HVAC installation and commissioning protocols
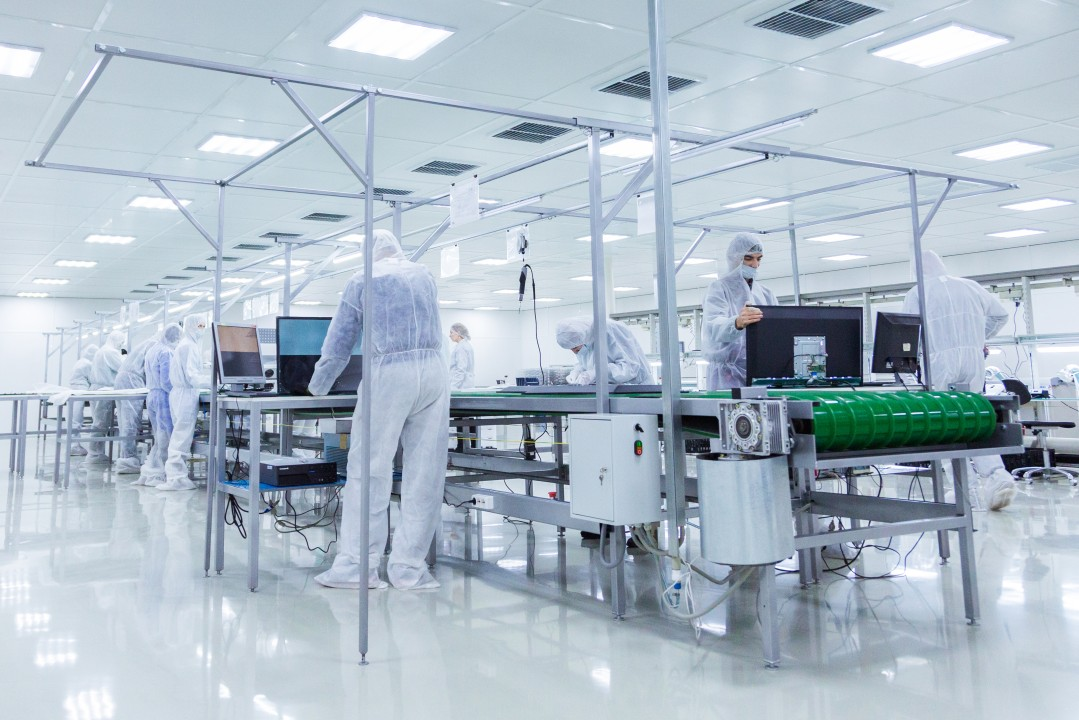
The Critical Role of HVAC Systems in Laboratory Environments
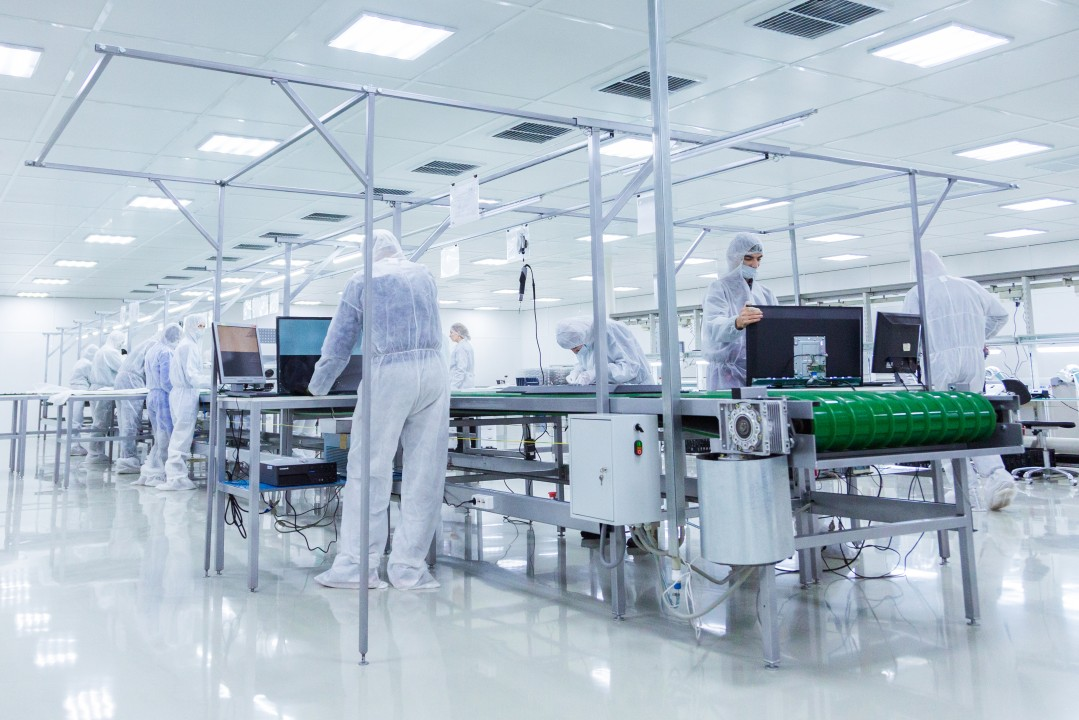
The scientific community relies heavily on laboratories to conduct research, develop new technologies, and advance our understanding of the world. These laboratories are complex environments that require precise control over various parameters, including temperature, humidity, air quality, and pressure. Maintaining these parameters within strict tolerances is crucial for ensuring the accuracy and reliability of experimental results, the safety of personnel, and the integrity of valuable samples and equipment.
One of the most critical factors influencing the performance and functionality of a laboratory is the **HVAC system**. HVAC stands for Heating, Ventilation, and Air Conditioning, and it encompasses the technology and processes involved in controlling the temperature, humidity, and air quality within a building. In the context of laboratories, HVAC systems play a vital role in creating and maintaining the controlled environments necessary for scientific research and development.
The importance of properly designed and maintained HVAC systems in laboratories cannot be overstated. These systems directly impact the accuracy and reproducibility of experiments, the safety of researchers, and the longevity and performance of sensitive equipment.
For instance, in a pharmaceutical laboratory, maintaining a consistent temperature and humidity level is essential for ensuring the stability and efficacy of drug formulations. Similarly, in a microbiology laboratory, controlling airflow and air quality is crucial for preventing contamination and ensuring the safety of researchers working with potentially hazardous microorganisms.
The complexity of laboratory operations and the stringent requirements for environmental control necessitate a comprehensive understanding of HVAC systems and their impact on laboratory performance. This understanding is essential for laboratory managers, project managers, procurement professionals, and even C-suite executives who are responsible for making decisions about laboratory infrastructure and operations.
This article delves into the critical aspects of HVAC installation and commissioning protocols in laboratory settings. We will explore the key considerations for designing and implementing HVAC systems that meet the specific needs of different types of laboratories. We will also discuss the importance of proper commissioning and ongoing maintenance to ensure optimal performance and reliability of these systems.
By understanding the intricacies of HVAC systems in laboratories, stakeholders can make informed decisions that optimize laboratory performance, enhance research outcomes, and ensure the safety and well-being of personnel.
HVAC Installation and Commissioning Protocols: A Comprehensive Guide for Laboratory Environments
The efficient operation of a laboratory hinges on a multitude of factors, with the HVAC system playing a pivotal role in ensuring optimal conditions for research, testing, and analysis. A well-designed and meticulously installed HVAC system is not merely a matter of comfort but a critical component in maintaining the integrity of experiments, safeguarding sensitive equipment, and protecting the health and safety of personnel. This comprehensive guide delves into the intricacies of HVAC installation and commissioning protocols specifically tailored for laboratory environments, providing a roadmap for achieving optimal performance and compliance with industry standards.
Understanding the Importance of HVAC in Laboratories
Laboratories, by their very nature, demand a controlled environment to ensure the accuracy and reliability of scientific endeavors. The HVAC system serves as the cornerstone of this control, regulating temperature, humidity, air pressure, and air quality. These parameters are not merely arbitrary values but are meticulously chosen to meet the specific requirements of the experiments conducted within the lab. For instance, a microbiology lab might require a tightly controlled temperature and humidity to prevent the growth of unwanted microorganisms, while a chemistry lab might necessitate a specific air pressure to minimize the risk of hazardous fumes escaping. The HVAC system's role extends beyond maintaining these parameters; it also plays a crucial role in safeguarding sensitive equipment, preventing the spread of contaminants, and ensuring the well-being of lab personnel.
The importance of a properly functioning HVAC system in a laboratory cannot be overstated. A malfunctioning system can lead to a cascade of negative consequences, including:
- Compromised Experiment Results: Fluctuations in temperature, humidity, or air pressure can significantly impact the accuracy and reproducibility of experiments, leading to unreliable data and potentially invalidating research findings.
- Equipment Damage: Sensitive laboratory equipment, such as microscopes, analytical instruments, and computers, can be susceptible to damage from extreme temperatures, humidity, or dust. A malfunctioning HVAC system can expose these instruments to adverse conditions, leading to costly repairs or replacements.
- Health and Safety Risks: Poor air quality, inadequate ventilation, or uncontrolled temperature and humidity can pose health risks to lab personnel, leading to respiratory problems, allergies, or even more serious health complications.
- Compliance Issues: Many laboratories operate under strict regulatory guidelines, such as those set by the Occupational Safety and Health Administration (OSHA) or the Environmental Protection Agency (EPA). A malfunctioning HVAC system can lead to non-compliance with these regulations, resulting in fines, penalties, or even the suspension of research activities.
The HVAC Installation Process: A Step-by-Step Guide
The installation of an HVAC system in a laboratory is a complex process that requires careful planning, meticulous execution, and adherence to industry best practices. The following steps outline the key stages involved in the installation process:
1. Needs Assessment and Design
The first step in the HVAC installation process is a comprehensive needs assessment. This involves a thorough understanding of the laboratory's specific requirements, including:
- Types of Experiments: The types of experiments conducted in the lab will dictate the specific environmental parameters that need to be controlled, such as temperature, humidity, air pressure, and air quality.
- Equipment Requirements: The equipment used in the lab, including sensitive instruments, computers, and storage systems, will have specific environmental requirements that need to be considered.
- Space Layout: The layout of the lab, including the location of equipment, workstations, and ventilation systems, will influence the design and placement of the HVAC system.
- Building Codes and Regulations: The HVAC system must comply with all applicable building codes and regulations, including those related to energy efficiency, safety, and environmental protection.
Based on the needs assessment, a detailed HVAC design is developed. This design will specify the type of HVAC system, the capacity of the equipment, the layout of the ductwork, and the control systems that will be used. The design should be reviewed and approved by qualified engineers and architects to ensure its feasibility and compliance with industry standards.
2. Equipment Selection and Procurement
Once the HVAC design is finalized, the next step is to select and procure the necessary equipment. This includes:
- Air Handling Units (AHUs): AHUs are the central components of the HVAC system, responsible for conditioning the air by heating, cooling, humidifying, or dehumidifying it. The type and capacity of the AHU will depend on the specific requirements of the lab.
- Chillers: Chillers are used to provide cooling water to the AHU, which in turn cools the air. The size and type of chiller will depend on the cooling load of the lab.
- Boilers: Boilers are used to provide hot water to the AHU, which in turn heats the air. The size and type of boiler will depend on the heating load of the lab.
- Ductwork: Ductwork is used to distribute conditioned air throughout the lab. The type and size of ductwork will depend on the layout of the lab and the airflow requirements.
- Filters: Filters are used to remove dust, particles, and other contaminants from the air. The type and efficiency of the filters will depend on the specific requirements of the lab.
- Control Systems: Control systems are used to monitor and regulate the operation of the HVAC system. These systems can be simple thermostats or more sophisticated building management systems (BMS) that can control multiple HVAC components and optimize energy efficiency.
The selection of equipment should be based on factors such as energy efficiency, reliability, noise levels, and compatibility with the existing building infrastructure. It is essential to work with reputable suppliers who can provide high-quality equipment and technical support.
3. Installation and Commissioning
The installation of the HVAC system is a critical phase that requires skilled technicians and adherence to strict safety protocols. The following steps are typically involved in the installation process:
- Site Preparation: The installation site must be properly prepared, including the removal of any obstructions, the installation of support structures, and the provision of access for equipment and technicians.
- Equipment Installation: The HVAC equipment, including the AHU, chiller, boiler, and ductwork, is installed according to the design specifications. This process involves careful handling of the equipment, proper connections, and adherence to safety regulations.
- Ductwork Installation: The ductwork is installed to distribute conditioned air throughout the lab. This involves careful routing of the ductwork, proper sealing, and insulation to minimize air leakage and noise levels.
- Control System Installation: The control system is installed and configured to monitor and regulate the operation of the HVAC system. This involves wiring the control system to the HVAC equipment, programming the control logic, and testing the system's functionality.
- Commissioning: Commissioning is the process of verifying that the installed HVAC system meets the design specifications and operates as intended. This involves a series of tests and adjustments to ensure that the system is properly balanced, controls are functioning correctly, and the desired environmental parameters are achieved.
The commissioning process is crucial for ensuring the optimal performance of the HVAC system. It involves a series of tests and adjustments to ensure that the system is properly balanced, controls are functioning correctly, and the desired environmental parameters are achieved. A qualified commissioning agent should be involved in this process to ensure that the system meets the required standards.
HVAC Commissioning Protocols: Ensuring Optimal Performance
HVAC commissioning is a comprehensive process that goes beyond simply turning on the system and verifying that it is operational. It involves a series of tests and adjustments to ensure that the system is properly balanced, controls are functioning correctly, and the desired environmental parameters are achieved. The commissioning process is crucial for ensuring the optimal performance of the HVAC system and achieving the desired environmental conditions in the laboratory.
1. Pre-Commissioning Inspection
Before the HVAC system is commissioned, a thorough pre-commissioning inspection should be conducted. This inspection involves verifying that the installed equipment meets the design specifications, that all connections are properly made, and that the system is ready for testing. The following aspects should be checked during the pre-commissioning inspection:
- Equipment Verification: Verify that all HVAC equipment, including the AHU, chiller, boiler, ductwork, and control system, is installed according to the design specifications and meets the required standards.
- Connections and Wiring: Inspect all connections and wiring to ensure that they are properly made and secure. This includes connections between the HVAC equipment, the control system, and the power supply.
- Safety Systems: Verify that all safety systems, such as fire alarms, smoke detectors, and emergency ventilation systems, are properly installed and functioning correctly.
- Documentation: Review all installation documentation, including drawings, specifications, and test reports, to ensure that they are complete and accurate.
The pre-commissioning inspection is a critical step in the commissioning process, as it helps to identify any potential problems before the system is put into operation. Addressing any issues identified during this inspection can prevent delays and costly repairs later on.
2. Functional Testing
Once the pre-commissioning inspection is complete, the HVAC system can be subjected to functional testing. This involves testing the operation of each component of the system to ensure that it is functioning correctly. The following tests are typically performed during functional testing:
- Airflow Testing: Measure the airflow through the ductwork and verify that it meets the design specifications. This involves using an anemometer to measure the air velocity at various points in the ductwork.
- Temperature and Humidity Testing: Measure the temperature and humidity at various points in the lab and verify that they meet the design specifications. This involves using calibrated thermometers and hygrometers.
- Air Pressure Testing: Measure the air pressure in the lab and verify that it meets the design specifications. This involves using a manometer to measure the pressure difference between the lab and the outside air.
- Control System Testing: Test the operation of the control system, including the thermostats, humidistats, and other control devices. This involves setting the control points and verifying that the system responds correctly to changes in the environmental parameters.
- Filter Performance Testing: Test the performance of the air filters to ensure that they are effectively removing dust, particles, and other contaminants from the air. This involves using a particle counter to measure the concentration of airborne particles before and after the filters.
Functional testing is essential for identifying any problems with the HVAC system before it is put into full operation. Addressing any issues identified during this testing can prevent costly repairs and ensure that the system is operating efficiently and effectively.
3. Balancing and Fine-Tuning
After functional testing is complete, the HVAC system may need to be balanced and fine-tuned to achieve the desired environmental parameters. Balancing involves adjusting the airflow through the ductwork to ensure that each room or zone in the lab receives the correct amount of conditioned air. Fine-tuning involves adjusting the control system settings to optimize the performance of the HVAC system and achieve the desired temperature, humidity, and air pressure levels.
Balancing and fine-tuning are iterative processes that may require multiple adjustments to achieve the desired results. A qualified commissioning agent should be involved in this process to ensure that the system is properly balanced and fine-tuned.
4. Documentation and Training
Once the HVAC system is commissioned, it is essential to document the commissioning process and provide training to the lab personnel. The documentation should include the following information:
- Commissioning Report: A detailed report outlining the commissioning process, including the tests performed, the results obtained, and any adjustments made to the system.
- Operating Manual: A comprehensive manual that provides instructions on how to operate and maintain the HVAC system, including information on troubleshooting common problems.
- Control System Documentation: Documentation on the control system, including the programming logic, operating procedures, and troubleshooting guides.
Training should be provided to lab personnel on the operation and maintenance of the HVAC system, including how to monitor the system's performance, identify potential problems, and respond to emergencies. This training should be conducted by qualified technicians who are familiar with the specific HVAC system installed in the lab.
HVAC System Maintenance: A Key to Long-Term Performance
A properly installed and commissioned HVAC system is only the first step in ensuring optimal performance. Regular maintenance is essential for keeping the system operating efficiently and effectively over the long term. A comprehensive maintenance program should include the following tasks:
1. Routine Inspections
Regular inspections of the HVAC system should be conducted to identify any potential problems before they become serious. These inspections should include the following:
- Visual Inspection: Inspect the HVAC equipment, including the AHU, chiller, boiler, ductwork, and control system, for any signs of damage, corrosion, or leaks.
- Filter Inspection and Replacement: Inspect the air filters for dirt and debris and replace them according to the manufacturer's recommendations.
- Control System Check: Verify that the control system is functioning correctly and that the setpoints are appropriate for the lab's requirements.
- Airflow Measurement: Measure the airflow through the ductwork to ensure that it is balanced and meets the design specifications.
- Temperature and Humidity Measurement: Measure the temperature and humidity at various points in the lab to ensure that they are within the desired range.
Routine inspections should be conducted on a regular basis, such as monthly or quarterly, depending on the specific requirements of the lab and the HVAC system.
2. Preventive Maintenance
Preventive maintenance involves performing regular tasks to keep the HVAC system operating efficiently and prevent major problems from occurring. These tasks may include:
- Cleaning and Lubrication: Clean and lubricate the HVAC equipment, including the AHU, chiller, boiler, and fans, according to the manufacturer's recommendations.
- Coil Cleaning: Clean the evaporator and condenser coils to remove dirt and debris that can reduce efficiency.
- Belt and Motor Inspection: Inspect the belts and motors for wear and tear and replace them as needed.
- Ductwork Inspection: Inspect the ductwork for leaks, damage, or insulation problems.
- Control System Calibration: Calibrate the control system to ensure that it is accurately measuring and regulating the environmental parameters.
Preventive maintenance should be conducted on a regular basis, such as annually or biannually, depending on the specific requirements of the lab and the HVAC system.
3. Corrective Maintenance
Corrective maintenance involves addressing any problems that are identified during routine inspections or preventive maintenance. This may involve repairing or replacing damaged components, adjusting the control system settings, or cleaning and lubricating the equipment. Corrective maintenance should be performed promptly to prevent minor problems from escalating into major issues.
HVAC System Optimization: Achieving Energy Efficiency
In today's environmentally conscious world, energy efficiency is a paramount concern. Optimizing the HVAC system in a laboratory can significantly reduce energy consumption and minimize the environmental impact of the facility. The following strategies can be employed to achieve energy efficiency in HVAC systems:
1. Building Envelope Optimization
The building envelope, which includes the walls, roof, windows, and doors, plays a significant role in energy efficiency. Optimizing the building envelope can reduce heat gain in the summer and heat loss in the winter, reducing the load on the HVAC system.
- Insulation: Adequate insulation in the walls, roof, and floors can significantly reduce heat transfer, reducing the need for heating and cooling.
- Window Glazing: High-performance windows with low-e coatings can reduce heat gain in the summer and heat loss in the winter.
- Air Sealing: Sealing air leaks in the building envelope can prevent conditioned air from escaping and unconditioned air from entering, reducing the load on the HVAC system.
2. HVAC System Upgrades
Upgrading the HVAC system can significantly improve energy efficiency. This may involve replacing outdated equipment with more energy-efficient models, installing variable-speed drives on fans and pumps, or implementing demand-controlled ventilation systems.
- High-Efficiency Equipment: Replacing outdated HVAC equipment with high-efficiency models can significantly reduce energy consumption.
- Variable-Speed Drives: Installing variable-speed drives on fans and pumps can adjust the speed of these components based on the load, reducing energy consumption.
- Demand-Controlled Ventilation: Demand-controlled ventilation systems adjust the ventilation rate based on occupancy and air quality, reducing energy consumption.
3. Building Automation and Control
Building automation and control systems can optimize the operation of the HVAC system, reducing energy consumption and improving comfort. These systems can monitor and adjust the HVAC system based on real-time conditions, such as occupancy, temperature, and humidity.
- Occupancy Sensors: Occupancy sensors can automatically adjust the HVAC system based on the presence or absence of people in a space, reducing energy consumption when the space is unoccupied.
- Temperature and Humidity Sensors: Temperature and humidity sensors can monitor the environmental conditions and adjust the HVAC system to maintain the desired comfort levels.
- Building Management Systems (BMS): BMS can integrate and control multiple HVAC components, optimizing the system's performance and reducing energy consumption.
4. Behavioral Changes
Behavioral changes can also play a role in reducing energy consumption. This may involve encouraging lab personnel to turn off lights and equipment when not in use, adjust the thermostat settings to appropriate levels, and use energy-efficient practices in the lab.
- Lighting: Using energy-efficient lighting fixtures and turning off lights when not in use can significantly reduce energy consumption.
- Equipment: Turning off equipment when not in use and using energy-efficient models can reduce energy consumption.
- Thermostat Settings: Adjusting the thermostat settings to appropriate levels can reduce energy consumption without compromising comfort.
Conclusion
The HVAC system is a critical component of any laboratory, ensuring optimal conditions for research, testing, and analysis. A well-designed and meticulously installed HVAC system is essential for maintaining the integrity of experiments, safeguarding sensitive equipment, and protecting the health and safety of personnel. This comprehensive guide has provided a roadmap for achieving optimal performance and compliance with industry standards, covering the installation process, commissioning protocols, maintenance procedures, and optimization strategies. By following these guidelines, laboratories can ensure that their HVAC systems are operating efficiently and effectively, contributing to the success of their scientific endeavors.
Ensuring Optimal Lab Function: A Recap
The successful installation and commissioning of HVAC systems in laboratories is paramount to achieving optimal lab function. This process involves a meticulous approach, encompassing careful planning, precise execution, and rigorous testing to guarantee the system's performance aligns with the specific requirements of the laboratory environment. This article has delved into the intricacies of this process, highlighting the critical steps involved in ensuring a seamless and efficient installation and commissioning process.
From the initial planning stages, where a thorough understanding of the laboratory's specific needs and environmental parameters is crucial, to the final commissioning phase, where the system's performance is rigorously tested and validated, each step plays a vital role in achieving a successful outcome. The article has emphasized the importance of meticulous documentation, clear communication, and a collaborative approach between all stakeholders involved, including lab technicians, project managers, procurement managers, and C-suite executives.
The article has also shed light on the critical role of proper ventilation and air filtration in maintaining a controlled and safe laboratory environment. It has highlighted the importance of selecting the appropriate HVAC system components, including air handling units, filters, and control systems, to meet the specific requirements of the laboratory. The article has also emphasized the importance of regular maintenance and calibration to ensure the system's continued performance and longevity.
By adhering to the outlined protocols and best practices, laboratories can ensure the successful installation and commissioning of their HVAC systems, thereby creating a controlled and safe environment conducive to scientific research and experimentation. This, in turn, contributes to the overall efficiency and productivity of the laboratory, fostering innovation and scientific breakthroughs.
Key Takeaways and Recommendations
The successful installation and commissioning of HVAC systems in laboratories is a complex process that requires careful planning, meticulous execution, and rigorous testing. By adhering to the following key takeaways and recommendations, laboratories can ensure the optimal performance of their HVAC systems, creating a controlled and safe environment for scientific research and experimentation.
1. Comprehensive Planning and Design
The foundation of a successful HVAC installation lies in comprehensive planning and design. This involves a thorough understanding of the laboratory's specific needs, including the type of research conducted, the required environmental parameters, and the potential hazards associated with the work. This information is crucial for selecting the appropriate HVAC system components, including air handling units, filters, and control systems, to meet the specific requirements of the laboratory.
Furthermore, the design phase should consider the layout of the laboratory, the location of equipment and personnel, and the potential for airflow disruptions. This ensures that the HVAC system is properly sized and configured to effectively control the laboratory environment, minimizing the risk of contamination and ensuring the safety of personnel.
2. Meticulous Installation and Commissioning
The installation and commissioning of the HVAC system should be carried out by qualified and experienced technicians who are familiar with the specific requirements of laboratory environments. This ensures that the system is installed correctly, with all components properly connected and functioning as intended. The commissioning phase involves rigorous testing and validation to ensure that the system meets the specified performance criteria, including temperature, humidity, and air quality parameters.
During the commissioning process, it is essential to document all test results and any adjustments made to the system. This documentation serves as a valuable reference for future maintenance and troubleshooting, ensuring that the system continues to operate optimally over its lifespan.
3. Regular Maintenance and Calibration
To ensure the continued performance and longevity of the HVAC system, regular maintenance and calibration are essential. This involves inspecting the system for any signs of wear or damage, cleaning filters and other components, and calibrating the control systems to ensure accurate temperature and humidity control. Regular maintenance helps to prevent system failures, reduce energy consumption, and extend the lifespan of the system.
It is also important to establish a comprehensive maintenance schedule that includes routine inspections, filter changes, and system calibration. This schedule should be tailored to the specific requirements of the laboratory and the operating conditions of the HVAC system.
4. Collaboration and Communication
The successful installation and commissioning of HVAC systems in laboratories require a collaborative approach between all stakeholders involved, including lab technicians, project managers, procurement managers, and C-suite executives. Clear communication is essential throughout the process, ensuring that everyone is aware of the project's goals, timelines, and potential challenges.
Regular meetings and communication channels should be established to facilitate information sharing and address any concerns or issues that may arise. This collaborative approach fosters a shared understanding of the project's objectives and ensures that the HVAC system meets the specific needs of the laboratory.
5. Continuous Improvement
The installation and commissioning of HVAC systems in laboratories is an ongoing process that requires continuous improvement. As technology advances and laboratory needs evolve, it is essential to review and update the HVAC system to ensure it remains effective and efficient. This may involve upgrading components, implementing new technologies, or adjusting the system's configuration to meet changing requirements.
By embracing a culture of continuous improvement, laboratories can ensure that their HVAC systems remain state-of-the-art, providing a controlled and safe environment for scientific research and experimentation.
Beyond the Basics: Optimizing Your Lab Environment
While the focus of this article has been on the installation and commissioning of HVAC systems, it's important to recognize that a comprehensive approach to laboratory environmental control extends beyond just the HVAC system. Factors such as lighting, noise levels, and even the layout of the laboratory can significantly impact the efficiency and productivity of research activities.
For instance, proper lighting can enhance visibility and reduce eye strain, while minimizing noise levels can create a more conducive environment for concentration and focus. A well-designed laboratory layout can optimize workflow, minimize bottlenecks, and ensure the safe and efficient handling of equipment and materials.
By considering these additional factors and implementing best practices for laboratory environmental control, laboratories can create a truly optimal environment for scientific research and experimentation, fostering innovation and scientific breakthroughs.
IT Tech: Your Partner in Laboratory Excellence
IT Tech understands the critical role that HVAC systems play in ensuring optimal lab function. We offer a comprehensive range of lab consumables and equipment, including high-quality HVAC components and systems designed specifically for laboratory environments. Our team of experts is dedicated to providing you with the best possible solutions to meet your specific needs, ensuring the successful installation and commissioning of your HVAC system.
We also offer a range of services to support your laboratory operations, including installation, commissioning, maintenance, and calibration of HVAC systems. Our commitment to quality and customer satisfaction ensures that you receive the best possible service and support, enabling you to focus on your research and achieve your scientific goals.
To learn more about our products and services, or to discuss your specific laboratory needs, please contact us today. We are dedicated to helping you create a controlled and safe environment for your research, fostering innovation and scientific breakthroughs.
Welcome to IT Tech's personalized approach to finding the ideal HVAC system for your laboratory. Our tailored services and comprehensive product offerings ensure that you receive the best solution to maximize efficiency, safety, and productivity in your lab environment.
Discover the perfect HVAC system for your lab by exploring IT Tech's bouquet of services and products. Our team is dedicated to understanding your specific requirements and providing customized solutions that meet your unique needs.
To begin your journey towards a controlled and safe laboratory environment, submit an inquiry to IT Tech today. Our experts are ready to assist you in selecting and implementing the perfect HVAC system for your lab, fostering innovation and scientific breakthroughs every step of the way.
Partner with IT Tech for a well-designed and properly installed HVAC system that is an essential investment in the success of your laboratory. Together, let's create an environment conducive to research excellence and advancement.
Submit your inquiry now and take the first step towards optimizing your laboratory environment with IT Tech.
Products You may Like
Check out other IT- Tech product that suit your taste
Subscribe to our newsletter
Stay updated with IT-Tech Insights
Related posts
Check out other IT- Tech Scientific Resources
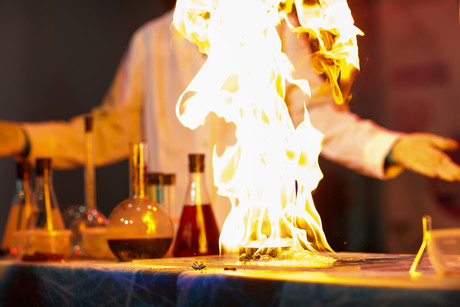
Lab fire hazards and applicable codes
Laboratories are inherently prone to fire hazards due to the presence of flammable chemicals, electrical equipment, and potential ignition sources. This article provides an overview of these hazards and the applicable codes that govern fire safety in laboratory settings. It highlights the importance of implementing comprehensive fire safety protocols, including the use of fire extinguishers, sprinkler systems, and other fire fighting systems. By understanding the risks and adhering to relevant codes, laboratories can significantly reduce the likelihood of fire incidents and ensure the safety of personnel and equipment.
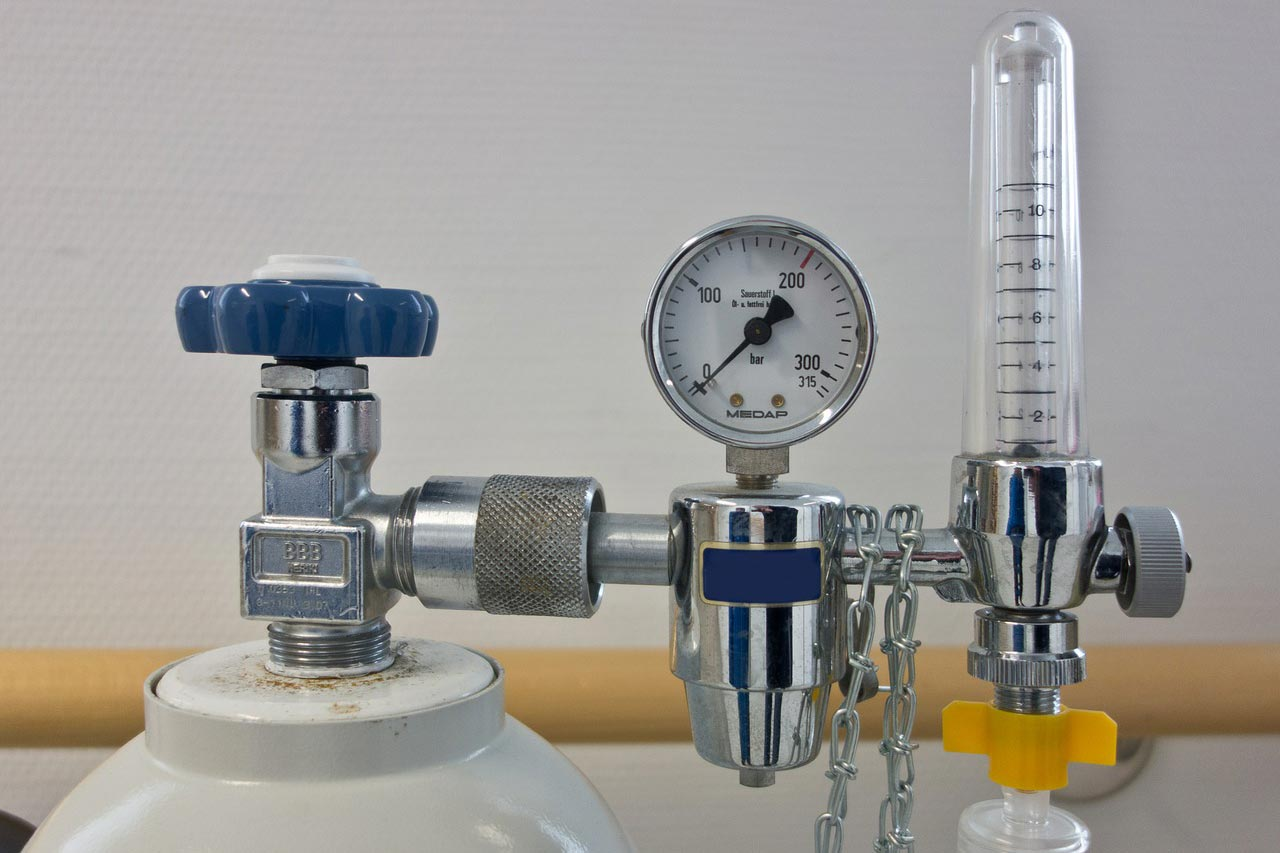
Types of lab gases and their applications
Laboratory gases play a vital role in a wide range of scientific research and development activities. From analytical chemistry to material science, these gases are essential for conducting experiments, calibrating instruments, and synthesizing new materials. This article explores the different types of lab gases, including nitrogen, oxygen, helium, argon, and hydrogen, highlighting their unique properties and applications. We also discuss the importance of reliable gas piping and distribution systems for safe and efficient delivery of these gases to laboratory equipment. Understanding the characteristics and applications of lab gases is crucial for researchers and lab technicians to ensure accurate and reliable experimental results.
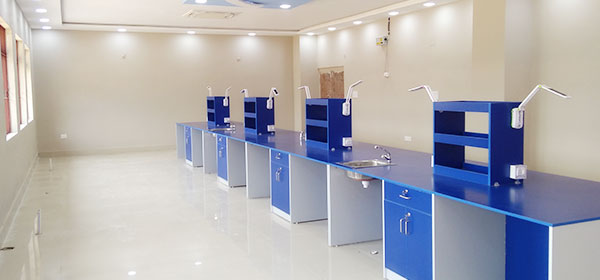
Comparing lab benchtop and flooring materials
Selecting the appropriate lab benchtop and flooring materials is essential for creating a safe, durable, and functional research space. This article explores the characteristics of common materials used in laboratories, including their resistance to chemicals, heat, and abrasion. We delve into the pros and cons of each material, considering factors like cost, maintenance, and suitability for specific applications. By understanding the differences between various options, you can make informed decisions to optimize your laboratory's performance and longevity.