Troubleshooting gas leaks and pressure drops
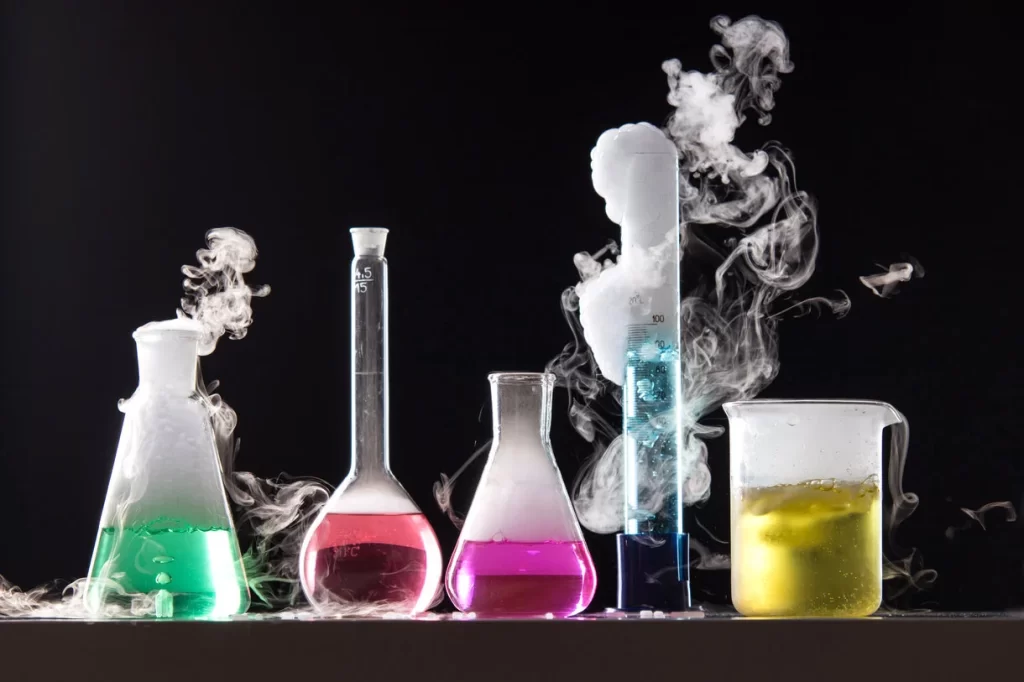
The Silent Saboteurs: Gas Leaks and Pressure Drops in Your Lab
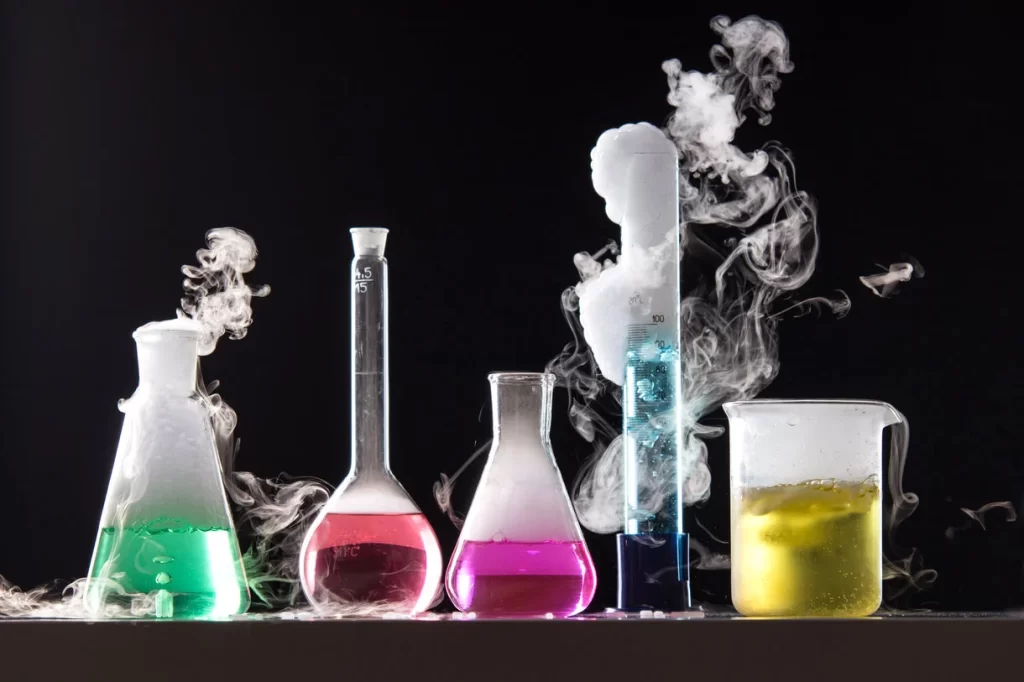
In the intricate world of scientific research, where precision and reliability are paramount, the seamless operation of laboratory equipment is a cornerstone of success. Among the many critical components that underpin this functionality, Gas Piping & Distribution Systems play a pivotal role, delivering the essential gases that fuel countless experiments and analyses. However, these systems, while seemingly invisible, can harbor silent saboteurs – gas leaks and pressure drops – that can wreak havoc on your research endeavors, leading to inaccurate results, compromised safety, and costly downtime.
Imagine a scenario where a seemingly minor gas leak in your chromatography system goes undetected. This seemingly insignificant issue can lead to a cascade of problems. The leak, even if small, can gradually deplete the gas supply, causing pressure fluctuations that disrupt the delicate balance of your analytical process. This can result in inaccurate data, compromised sample integrity, and ultimately, a need to repeat experiments, wasting valuable time and resources. Furthermore, the undetected leak poses a safety hazard, potentially creating an explosive atmosphere if the leaked gas accumulates in an enclosed space.
The impact of pressure drops is equally insidious. A gradual decline in gas pressure can be a subtle indicator of a larger problem within your Gas Piping & Distribution Systems. This pressure drop can affect the performance of sensitive instruments, leading to reduced sensitivity, inaccurate readings, and compromised experimental outcomes. The root cause of the pressure drop could be a clogged regulator, a faulty valve, or even a leak in the system, all of which require prompt attention to prevent further disruption to your research.
The consequences of gas leaks and pressure drops extend beyond the immediate impact on individual experiments. These issues can disrupt entire research projects, delaying timelines, jeopardizing grant funding, and ultimately hindering scientific progress. The financial implications are significant, encompassing the cost of lost research time, equipment repair or replacement, and potential safety incidents. Moreover, the reputational damage caused by unreliable data and compromised research integrity can be long-lasting.
Recognizing the critical importance of maintaining the integrity of your Gas Piping & Distribution Systems, this article delves into the intricacies of troubleshooting gas leaks and pressure drops. We will explore the common causes of these issues, provide practical strategies for identifying and resolving them, and offer valuable insights to prevent future occurrences. By understanding the underlying mechanisms and implementing proactive measures, you can ensure the smooth and reliable operation of your laboratory's gas systems, safeguarding the integrity of your research and maximizing the efficiency of your scientific endeavors.
Maintaining the Integrity of Your Gas Piping & Distribution Systems: A Comprehensive Guide to Troubleshooting Leaks and Pressure Drops
In the realm of scientific research, the reliability of gas delivery systems is paramount. From delicate analytical instruments to critical experimental setups, the precise and consistent flow of gases is essential for accurate results and safe operation. However, the intricate nature of Gas Piping & Distribution Systems can lead to unforeseen challenges, such as leaks and pressure drops, which can disrupt experiments, compromise safety, and incur significant costs.
This comprehensive guide delves into the intricacies of troubleshooting gas leaks and pressure drops, providing a practical framework for identifying the root cause, implementing effective solutions, and ensuring the long-term integrity of your gas delivery systems. We will explore the common culprits behind these issues, ranging from faulty connections and compromised tubing to environmental factors and improper maintenance practices. By understanding the underlying mechanisms and adopting a systematic approach to troubleshooting, you can minimize downtime, enhance operational efficiency, and maintain the highest standards of scientific rigor.
Understanding the Importance of Gas Piping & Distribution Systems
Gas Piping & Distribution Systems serve as the lifeblood of many scientific laboratories, providing a reliable and controlled supply of gases essential for a wide range of applications. These systems are typically designed to deliver gases such as nitrogen, oxygen, helium, argon, and hydrogen, each with specific properties and applications. The integrity of these systems is critical for:
- Ensuring Accurate and Reproducible Results: Precise gas flow rates and pressures are essential for achieving accurate and reproducible results in analytical instruments, such as gas chromatographs, mass spectrometers, and atomic absorption spectrometers. Any fluctuations or inconsistencies in gas delivery can lead to errors in measurements and compromise the validity of research findings.
- Maintaining Safety in the Laboratory: Gas leaks can pose significant safety hazards, potentially leading to explosions, fires, or asphyxiation. Proper maintenance and leak detection are crucial for ensuring a safe working environment for laboratory personnel.
- Optimizing Operational Efficiency: Gas leaks and pressure drops can lead to downtime, interrupting experiments and delaying research progress. By addressing these issues promptly, laboratories can maintain optimal operational efficiency and maximize productivity.
- Reducing Costs: Gas leaks result in wasted gas, leading to increased operating expenses. Regular maintenance and proactive leak detection can help minimize gas consumption and reduce overall costs.
Common Causes of Gas Leaks and Pressure Drops
Gas leaks and pressure drops can arise from a variety of factors, ranging from simple mechanical issues to more complex environmental influences. Understanding the common causes is essential for effective troubleshooting and preventative maintenance.
1. Faulty Connections and Fittings
One of the most common causes of gas leaks is faulty connections and fittings. Over time, connections can become loose, corroded, or damaged, leading to leaks. This is particularly true for older systems or those subjected to frequent handling or vibrations. Common culprits include:
- Loose or Damaged Fittings: Fittings that are not properly tightened or have become damaged can lead to leaks. This can occur due to improper installation, excessive force during tightening, or wear and tear over time.
- Corrosion: Corrosion can weaken fittings and connections, making them more susceptible to leaks. This is particularly common in environments with high humidity or exposure to corrosive chemicals.
- Improper Threading: Mismatched threads or damaged threads can prevent fittings from sealing properly, resulting in leaks.
2. Compromised Tubing
The tubing used in Gas Piping & Distribution Systems can also be a source of leaks and pressure drops. Over time, tubing can become brittle, cracked, or punctured, leading to gas leakage. Factors that can contribute to tubing degradation include:
- Age and Wear: Tubing, especially older tubing, can become brittle and prone to cracking due to age and repeated flexing or bending.
- Chemical Exposure: Exposure to certain chemicals can degrade tubing materials, making them more susceptible to leaks.
- Mechanical Damage: Tubing can be damaged by sharp objects, kinks, or excessive pressure, leading to leaks.
3. Environmental Factors
Environmental factors can also play a role in gas leaks and pressure drops. These factors can influence the integrity of the Gas Piping & Distribution System and create conditions that promote leaks.
- Temperature Fluctuations: Extreme temperature changes can cause expansion and contraction of tubing and fittings, leading to leaks. This is particularly relevant in laboratories with fluctuating temperatures or those located in areas with extreme climates.
- Vibration: Vibration from equipment or nearby machinery can stress tubing and fittings, leading to leaks over time.
- Humidity: High humidity can contribute to corrosion, which can weaken fittings and connections, making them more susceptible to leaks.
4. Improper Maintenance Practices
Neglecting regular maintenance can significantly increase the risk of gas leaks and pressure drops. Proper maintenance practices are essential for identifying and addressing potential issues before they become major problems.
- Insufficient Leak Testing: Regular leak testing is crucial for identifying leaks early on, before they become significant problems. Failure to conduct regular leak tests can allow leaks to develop and worsen, leading to safety hazards and operational disruptions.
- Inadequate Cleaning and Inspection: Regular cleaning and inspection of Gas Piping & Distribution Systems can help identify potential issues, such as corrosion, damage, or debris buildup, before they lead to leaks or pressure drops.
- Improper Handling of Gas Cylinders: Improper handling of gas cylinders, such as dropping or mishandling, can damage valves and fittings, leading to leaks.
Troubleshooting Gas Leaks and Pressure Drops: A Step-by-Step Approach
Troubleshooting gas leaks and pressure drops requires a systematic and methodical approach to identify the root cause and implement effective solutions. The following steps provide a comprehensive framework for addressing these issues:
1. Identify the Leak or Pressure Drop
The first step in troubleshooting is to accurately identify the location and nature of the leak or pressure drop. This can be done through a combination of visual inspection, leak detection equipment, and pressure monitoring.
- Visual Inspection: A visual inspection of the Gas Piping & Distribution System can often reveal obvious signs of leaks, such as bubbles in water or soapy solutions, hissing sounds, or visible gas escaping from fittings or tubing. However, visual inspection may not always be sufficient to detect all leaks, especially those that are small or hidden.
- Leak Detection Equipment: Specialized leak detection equipment, such as electronic leak detectors or soap solution, can be used to identify leaks that are not visible to the naked eye. These devices can detect even small leaks by sensing changes in gas concentration or pressure.
- Pressure Monitoring: Monitoring the pressure in the Gas Piping & Distribution System can help identify pressure drops, which can indicate a leak or blockage. Pressure gauges or pressure transducers can be used to monitor pressure levels and identify any fluctuations or drops.
2. Isolate the Problem Area
Once the leak or pressure drop has been identified, the next step is to isolate the problem area. This involves identifying the specific section of the Gas Piping & Distribution System where the issue is occurring. This can be done by:
- Closing Valves: Closing valves upstream and downstream of the suspected leak area can help isolate the problem and prevent gas from escaping. This allows for a more focused inspection and troubleshooting effort.
- Testing Individual Components: Testing individual components, such as fittings, tubing, or valves, can help pinpoint the source of the leak or pressure drop. This can involve using leak detection equipment or pressure monitoring to assess the integrity of each component.
3. Determine the Cause of the Leak or Pressure Drop
Once the problem area has been isolated, the next step is to determine the underlying cause of the leak or pressure drop. This involves a thorough inspection of the affected components and consideration of potential contributing factors.
- Visual Inspection: A close visual inspection of the affected components can reveal signs of damage, corrosion, or loose connections. This can include checking for cracks, punctures, or signs of wear and tear on tubing, fittings, and valves.
- Testing for Corrosion: If corrosion is suspected, testing for corrosion can help confirm its presence and extent. This can involve using specialized corrosion detection equipment or visual inspection for signs of rust or pitting.
- Checking for Blockages: Blockages in tubing or fittings can also cause pressure drops. Checking for blockages can involve inspecting the tubing for debris or using pressure monitoring to assess flow restrictions.
- Environmental Assessment: Assessing the surrounding environment can help identify potential contributing factors, such as temperature fluctuations, vibration, or humidity, that may be affecting the Gas Piping & Distribution System.
4. Implement Solutions
Once the cause of the leak or pressure drop has been identified, the next step is to implement appropriate solutions. The specific solution will depend on the nature of the problem and the design of the Gas Piping & Distribution System.
- Repair or Replace Damaged Components: Damaged components, such as leaking fittings, cracked tubing, or faulty valves, should be repaired or replaced. This may involve tightening loose fittings, replacing damaged tubing, or installing new valves.
- Address Corrosion: If corrosion is identified, it should be addressed by cleaning the affected components, applying corrosion inhibitors, or replacing corroded components. This can help prevent further corrosion and leaks.
- Remove Blockages: Blockages in tubing or fittings should be removed to restore proper gas flow. This may involve flushing the tubing with compressed air or using specialized tools to remove debris.
- Improve Environmental Conditions: If environmental factors are contributing to leaks or pressure drops, steps should be taken to improve the surrounding environment. This may involve controlling temperature fluctuations, reducing vibration, or controlling humidity levels.
5. Test and Verify the Solution
After implementing a solution, it is essential to test and verify its effectiveness. This involves checking for leaks, monitoring pressure levels, and ensuring that the Gas Piping & Distribution System is functioning properly.
- Leak Testing: Conduct thorough leak testing using leak detection equipment to ensure that the leak has been successfully repaired. This should be done both immediately after the repair and on a regular basis to prevent future leaks.
- Pressure Monitoring: Monitor pressure levels in the Gas Piping & Distribution System to ensure that the pressure is stable and within the desired range. This can help identify any residual leaks or pressure drops that may have been missed during the initial testing.
- Functional Testing: Test the Gas Piping & Distribution System to ensure that it is functioning properly and delivering gas to all connected equipment. This can involve running experiments or using instruments that rely on gas flow to verify that the system is operating as intended.
6. Document the Solution and Implement Preventative Measures
Once the solution has been verified, it is important to document the problem, the solution, and any preventative measures that were implemented. This documentation can help prevent future issues and ensure that the Gas Piping & Distribution System is maintained properly.
- Record the Problem: Document the details of the leak or pressure drop, including the location, the date, and the symptoms observed. This information can be helpful for future troubleshooting and preventative maintenance.
- Record the Solution: Document the solution that was implemented, including the specific repairs or adjustments made. This information can help ensure that the same solution is applied in the future if a similar problem arises.
- Implement Preventative Measures: Implement preventative measures to minimize the risk of future leaks or pressure drops. This may involve establishing a regular maintenance schedule, conducting routine leak testing, and training personnel on proper handling of gas cylinders and equipment.
Best Practices for Maintaining Gas Piping & Distribution Systems
Maintaining the integrity of Gas Piping & Distribution Systems is essential for ensuring safe and reliable operation. The following best practices can help minimize the risk of leaks and pressure drops and ensure the long-term performance of these systems:
1. Regular Maintenance and Inspection
Regular maintenance and inspection are crucial for identifying potential issues before they become major problems. This should include:
- Visual Inspection: Conduct regular visual inspections of the Gas Piping & Distribution System, checking for signs of damage, corrosion, or loose connections. This should be done at least annually, or more frequently if the system is subjected to heavy use or harsh environmental conditions.
- Leak Testing: Conduct regular leak testing using leak detection equipment to identify any leaks, even those that are not visible to the naked eye. The frequency of leak testing should be determined based on the age and usage of the system, but at least annually is recommended.
- Pressure Monitoring: Monitor pressure levels in the Gas Piping & Distribution System to ensure that the pressure is stable and within the desired range. This can help identify any pressure drops that may indicate a leak or blockage.
- Cleaning and Inspection: Regularly clean and inspect the Gas Piping & Distribution System to remove debris, dust, and other contaminants that can contribute to leaks or blockages. This should be done at least annually, or more frequently if the system is located in a dusty or dirty environment.
2. Proper Handling of Gas Cylinders
Proper handling of gas cylinders is essential for preventing leaks and ensuring safety. This includes:
- Secure Storage: Store gas cylinders in a well-ventilated area, away from heat sources and flammable materials. Cylinders should be secured to prevent them from falling or rolling.
- Proper Valve Operation: Always use the correct wrench to open and close gas cylinder valves. Avoid overtightening or damaging the valve.
- Regular Inspection: Regularly inspect gas cylinders for damage, such as dents, cracks, or corrosion. Damaged cylinders should be removed from service and replaced.
3. Training and Education
Training and education are essential for ensuring that laboratory personnel are aware of the potential hazards associated with Gas Piping & Distribution Systems and are equipped to handle these systems safely and effectively. This should include:
- Safety Training: Provide comprehensive safety training to all personnel who work with Gas Piping & Distribution Systems. This training should cover topics such as gas cylinder handling, leak detection, emergency procedures, and personal protective equipment.
- Troubleshooting Training: Train personnel on how to troubleshoot gas leaks and pressure drops, including the steps involved in identifying the problem, isolating the problem area, determining the cause, and implementing solutions.
- Maintenance Training: Train personnel on how to perform routine maintenance and inspection of Gas Piping & Distribution Systems, including leak testing, cleaning, and inspection procedures.
4. Use of High-Quality Materials
Using high-quality materials for Gas Piping & Distribution Systems is essential for ensuring long-term performance and minimizing the risk of leaks. This includes:
- Tubing: Use tubing that is specifically designed for gas delivery and is compatible with the gases being used. Tubing should be made of materials that are resistant to corrosion, chemical degradation, and mechanical damage.
- Fittings: Use high-quality fittings that are properly sized and compatible with the tubing being used. Fittings should be made of materials that are resistant to corrosion and wear and tear.
- Valves: Use valves that are specifically designed for gas delivery and are compatible with the gases being used. Valves should be made of materials that are resistant to corrosion and wear and tear.
5. Regular System Upgrades
Regular system upgrades can help ensure that the Gas Piping & Distribution System is up-to-date and meets current safety and performance standards. This may involve replacing outdated components, upgrading to newer materials, or implementing new technologies to enhance safety and efficiency.
By implementing these best practices, laboratories can significantly reduce the risk of gas leaks and pressure drops, ensuring the safe and reliable operation of their Gas Piping & Distribution Systems. This will contribute to a safer working environment, enhance operational efficiency, and maintain the highest standards of scientific rigor.
Preventative Maintenance: The Cornerstone of Gas System Integrity
The importance of preventative maintenance in ensuring the longevity and reliability of your laboratory's gas systems cannot be overstated. Regular inspections, testing, and proactive repairs are the cornerstones of a robust and safe gas infrastructure. By embracing a culture of preventative maintenance, you can significantly reduce the risk of costly downtime, safety hazards, and compromised research outcomes.
The benefits of preventative maintenance extend far beyond simply avoiding catastrophic failures. Regular inspections allow for the early detection of minor issues, such as leaks, pressure drops, and component wear, before they escalate into major problems. This proactive approach not only minimizes downtime but also helps to extend the lifespan of your gas systems, saving you money in the long run.
Furthermore, preventative maintenance plays a crucial role in ensuring the safety of your laboratory environment. Gas leaks can pose serious health risks, and pressure drops can disrupt sensitive experiments. By identifying and addressing potential hazards early on, you can create a safer and more reliable working environment for your staff.
In addition to the practical benefits, preventative maintenance also demonstrates a commitment to quality and professionalism. By investing in the upkeep of your gas systems, you signal to your stakeholders, including funding agencies, collaborators, and the scientific community, that you prioritize accuracy, reliability, and safety in your research endeavors.
Navigating the Labyrinth of Gas Piping & Distribution Systems
The complexity of modern laboratory gas systems can be daunting, with intricate networks of pipes, regulators, valves, and other components. Understanding the intricacies of these systems is essential for effective troubleshooting and preventative maintenance. IT Tech, with its deep expertise in Gas Piping & Distribution Systems, can be your trusted partner in navigating this labyrinth.
Our team of experienced engineers and technicians possesses a comprehensive understanding of the various components and functionalities of gas systems. We offer a wide range of services, including:
- Comprehensive Gas System Audits: Our expert audits provide a thorough assessment of your existing gas infrastructure, identifying potential vulnerabilities and recommending corrective actions.
- Leak Detection and Repair: We utilize state-of-the-art leak detection technologies to pinpoint even the smallest leaks, ensuring the safety and integrity of your gas systems.
- Pressure Testing and Calibration: Regular pressure testing and calibration of your gas system components are crucial for maintaining optimal performance and safety.
- Gas System Design and Installation: From initial planning to final installation, IT Tech provides comprehensive design and installation services for new gas systems, ensuring compliance with industry standards and your specific requirements.
- Gas System Maintenance and Repair: We offer comprehensive maintenance and repair services, including routine inspections, component replacement, and emergency repairs.
By partnering with IT Tech, you gain access to a wealth of knowledge and expertise in Gas Piping & Distribution Systems. We are committed to providing you with the highest quality services and products, ensuring the smooth operation and safety of your laboratory's gas infrastructure.
A Call to Action: Partner with IT Tech for a Secure Gas Future
Don't wait for a gas leak or pressure drop to disrupt your research or compromise safety. Take proactive steps to ensure the reliability and integrity of your laboratory's gas systems. Contact IT Tech today to schedule a comprehensive gas system audit or discuss your specific needs. Our team of experts is ready to assist you in creating a secure and efficient gas infrastructure for your laboratory.
Submit an enquiry today and let IT Tech be your trusted partner in safeguarding your laboratory's gas systems.
Subscribe to our newsletter
Stay updated with IT-Tech Insights
Related posts
Check out other IT- Tech Scientific Resources
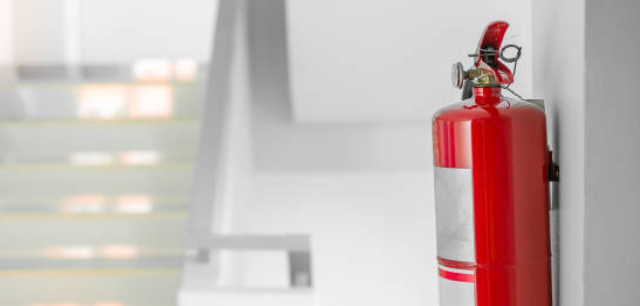
Gaseous vs water-based fire extinguishing
Choosing the right fire extinguishing system is crucial for research labs. This article delves into the distinct characteristics of gaseous and water-based systems. Gaseous systems, like CO2 or inert gas, are ideal for sensitive equipment and electronics, while water-based systems are effective for general fires. We discuss the advantages and disadvantages of each, including their impact on lab environments and the types of fires they are best suited for. By understanding these differences, researchers can make informed decisions about the most appropriate fire safety measures for their specific needs.
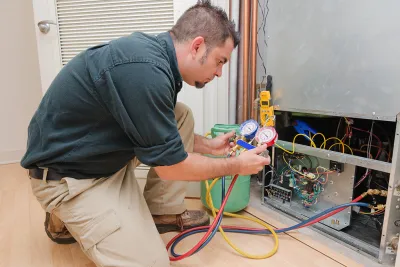
Optimizing HVAC maintenance and monitoring
This training module delves into the critical aspects of HVAC maintenance and monitoring. You'll gain insights into preventative maintenance schedules, troubleshooting common HVAC issues, and utilizing advanced monitoring technologies. By understanding these concepts, you can ensure your HVAC systems operate at peak efficiency, minimize downtime, and extend their lifespan. This module is designed to equip you with the knowledge and skills to effectively manage your HVAC systems and optimize their performance.
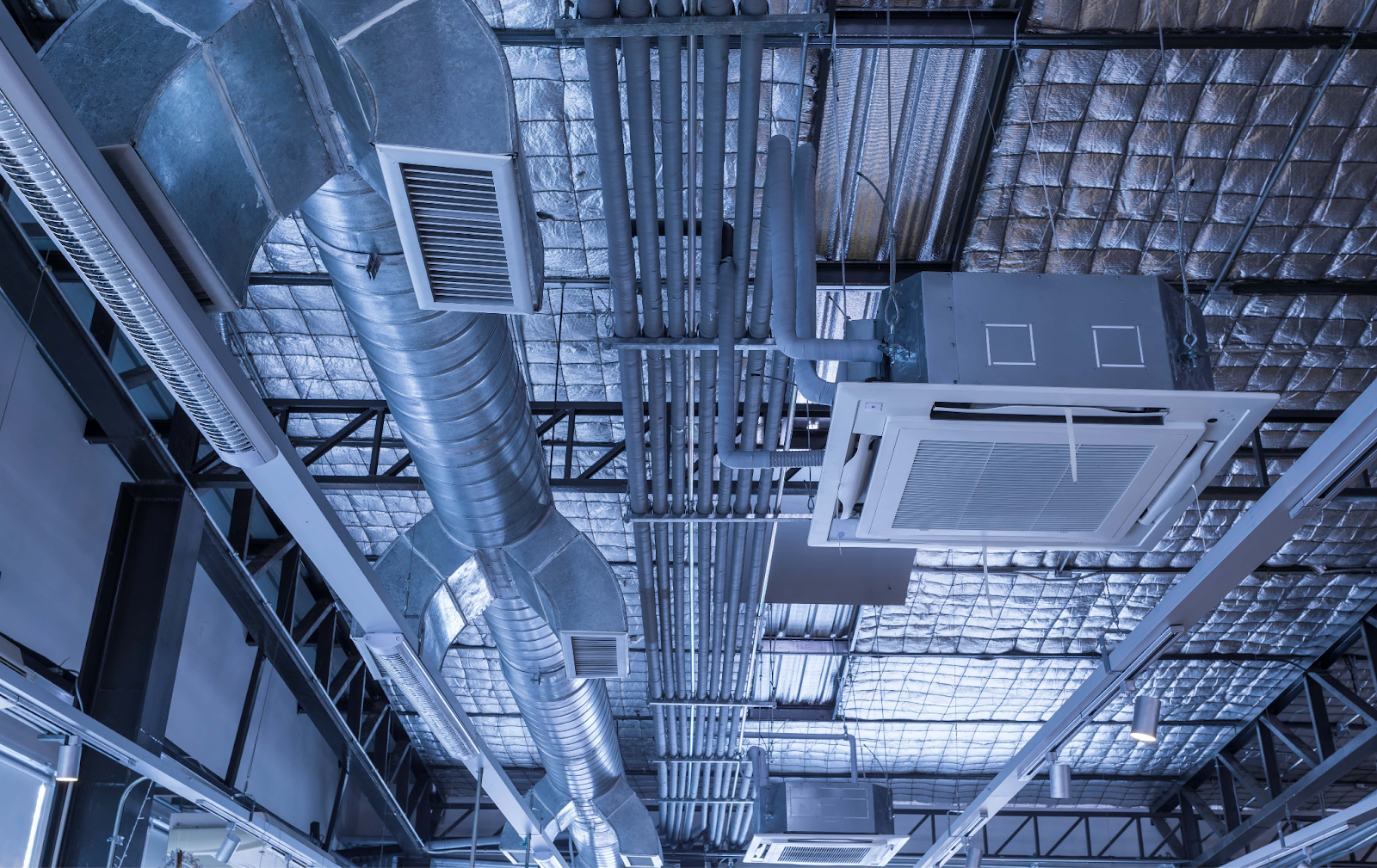
Choosing HVAC controls for lab environments
Maintaining a controlled environment is essential for research labs. HVAC systems play a critical role in regulating temperature, humidity, and air quality, impacting experiment accuracy and safety. This article guides you through key considerations when selecting HVAC controls for your lab. Factors like lab size, equipment sensitivity, and budget are crucial. We explore different HVAC system types, including VAV systems, fan coil units, and dedicated outdoor air systems, highlighting their advantages and disadvantages. By understanding these factors, you can choose the most suitable HVAC system to ensure optimal lab conditions and support your research endeavors.