Driving Innovation: Key Bioreactor & Fermentor Advancements and Applications
.png)
As biopharmaceutical pipelines accelerate rapidly, having optimal bioreactor and fermentor systems in place proves vital. These cultivation devices enable creating precisely controlled environments nurturing cells to achieve consistent growth and biologic production. However, selecting the right technologies spanning hardware, sensors, and process analytical solutions can get overwhelming.
This blog offers insightful guidance on key advancements and latest applications of bioreactors and fermentors. It details how leading technologies, functionality innovations, and usage best practices empower scientists. Equipped with this knowledge, research and bioprocess experts can confidently determine equipment investments delivering maximum value.
Essential Attributes of Premier Bioreactor & Fermentor Platforms
As advanced therapeutic pipelines continue accelerating rapidly, having optimal bioreactor and fermentor systems underpinning upstream development and manufacturiing processes proves vital. However, not all bioreactors and fermentors provide equal performance and capabilities. Premier platforms share essential attributes and innovations enabling smooth, efficient translation of discoveries through clinical advancement and ultimately to widespread patient impact including:
Precisely Regulated Incubation
Maintaining rigorous environmental control is fundamental for bioreactor success across applications. Modern bioreactors systems like the Thermo Scientific HyPerforma SUB incorporate thermal jackets and probes enabling precise, uniform temperature control within ±0.1°C. Automated sensors also tightly regulate dissolved oxygen, pH, and carbon dioxide levels through feedback loops to match cell culture needs whether growing CHO cells or optimizing microbial fermentations. This prevents deviations compromising cell health and product quality.
Enhanced Analytical Capabilities
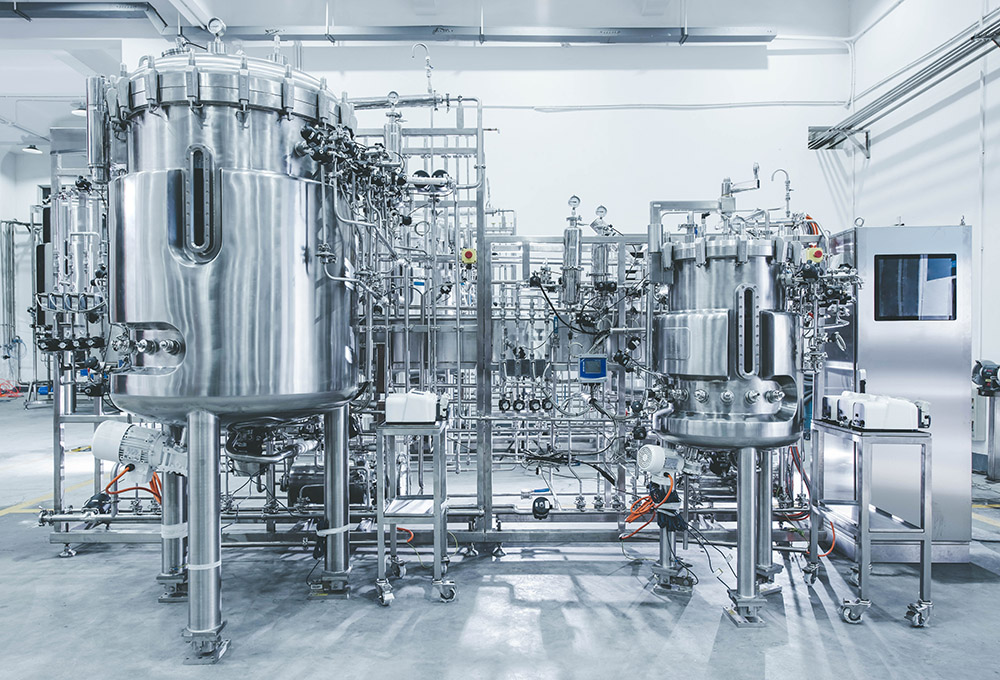
Real-time data visibility via enhanced analytical capabilities is vital for tight process control. Innovations like the Finesse G3Lab Universal Controller offer input/output flexibility to incorporate an array of external sensors while integrating seamlessly with software platforms like Thermo's TruBio DV for centralized monitoring. This enables granular tracking of multiple parameters with auto-tunable control loops balancing temperature, pH, dissolved oxygen, redox, glucose and gas flows catered to each cell culture's needs. Data-informed automatic feeding further stabilizes processes.
Production Scalability from Pilot through Manufacturing
Scalable bioreactor platforms enable seamless transfers between process development and commercial production to maximize return on investment. Best-in-class equipment like Sartorius Stedim’s BIOSTAT STR single-use bioreactors satisfy small pilot-scale batches with the same cGMP-compliant film technology used up to the 2,000L production scale. Similarly, Danaher’s Xcellerex XDR cell culture bioreactors range from 10L to 10,000L using single-use or stainless-steel options with comparable engineering controls and component sourcing suitable for global regulatory filings.
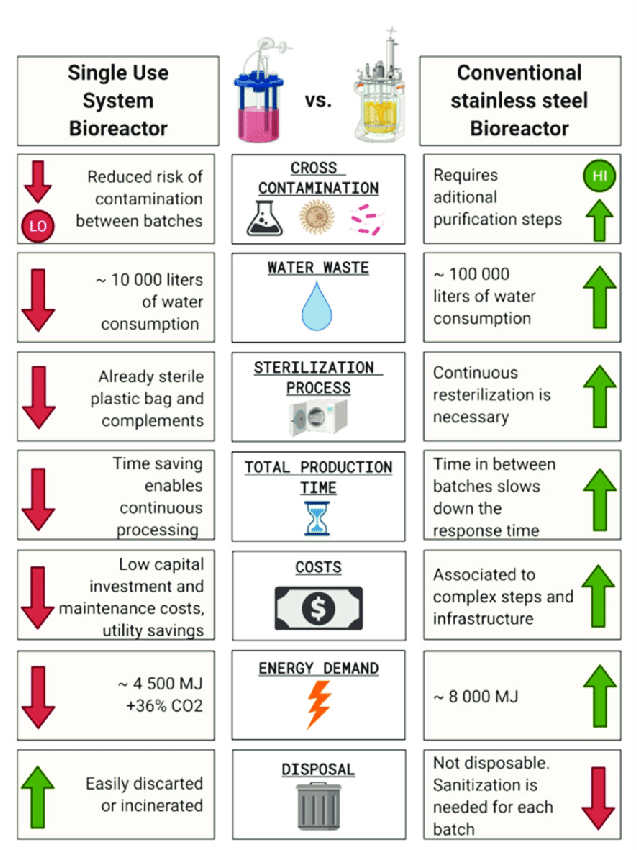
Identifying bioreactor and fermentor solutions aligning on flexibility, analytics, and scalability establishes an optimized technology foundation for accelerating pipelines from discovery through therapeutic production. Consult with process experts early when evaluating options.
Trends and Innovations Advancing Bioreactor & Fermentor Performance
In addition to environmental control and analytical capabilities, supplementary functionality innovations around single-use systems, continuous processing, and enhanced data analytics further augment bioreactor and fermentor solutions unlocking greater efficiency.
Single-Use Pre-Sterilized Configurations
Pre-sterilized, single-use bioreactors utilizing disposable plastic bags and tubing assemblies eliminate time-intensive cleaning validation between batches. The Thermo Scientific HyPerforma S.U.B. range with HyPerforma G3 film technology simplifies changeovers enabling rapid lot-to-lot bioreactor replacements at up to 2,000L scale. GE Healthcare’s FlexFactory line likewise offers preset single-use container and sensor options up to 1,500L for turnkey batch-to-batch consistency.
Continuous Perfusion Processing
Transitioning from peak-limited fed-batch processes, continuous perfusion bioreactors sustain extremely high cell densities through constant filtered feeding over weeks-long durations. MilliporeSigma’s UniVessel SU 2L single-use bioreactor incorporates biomass retention filters enabling reliable low-shear perfusions. Among stainless options, Eppendorf’s BioBLU c 14c/19c systems integrate viability chips or overflow harvest tubes for automated closed-loop cell bleeding and media replenishments.
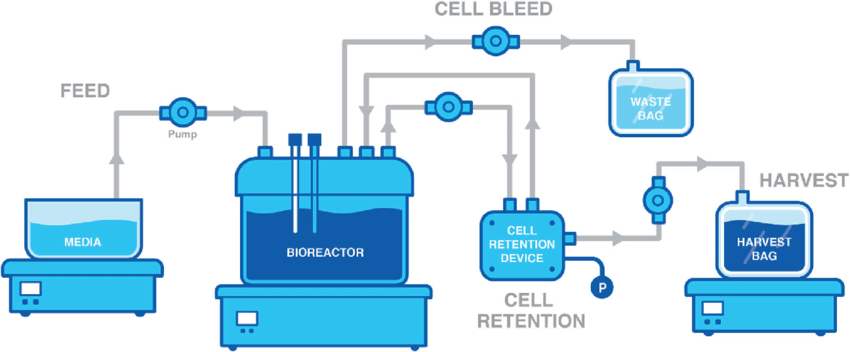
Advanced Analytics and Process Automation
Collating real-time data-informed process adjustments prevents disruptions through tighter control. Thermo Fisher’s TruBio DV software condenses indicators from multiple bioreactors into centralized dashboards aiding troubleshooting. Meanwhile Merck’s Bio4 bioprocess controls automate monitoring, adding feeds, regulating gases to stabilize cultures. Specialty sensors like Hamilton’s VisiFerm DO probe and Finesse’s Trk inline glucose analyzer provide analytical rigor while preventing media interactions.
Leveraging these supplemental capabilities expands bioprocess possibilities across applications and scales. Consult our experts on innovations suiting your needs.
Functionality Innovations Expanding Bioreactor & Fermentor Applications
Beyond reliable microbial cultures and common CHO workflows for antibodies, growth factors and vaccines, today’s bioreactor platforms drive breakthroughs across novel modalities and cell types.
Optimized for Continuous Perfusion Cultures
Continuous perfusion bioreactors utilize filters or cell retention devices to enable prolonged high-density cultures. Cells and media flow continuously through the system while the bioreactor retains cells, allowing for constant nutrient feeding and waste removal. This avoids peak harvest limitations of fed-batch processes. The Xcellerex XDR stirred tank system from Danaher offers automated cell retention control and sensors to sustain extremely high viable cell densities over extended periods. Some perfusion systems can achieve over 50-fold increases in product titers compared to fed-batch.
High-Efficiency Gene Therapy Vector Production
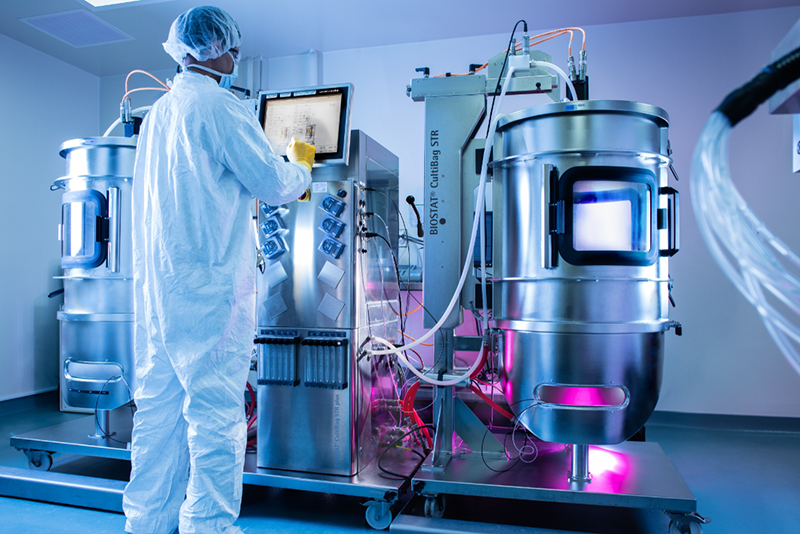
Gene therapies using viral vectors like lentiviruses and adeno-associated viruses (AAVs) can deliver corrected genes to counter genetic disorders. However, scaling fragile HEK293 or suspension cultures of these viruses requires tailored systems. Thermo Fisher's GibcoTM CTS DynaDrive Culture System provides single-use bioreactors up to 50L under tightened control of feeding, gas, and pH for uniform growth. Advanced features like the Dynamix disposable impeller mixer prevent shear stress on cells. Optimized for adenovirus or AAV yields exceeding 1x10^15 vector genomes/mL, this enhances scale-up efficiency.
Algae and Plant Cell Photobioreactors
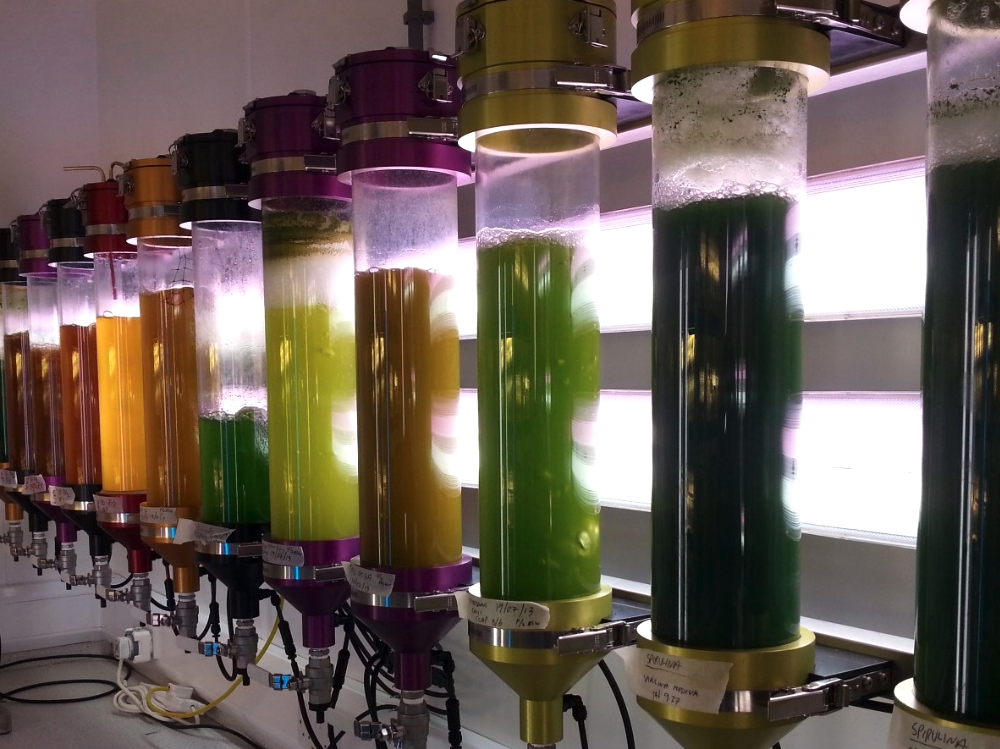
In addition to biopharma applications, photobioreactors equipped with LED lighting panels enable cultivation of photosynthetic algae and plant cells as renewable sources for biofuels, nutrients, and high-value botanical compounds. Tailored features like internal illumination and gas exchange optimize growth. The Applikon luminostat provides precise recipe-driven light and temperature cycling to simulate day-night rhythms for plant cell cultures.
Primary Human Cell Harvests
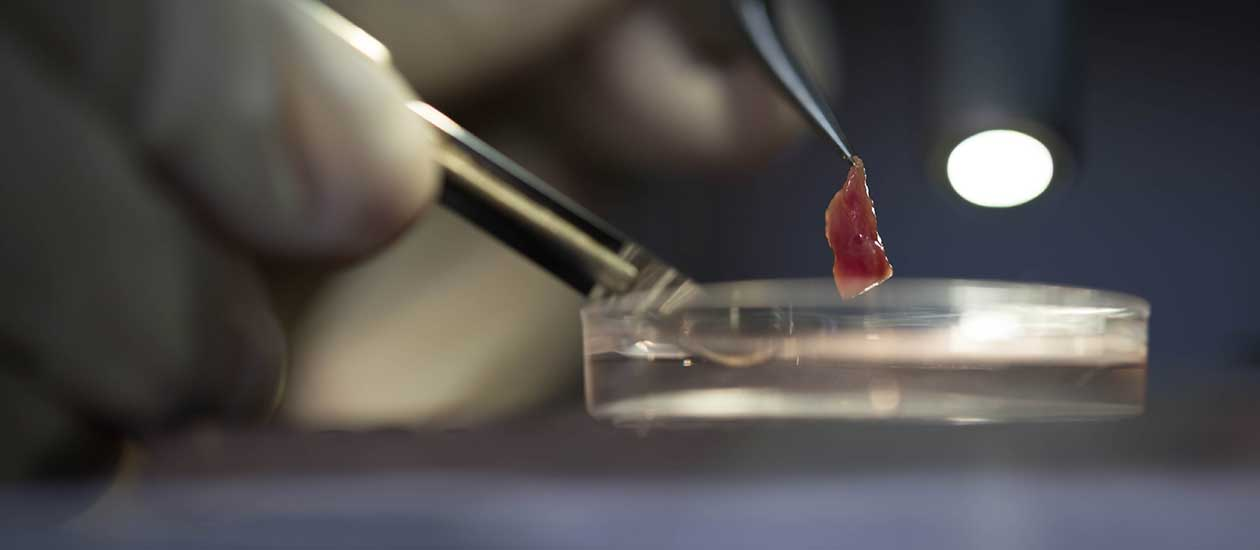
Transitioning from standardized cell lines to patient-derived primary cells can enable more personalized therapies. However, primary cells have more complex nutritional demands. Small-scale automated perfusion bioreactors like the Thermo Scientific Microcarrier Bioreactor provide fine-tuned nutrient feeding alongside microcarriers for cell adherence to retain viability and potency. As innovations continue, tailored bioreactor platforms will become vital to translate patient-specific harvests into commercial scale.
Conclusion and Next Steps
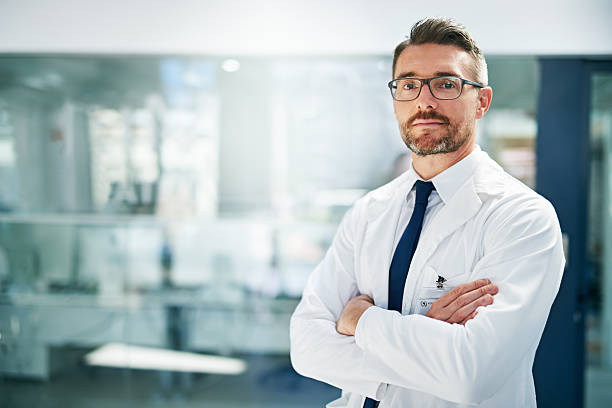
This guide has explored several major technology drivers spurring impactful innovations in bioreactor and fermentor systems, including single-use configurations eliminating cleaning validation needs, continuous processing capabilities enabling prolonged high-density perfusions, enhanced bioanalytic monitoring, and expanded applications encompassing gene therapies, algae, and primary cell harvests.
As pipelines accelerate across novel modalities, having optimal upstream development and manufacturing platforms in place proves vital. However, selecting the ideal bioreactor hardware, sensors, and process controls can become a complex undertaking needing to balance immediate functionality demands against future scalability goals.
Fortunately, working with an experienced solutions provider can simplify your decision journey. The bioprocess consultants at IT Tech offer complimentary, application-specific technical and economic guidance based on your specific cell types, modalities, and projected production needs over upcoming years. We partner closely with global bioreactor manufacturers and can advise on flexible procurement options spanning outright capital purchases, reagent rentals, clinical trial services, and process development collaborations.
Whether needing process improvements for existing pipelines or planning capacity expansions and new facility builds, reach out to speak with our team. We facilitate creating comprehensive bioprocess roadmaps incorporating the latest innovations that translate discoveries efficiently and economically into broad patient impact. Let us help determine the ideal options fitting current priorities and future manufacturing goals.
Subscribe to our newsletter
Stay updated with IT-Tech Insights
Related posts
Check out other IT- Tech Scientific Resources
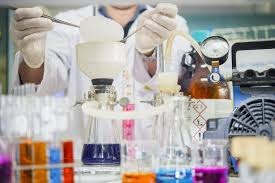
Selecting CRMs for your analytical method
Selecting the right CRMs (Certified Reference Materials) is a critical step in establishing a robust analytical method. This article provides insights into key factors to consider when choosing CRMs, including purity, traceability, and suitability for your specific application. Understanding the role of CRMs in quality control and method validation is essential for achieving accurate and reliable results. We discuss the importance of selecting CRMs from reputable suppliers who adhere to strict quality standards and provide comprehensive documentation. By carefully considering these factors, you can ensure that your chosen CRMs meet your specific needs and contribute to the overall success of your analytical workflow.
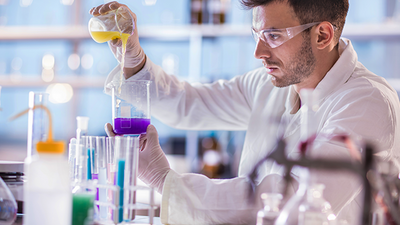
Multi-component standard mixes vs single standards
When conducting research, accurate calibration and validation are crucial. This often involves using chemical standards or certified reference materials (CRMs). Two common approaches are multi-component standard mixes and single standards. Multi-component mixes offer convenience and cost-effectiveness, while single standards provide greater flexibility and control. This article delves into the advantages and disadvantages of each approach, helping you determine the best option for your specific research needs. We discuss factors such as accuracy, traceability, and cost, providing insights to ensure reliable and accurate results in your experiments.
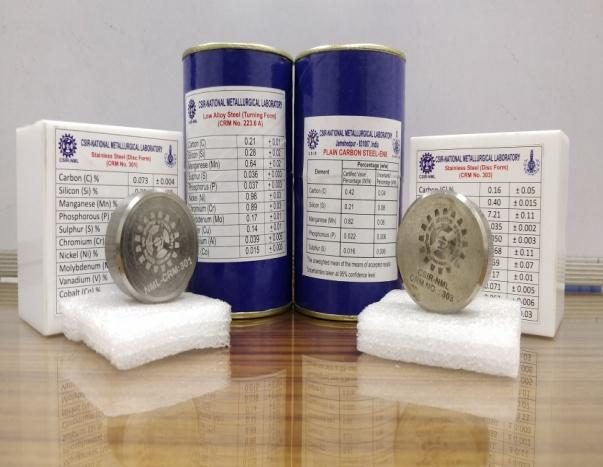
Understanding certified reference materials (CRMs)
Certified reference materials (CRMs) are highly characterized materials with known and certified properties. They play a crucial role in analytical chemistry by providing a reference point for calibrating instruments, validating analytical methods, and ensuring the accuracy of measurements. CRMs are essential for quality control, research, and regulatory compliance. This article explores the importance of CRMs, their different types, and how they contribute to reliable and accurate analytical results. Discover how IT tech can provide you with a comprehensive range of Chemical Standards & CRMs to meet your specific needs.