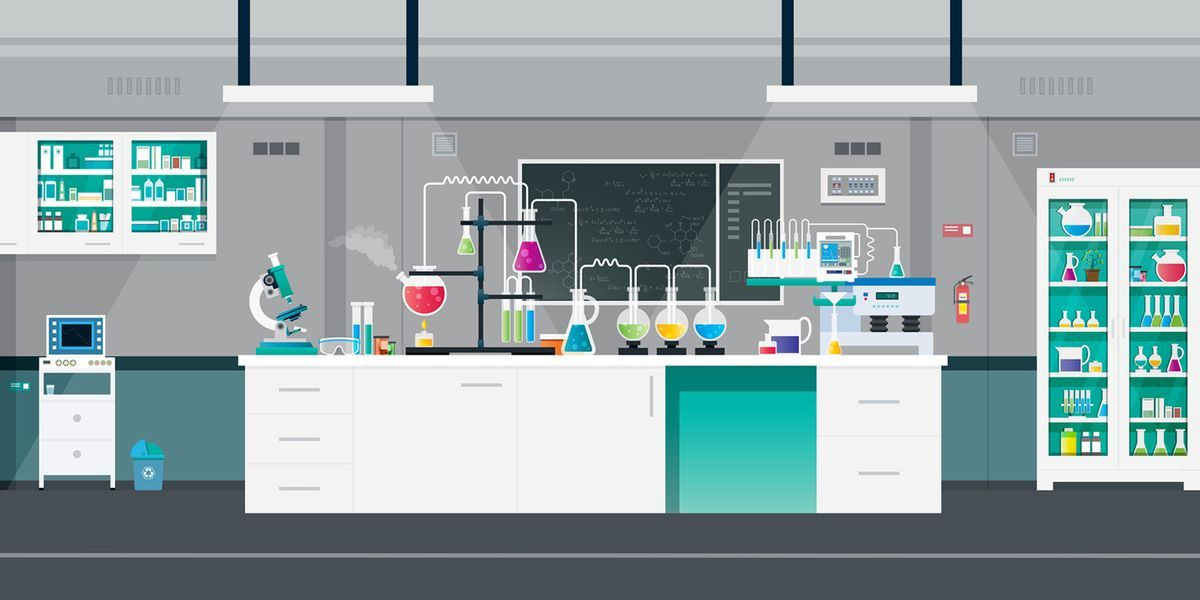
Resolving lab furniture and casework issues
Laboratory furniture and casework play a crucial role in the functionality and safety of any research facility. Over time, these elements can experience wear and tear, leading to various issues. This article offers a comprehensive guide to troubleshooting common problems, covering everything from drawer malfunctions to unstable work surfaces. By understanding the root causes and implementing effective solutions, you can ensure your lab furniture remains in optimal condition, promoting a productive and secure research environment. From identifying potential hazards to optimizing storage solutions, this guide empowers you to address issues proactively and maintain a high standard of laboratory operations.
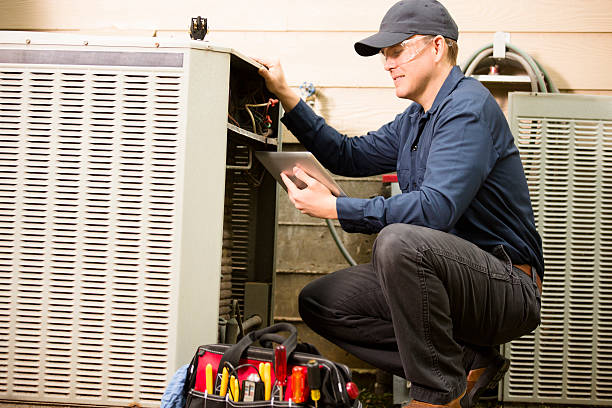
Troubleshooting HVAC system failures
Maintaining a stable and controlled environment is crucial for any laboratory. HVAC systems play a vital role in ensuring optimal conditions for research and experimentation. This article provides a step-by-step guide to troubleshooting common HVAC system failures. We cover identifying potential issues, diagnosing problems, and exploring solutions to restore your lab's HVAC system to optimal performance. From temperature fluctuations to airflow problems, this guide equips you with the knowledge to address HVAC challenges and maintain a reliable lab environment.