Implementing lab engineering change control
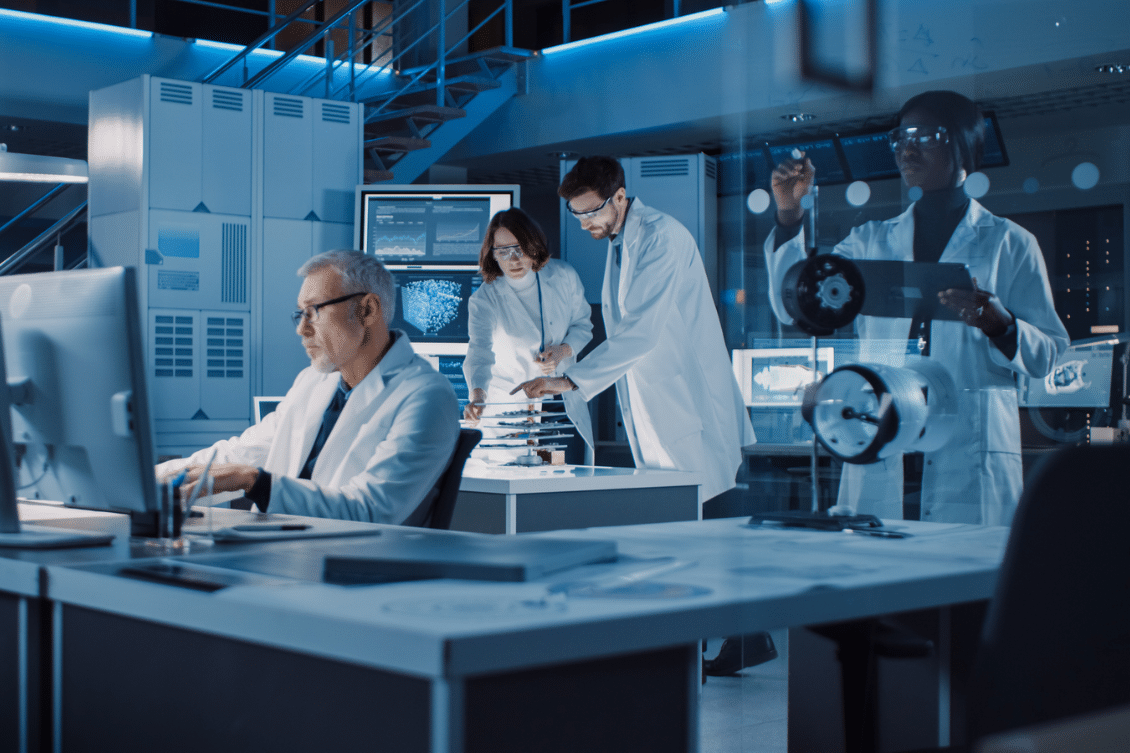
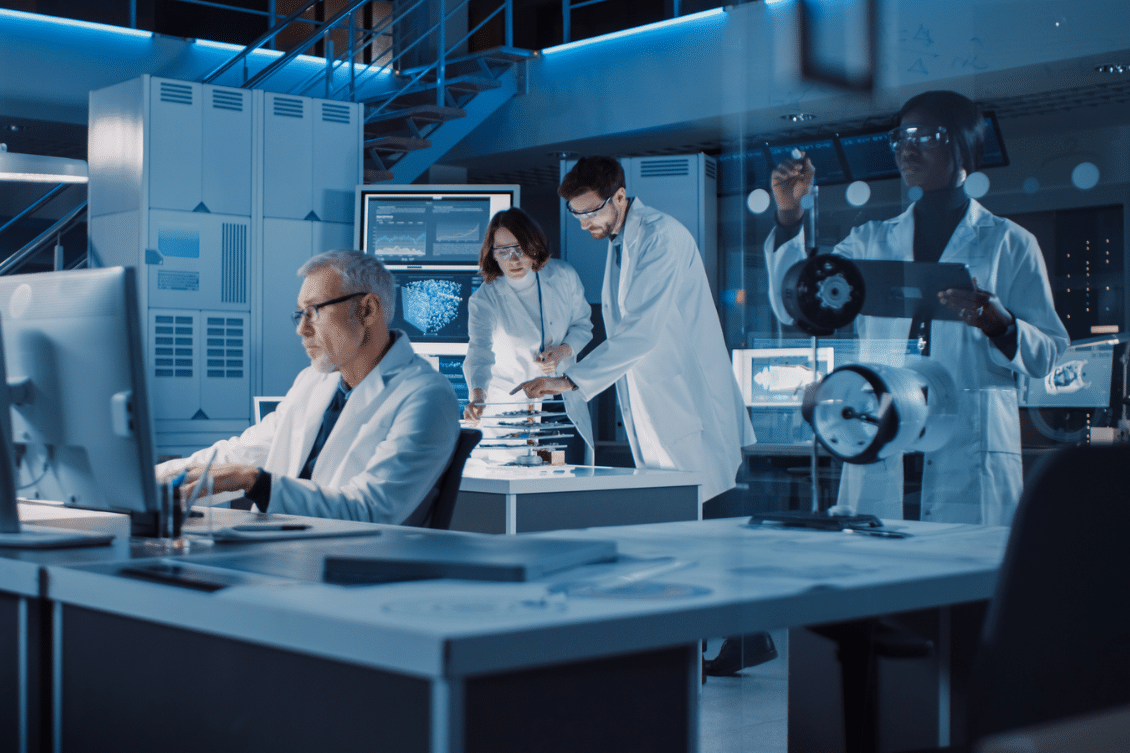
Implementing Lab Engineering Change Control
In the dynamic realm of scientific research and development, laboratories are the epicenters of innovation, where groundbreaking discoveries are made and cutting-edge technologies are refined. The intricate interplay of sophisticated equipment, specialized consumables, and highly skilled personnel necessitates a robust framework for managing change, ensuring the integrity and efficiency of laboratory operations. This framework is known as **Lab Engineering Change Control**, a critical process that governs the implementation of modifications to laboratory infrastructure, equipment, procedures, and consumables.
The need for change control in laboratories arises from the inherent nature of scientific exploration. As research progresses, new discoveries, evolving technologies, and changing regulatory landscapes necessitate adjustments to existing practices and infrastructure. These changes, if not carefully managed, can introduce unintended consequences, jeopardizing the accuracy, reliability, and safety of laboratory operations. Implementing a comprehensive change control system is paramount to mitigating these risks and ensuring the seamless integration of modifications while maintaining the integrity of research outcomes.
The Importance of Lab Engineering Change Control
The significance of Lab Engineering Change Control extends beyond mere compliance with regulatory requirements. It serves as a cornerstone for maintaining the integrity of scientific research, ensuring the accuracy and reliability of experimental results, and safeguarding the safety of laboratory personnel. A well-defined change control process fosters a culture of accountability, transparency, and continuous improvement within the laboratory environment.
Ensuring Data Integrity and Reproducibility
Scientific research relies heavily on the reproducibility of experimental results. Any changes to laboratory equipment, procedures, or consumables can potentially impact the accuracy and reliability of data. Lab Engineering Change Control provides a structured framework for documenting and validating these changes, ensuring that any modifications are properly assessed and their potential impact on data integrity is understood. This meticulous approach safeguards the validity of research findings and enhances the credibility of scientific publications.
Maintaining Equipment Performance and Safety
Laboratory equipment is often highly specialized and critical to the success of research projects. Changes to equipment, such as upgrades, repairs, or replacements, can affect its performance and safety. Lab Engineering Change Control ensures that all equipment modifications are properly documented, tested, and validated, minimizing the risk of equipment malfunction or safety hazards. This proactive approach helps maintain the optimal performance of laboratory equipment and safeguards the well-being of laboratory personnel.
Streamlining Laboratory Operations
Change control processes can streamline laboratory operations by providing a structured framework for managing modifications. By clearly defining the steps involved in implementing changes, from initiation to approval and implementation, the process ensures that all stakeholders are informed and involved. This collaborative approach minimizes delays, reduces errors, and promotes efficient workflow within the laboratory environment.
Compliance with Regulatory Requirements
Many regulatory bodies, such as the Food and Drug Administration (FDA) and the European Medicines Agency (EMA), require laboratories to implement robust change control systems. These regulations are designed to ensure the quality, safety, and efficacy of products and processes. Lab Engineering Change Control helps laboratories comply with these regulations by providing a documented system for managing changes and demonstrating adherence to regulatory standards.
Key Components of Lab Engineering Change Control
A comprehensive Lab Engineering Change Control system encompasses several key components, each playing a crucial role in ensuring the smooth and effective implementation of changes within the laboratory environment.
1. Change Request and Evaluation
The process begins with a formal change request, which outlines the proposed modification and its rationale. This request should be submitted by a designated individual, typically a laboratory technician, project manager, or procurement manager, who has identified the need for change. The change request should include detailed information about the proposed modification, its potential impact on laboratory operations, and the justification for its implementation.
Once submitted, the change request is reviewed and evaluated by a designated change control team. This team typically comprises individuals with expertise in laboratory operations, equipment maintenance, safety, and regulatory compliance. The team assesses the proposed change, considering its potential impact on data integrity, equipment performance, safety, and compliance with regulatory requirements. The team may also consult with other stakeholders, such as laboratory personnel, project managers, and procurement managers, to gather input and ensure a comprehensive evaluation.
2. Risk Assessment and Mitigation
A crucial step in the change control process is the assessment of potential risks associated with the proposed modification. This risk assessment should identify potential hazards, evaluate their likelihood and severity, and develop mitigation strategies to minimize the risks. The risk assessment should consider factors such as the impact on data integrity, equipment performance, safety, and compliance with regulatory requirements.
The risk assessment process may involve the use of formal risk assessment tools and methodologies, such as Failure Mode and Effects Analysis (FMEA) or Hazard Analysis and Critical Control Points (HACCP). These tools provide a structured framework for identifying potential risks, evaluating their likelihood and severity, and developing mitigation strategies. The risk assessment should be documented and reviewed by the change control team to ensure that all potential risks have been identified and addressed.
4. Implementation and Verification
Once the change has been approved, it is implemented according to a pre-defined plan. This plan should outline the steps involved in implementing the change, the resources required, and the timeline for completion. The implementation process should be carefully monitored to ensure that it is carried out according to the plan and that any potential risks are mitigated.
After the change has been implemented, it is verified to ensure that it meets the intended objectives and that it does not introduce any unintended consequences. This verification process may involve testing, validation, and documentation. The verification results should be documented and reviewed by the change control team to ensure that the change has been successfully implemented and that it meets all requirements.
5. Documentation and Record Keeping
Comprehensive documentation is essential for effective Lab Engineering Change Control. All aspects of the change control process, from the initial change request to the final verification, should be meticulously documented. This documentation should include the following information:
- Change request details
- Risk assessment results
- Approval records
- Implementation plan
- Verification results
- Any deviations from the plan
- Corrective actions taken
This documentation provides a clear audit trail of the change control process, allowing for easy tracking of changes, identification of potential issues, and demonstration of compliance with regulatory requirements. The documentation should be stored in a secure and accessible location, ensuring that it is readily available for review and audit purposes.
Benefits of Implementing Lab Engineering Change Control
Implementing a robust Lab Engineering Change Control system offers numerous benefits for laboratories, enhancing the efficiency, safety, and integrity of research operations.
Improved Data Integrity and Reproducibility
By meticulously documenting and validating all changes, Lab Engineering Change Control ensures that any modifications to laboratory procedures, equipment, or consumables are properly assessed and their potential impact on data integrity is understood. This rigorous approach safeguards the validity of research findings and enhances the credibility of scientific publications, fostering trust in the scientific community.
Enhanced Equipment Performance and Safety
Lab Engineering Change Control helps maintain the optimal performance of laboratory equipment by ensuring that all modifications are properly documented, tested, and validated. This proactive approach minimizes the risk of equipment malfunction or safety hazards, safeguarding the well-being of laboratory personnel and ensuring the smooth operation of research projects.
Streamlined Laboratory Operations
By providing a structured framework for managing changes, Lab Engineering Change Control streamlines laboratory operations, minimizing delays, reducing errors, and promoting efficient workflow. This collaborative approach ensures that all stakeholders are informed and involved in the change process, fostering a culture of transparency and accountability.
Compliance with Regulatory Requirements
Lab Engineering Change Control helps laboratories comply with regulatory requirements by providing a documented system for managing changes and demonstrating adherence to regulatory standards. This compliance ensures that laboratories operate within the legal framework, minimizing the risk of penalties or sanctions.
Continuous Improvement
Lab Engineering Change Control fosters a culture of continuous improvement by providing a mechanism for identifying areas for enhancement and implementing changes to improve laboratory operations. By regularly reviewing the change control process and seeking feedback from stakeholders, laboratories can identify opportunities for optimization and enhance the overall efficiency and effectiveness of their operations.
Challenges in Implementing Lab Engineering Change Control
While the benefits of Lab Engineering Change Control are undeniable, implementing a robust system can present certain challenges, requiring careful planning, communication, and commitment from all stakeholders.
Resistance to Change
One of the most common challenges in implementing change control is resistance from laboratory personnel. Individuals may be reluctant to embrace new procedures or technologies, fearing disruption to their established routines or a perceived loss of control. Overcoming this resistance requires effective communication, education, and training, emphasizing the benefits of change control and addressing concerns in a timely and respectful manner.
Lack of Resources
Implementing a comprehensive change control system requires resources, including time, personnel, and funding. Laboratories may face challenges in allocating sufficient resources to the change control process, particularly in resource-constrained environments. Addressing this challenge requires prioritizing change control activities, allocating resources strategically, and seeking support from senior management.
Complexity of the Process
The change control process can be complex, involving multiple steps, stakeholders, and documentation requirements. This complexity can lead to confusion, delays, and errors if not properly managed. Overcoming this challenge requires clear communication, standardized procedures, and effective training for all stakeholders involved in the change control process.
Lack of Standardization
In some laboratories, change control processes may not be standardized, leading to inconsistencies and inefficiencies. This lack of standardization can make it difficult to track changes, assess risks, and ensure compliance with regulatory requirements. Addressing this challenge requires developing and implementing standardized procedures for change control, ensuring consistency across all laboratory operations.
Best Practices for Implementing Lab Engineering Change Control
To overcome these challenges and successfully implement Lab Engineering Change Control, laboratories should adopt best practices that ensure the effectiveness and efficiency of the process.
1. Define Clear Roles and Responsibilities
Clearly define the roles and responsibilities of individuals involved in the change control process. This includes identifying the individuals responsible for initiating change requests, evaluating changes, approving changes, implementing changes, and verifying changes. This clarity ensures accountability and facilitates efficient workflow.
2. Establish a Standardized Change Control Process
Develop and implement a standardized change control process that outlines the steps involved in initiating, evaluating, approving, implementing, and verifying changes. This standardization ensures consistency, reduces errors, and facilitates compliance with regulatory requirements.
3. Use a Change Control System
Utilize a dedicated change control system, either software-based or paper-based, to manage change requests, track approvals, document implementation details, and record verification results. This system provides a centralized repository for all change control information, facilitating easy access, tracking, and auditing.
4. Conduct Regular Reviews and Audits
Regularly review and audit the change control process to identify areas for improvement and ensure its effectiveness. This review should involve assessing the process's efficiency, identifying any bottlenecks or inconsistencies, and evaluating the effectiveness of risk mitigation strategies. The audit results should be documented and used to refine the change control process.
5. Provide Training and Education
Provide comprehensive training and education to all laboratory personnel involved in the change control process. This training should cover the purpose of change control, the steps involved in the process, the documentation requirements, and the importance of compliance with regulatory requirements. This education ensures that all stakeholders understand their roles and responsibilities and can effectively participate in the change control process.
6. Foster a Culture of Continuous Improvement
Encourage a culture of continuous improvement by actively seeking feedback from laboratory personnel on the change control process. This feedback can be gathered through surveys, meetings, or informal discussions. The feedback should be used to identify areas for improvement and refine the change control process to ensure its effectiveness and efficiency.
Conclusion
Lab Engineering Change Control is an essential process for maintaining the integrity, efficiency, and safety of laboratory operations. By implementing a robust change control system, laboratories can ensure that all modifications are properly assessed, documented, and validated, safeguarding the accuracy and reliability of research findings, enhancing equipment performance, and complying with regulatory requirements. By adopting best practices, laboratories can overcome the challenges associated with implementing change control and reap the numerous benefits it offers, fostering a culture of continuous improvement and ensuring the success of their research endeavors.
Streamlining Lab Operations: A Recap
In the dynamic world of scientific research and development, maintaining operational efficiency is paramount. This is where the concept of "Lab Engineering Services" comes into play, offering a comprehensive approach to optimizing lab workflows, ensuring accuracy, and maximizing productivity. This article has delved into the critical aspect of implementing lab engineering change control, a cornerstone of effective lab management. We've explored the rationale behind this practice, the key steps involved, and the potential pitfalls to avoid.
By embracing a structured change control process, laboratories can mitigate risks associated with modifications, ensuring that any alterations to equipment, procedures, or materials are thoroughly evaluated, documented, and implemented in a controlled manner. This approach fosters a culture of accountability, transparency, and continuous improvement, ultimately contributing to the reliability and validity of research outcomes.
The journey towards streamlined lab operations is not without its challenges. Implementing change control effectively requires a collaborative effort from all stakeholders, including lab technicians, project managers, procurement managers, and even C-suite executives. It necessitates a commitment to clear communication, meticulous documentation, and a willingness to adapt to evolving needs. However, the rewards are substantial, ranging from enhanced data integrity and reduced errors to improved compliance with regulatory standards and increased overall efficiency.
As we conclude this exploration of lab engineering change control, it's crucial to remember that this is not a one-time endeavor. It's an ongoing process that requires continuous evaluation, refinement, and adaptation. By regularly reviewing and updating change control procedures, laboratories can ensure they remain aligned with evolving scientific practices, technological advancements, and regulatory requirements.
To further enhance your understanding of lab engineering services and their impact on your specific laboratory environment, explore IT Tech's bouquet of services and products. Our tailored solutions can address your unique needs and challenges, helping you optimize your lab operations for maximum efficiency and success.
Ready to take your lab operations to the next level? Submit an enquiry to IT Tech today and discover personalized recommendations for optimizing your workflow and maximizing efficiency. Unlock the full potential of your laboratory and contribute to groundbreaking scientific discoveries with IT Tech by your side.
Products You may Like
Check out other IT- Tech product that suit your taste
Subscribe to our newsletter
Stay updated with IT-Tech Insights
Related posts
Check out other IT- Tech Scientific Resources
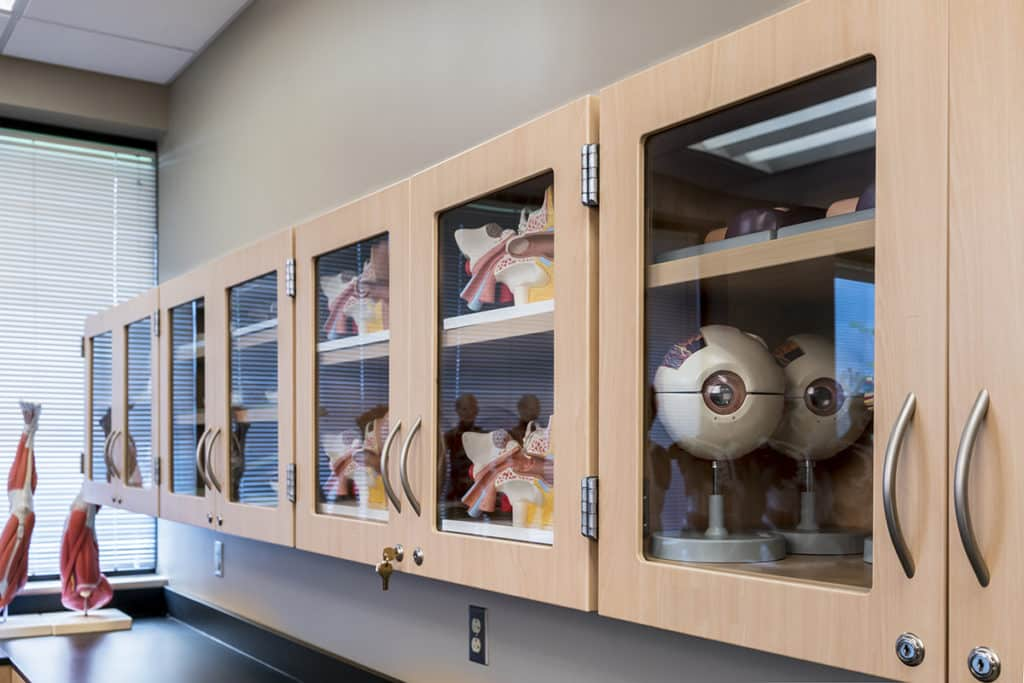
Modular vs custom built-in lab casework
Choosing the right lab casework is crucial for any research facility. Modular casework offers flexibility and cost-effectiveness, while custom built-in solutions provide tailored design and functionality. This article examines the key considerations for each option, including space utilization, budget, and long-term adaptability. We delve into the benefits and drawbacks of both approaches, empowering you to make an informed decision that aligns with your research needs and budget.
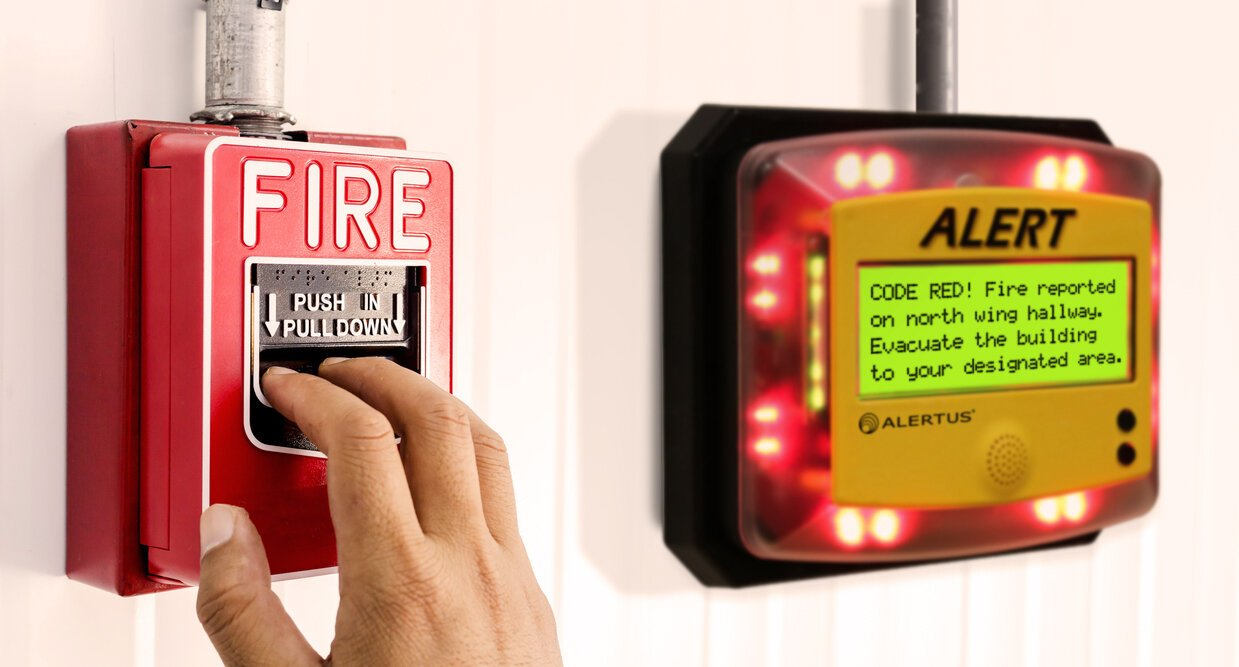
Selecting fire alarm and emergency notification
Properly sizing fire sprinkler and standpipe systems is crucial for effective fire suppression. This article delves into the factors influencing system design, including building occupancy, water supply, and fire hazard classification. It emphasizes the importance of professional expertise in conducting hydraulic calculations, selecting appropriate components, and ensuring compliance with relevant building codes. By understanding the intricacies of system sizing, you can make informed decisions to safeguard your property and occupants from fire hazards.
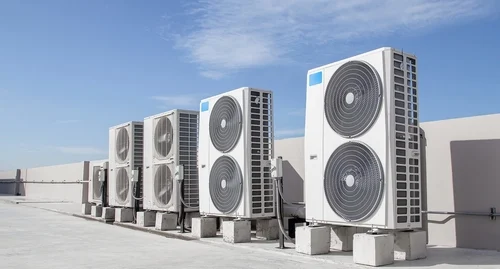
Comparing HVAC system architectures
This article provides a comprehensive comparison of various HVAC system architectures commonly used in research laboratories. It delves into the strengths and weaknesses of each system, including central air conditioning, split systems, and variable refrigerant flow (VRF) systems. The article also discusses factors to consider when selecting an HVAC system, such as energy efficiency, temperature control precision, and cost. By understanding the different architectures and their characteristics, researchers can make informed decisions to optimize their lab's environment and enhance research productivity.