Maintenance best practices for lab gas supply
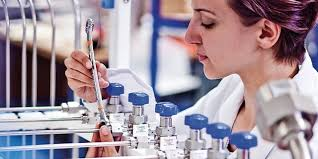
The Vital Role of Gas Piping & Distribution Systems in Laboratory Safety
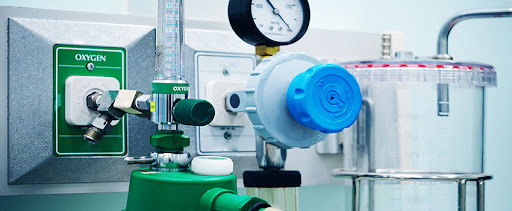
In the realm of scientific research and development, laboratories serve as the bedrock of innovation, where groundbreaking discoveries and technological advancements are made. These specialized environments rely heavily on a complex network of infrastructure, including sophisticated equipment, advanced instrumentation, and a critical component often overlooked: gas piping & distribution systems. These systems play a pivotal role in delivering essential gases, such as nitrogen, oxygen, hydrogen, helium, and argon, to various laboratory applications, enabling a wide range of experiments and procedures.
The safe and reliable delivery of these gases is paramount to the integrity of research, the well-being of laboratory personnel, and the overall operational efficiency of the facility. Gas piping & distribution systems are not merely conduits for gas flow; they are intricate networks that require meticulous design, installation, maintenance, and ongoing monitoring to ensure optimal performance and minimize the risk of accidents or malfunctions.
The consequences of neglecting proper maintenance and safety protocols within these systems can be severe, ranging from minor disruptions in research to catastrophic events with potentially life-threatening outcomes. The potential hazards associated with gas leaks, explosions, or fires underscore the critical need for a comprehensive understanding of gas piping & distribution systems and the implementation of robust maintenance best practices.
This article delves into the intricacies of gas piping & distribution systems, highlighting the importance of preventive maintenance, regular inspections, and adherence to industry standards. It aims to provide laboratory technicians, project managers, procurement managers, and C-suite executives in the scientific industry with the knowledge and tools necessary to ensure the safe and reliable operation of these vital systems, safeguarding both personnel and research endeavors.
The article will explore the following key aspects:
- Understanding the fundamentals of gas piping & distribution systems, including their components, design considerations, and operational principles.
- Identifying potential hazards and risks associated with gas leaks, explosions, and fires, emphasizing the importance of proactive measures to mitigate these threats.
- Establishing a comprehensive maintenance program that encompasses regular inspections, leak testing, pressure checks, and component replacement, ensuring the longevity and reliability of the system.
- Implementing best practices for gas handling and usage, including proper cylinder storage, valve operation, and emergency procedures.
- Promoting a culture of safety awareness among laboratory personnel, fostering a collaborative approach to risk management and incident reporting.
By addressing these critical aspects, this article seeks to empower laboratory professionals with the knowledge and tools necessary to ensure the safe and efficient operation of gas piping & distribution systems, contributing to a secure and productive research environment.
The Vital Role of Gas Piping & Distribution Systems in Laboratory Operations
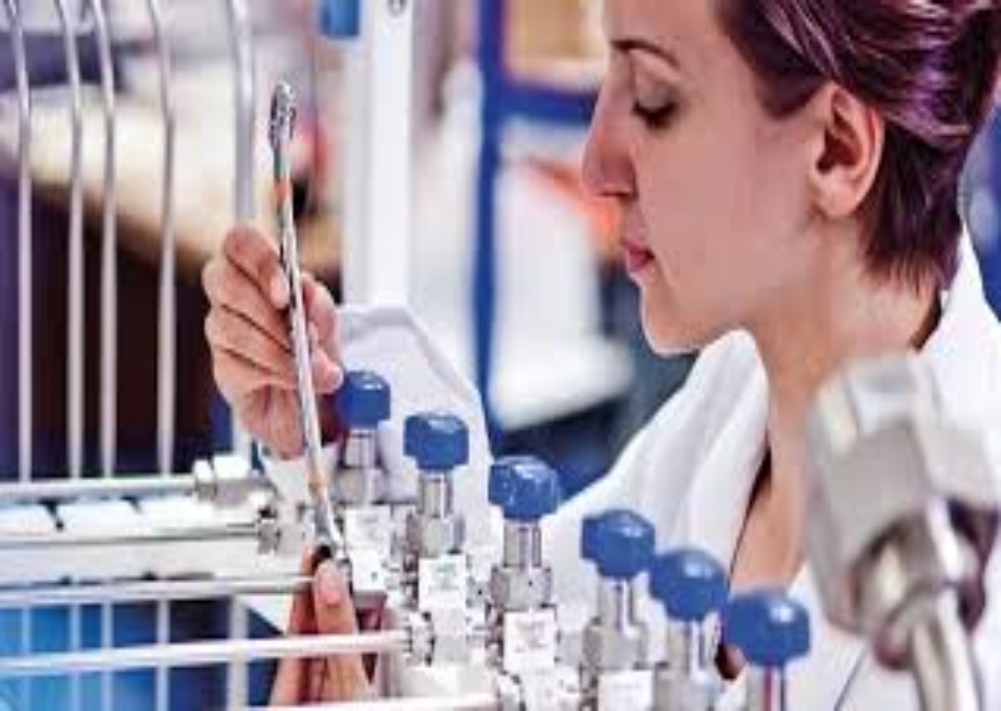
In the realm of scientific research and development, laboratories serve as the bedrock of innovation, where groundbreaking discoveries and technological advancements are meticulously crafted. At the heart of these laboratories lies a critical infrastructure that often goes unnoticed yet plays an indispensable role in ensuring the smooth and reliable operation of experiments and analyses: the gas piping & distribution systems. These systems are the lifeblood of many laboratory processes, providing a constant and controlled supply of essential gases that are vital for a wide range of applications.
From the precise delivery of oxygen for cell culture and the controlled flow of nitrogen for inert atmospheres to the precise delivery of flammable gases like acetylene for welding and cutting, gas piping & distribution systems are the unsung heroes of laboratory operations. Their reliability and integrity are paramount, as any disruption or malfunction can have significant consequences, ranging from compromised experimental results to safety hazards.
The importance of gas piping & distribution systems extends beyond the immediate needs of individual experiments. These systems are often integrated into complex laboratory workflows, supporting multiple research projects and analytical techniques simultaneously. Their efficient operation is crucial for maintaining the overall productivity and efficiency of the laboratory, ensuring that researchers can focus on their core scientific endeavors without being hindered by technical issues.
However, the complexity of these systems and the critical nature of their function necessitate a comprehensive approach to maintenance and management. Neglecting routine maintenance can lead to a cascade of problems, including leaks, pressure fluctuations, and contamination, all of which can compromise the integrity of experiments and potentially endanger personnel. This is where a proactive and well-defined maintenance strategy becomes essential, ensuring that gas piping & distribution systems operate reliably and safely over their lifespan.
Understanding the Components of Gas Piping & Distribution Systems
Before delving into the intricacies of maintenance best practices, it is crucial to have a fundamental understanding of the components that make up a typical gas piping & distribution system. These systems are typically comprised of several key elements, each playing a distinct role in the safe and efficient delivery of gases to laboratory equipment.
1. Gas Cylinders: The Source of Supply
The journey of a gas supply begins with the gas cylinders themselves, which serve as the primary source of the gases used in the laboratory. These cylinders are typically made of high-pressure steel and contain the compressed gas under high pressure. The type of gas cylinder used will depend on the specific gas required for the application, with different gases requiring different cylinder sizes, pressures, and safety features.
Gas cylinders are typically equipped with a variety of safety features, including pressure relief valves, safety caps, and cylinder valves. These features are designed to prevent over-pressurization, accidental release of gas, and other potential hazards. It is essential to ensure that all safety features are in good working order and that the cylinders are properly labeled and stored in accordance with safety regulations.
2. Gas Regulators: Controlling the Flow
Once the gas cylinder is in place, the next step is to control the flow of gas to the laboratory equipment. This is where gas regulators come into play. Gas regulators are devices that reduce the high pressure of the gas in the cylinder to a lower, more manageable pressure suitable for laboratory applications.
Gas regulators typically consist of a pressure gauge, a control knob, and a diaphragm or piston that regulates the flow of gas. The pressure gauge indicates the pressure of the gas in the cylinder, while the control knob allows the user to adjust the output pressure. The diaphragm or piston acts as a valve, opening and closing to control the flow of gas based on the desired output pressure.
Gas regulators are essential for ensuring that the gas is delivered at the correct pressure and flow rate for the specific application. They also play a crucial role in preventing over-pressurization and ensuring the safe operation of the gas piping & distribution system.
3. Gas Piping: The Pathway to Delivery
The gas piping system is the backbone of the gas distribution network, providing the pathway for the gas to travel from the gas cylinders to the laboratory equipment. Gas piping is typically made of copper, stainless steel, or other materials that are compatible with the specific gas being delivered.
The design and layout of the gas piping system are critical for ensuring the safe and efficient delivery of gas. The piping should be properly sized to accommodate the flow rate of the gas, and it should be installed in a way that minimizes the risk of leaks and other hazards. The piping should also be properly supported and secured to prevent damage or movement.
Gas piping systems are often equipped with a variety of fittings and valves, which allow for the control and distribution of gas to different parts of the laboratory. These fittings and valves should be regularly inspected and maintained to ensure that they are in good working order and that they are not leaking.
4. Gas Manifolds: Centralized Control
Gas manifolds are central hubs in the gas piping & distribution system, providing a point of connection for multiple gas cylinders and allowing for the distribution of gas to different parts of the laboratory. Gas manifolds typically consist of a series of valves and fittings that allow for the selection and control of the gas supply to different outlets.
Gas manifolds are essential for managing the flow of gas from multiple cylinders and for ensuring that the correct gas is delivered to the appropriate equipment. They also provide a convenient point for monitoring the pressure and flow rate of the gas supply.
5. Gas Outlets: The Final Destination
Gas outlets are the final points of connection in the gas piping & distribution system, providing the interface between the gas piping and the laboratory equipment. Gas outlets are typically equipped with a valve that allows for the control of the flow of gas to the equipment.
Gas outlets should be designed and installed in a way that minimizes the risk of leaks and other hazards. They should also be easily accessible for maintenance and inspection. The type of gas outlet used will depend on the specific equipment being connected, with different equipment requiring different types of connections and fittings.
The Importance of Regular Maintenance for Gas Piping & Distribution Systems
The reliability and safety of gas piping & distribution systems are paramount for the smooth operation of the laboratory. Regular maintenance is essential for ensuring that these systems operate safely and efficiently over their lifespan. Neglecting routine maintenance can lead to a cascade of problems, including leaks, pressure fluctuations, and contamination, all of which can compromise the integrity of experiments and potentially endanger personnel.
A comprehensive maintenance program should include a combination of preventative maintenance, corrective maintenance, and ongoing monitoring. Preventative maintenance involves regularly inspecting and servicing the system to identify and address potential problems before they become major issues. Corrective maintenance involves addressing problems that have already occurred, such as leaks or malfunctions. Ongoing monitoring involves regularly checking the system for signs of wear and tear, leaks, and other potential problems.
Preventative Maintenance: Proactive Measures for Long-Term Reliability
Preventative maintenance is the cornerstone of a robust maintenance program for gas piping & distribution systems. By proactively identifying and addressing potential problems before they become major issues, preventative maintenance helps to ensure the long-term reliability and safety of the system.
1. Regular Inspections: Catching Problems Early
Regular inspections are the foundation of preventative maintenance. These inspections should be conducted on a regular schedule, with the frequency depending on the specific system and the level of risk associated with its operation. Inspections should cover all components of the system, including gas cylinders, regulators, piping, manifolds, and outlets.
During inspections, technicians should look for signs of wear and tear, leaks, corrosion, damage, and other potential problems. They should also check the pressure gauges, valves, and other components to ensure that they are functioning properly. Any problems identified during inspections should be addressed promptly to prevent them from escalating into more serious issues.
2. Pressure Testing: Ensuring System Integrity
Pressure testing is a critical component of preventative maintenance for gas piping & distribution systems. This involves pressurizing the system to a specified pressure and then monitoring for leaks or other problems. Pressure testing helps to ensure that the system is capable of handling the pressure of the gas being delivered and that it is not leaking.
The frequency of pressure testing will depend on the specific system and the level of risk associated with its operation. However, it is generally recommended that pressure testing be conducted at least annually, or more frequently if the system is used heavily or if there is a high risk of leaks.
4. Valve Maintenance: Ensuring Proper Operation
Valves are essential components of gas piping & distribution systems, and they require regular maintenance to ensure that they are functioning properly. Valve maintenance should include inspecting the valves for signs of wear and tear, leaks, corrosion, and damage. It should also include lubricating the valves to ensure that they operate smoothly.
The frequency of valve maintenance will depend on the specific valves and the level of use. However, it is generally recommended that valves be inspected and lubricated at least annually, or more frequently if they are used heavily.
5. Gas Cylinder Inspection: Maintaining Safety
Gas cylinders are the primary source of gas for the laboratory, and they require regular inspection to ensure that they are safe and in good working order. Gas cylinder inspections should include checking the cylinder for signs of damage, corrosion, or leaks. They should also include checking the pressure relief valve, safety cap, and cylinder valve to ensure that they are functioning properly.
The frequency of gas cylinder inspections will depend on the specific cylinder and the level of use. However, it is generally recommended that cylinders be inspected at least annually, or more frequently if they are used heavily.
Corrective Maintenance: Addressing Problems as They Arise
Corrective maintenance involves addressing problems that have already occurred in the gas piping & distribution system. This can include repairing leaks, replacing damaged components, or addressing other malfunctions. Corrective maintenance is essential for ensuring the safety and reliability of the system, and it should be conducted promptly to prevent problems from escalating.
1. Leak Repair: Stopping the Flow
Leaks are a common problem in gas piping & distribution systems, and they can pose a significant safety hazard. Leaks can occur in any part of the system, and they can be caused by a variety of factors, including corrosion, damage, or improper installation.
Leak repair should be conducted by qualified technicians who are familiar with the specific system and the safety procedures involved. The repair process will vary depending on the location and cause of the leak, but it may involve replacing damaged piping, tightening fittings, or applying sealant.
2. Component Replacement: Restoring Functionality
Components of the gas piping & distribution system can fail over time, and they may need to be replaced. This can include replacing damaged piping, regulators, valves, manifolds, or outlets. Component replacement should be conducted by qualified technicians who are familiar with the specific system and the safety procedures involved.
When replacing components, it is important to use parts that are compatible with the system and that meet the appropriate safety standards. It is also important to ensure that the new components are properly installed to prevent leaks or other problems.
3. System Troubleshooting: Identifying and Resolving Malfunctions
Malfunctions can occur in any part of the gas piping & distribution system, and they can be caused by a variety of factors. System troubleshooting involves identifying the cause of the malfunction and then taking steps to resolve it. This may involve inspecting the system for signs of damage, checking the pressure gauges and valves, or testing the components.
System troubleshooting should be conducted by qualified technicians who are familiar with the specific system and the safety procedures involved. It is important to isolate the problem area and to take steps to prevent further damage or injury during the troubleshooting process.
Ongoing Monitoring: Keeping a Watchful Eye
Ongoing monitoring is an essential part of a comprehensive maintenance program for gas piping & distribution systems. This involves regularly checking the system for signs of wear and tear, leaks, and other potential problems. Ongoing monitoring helps to identify problems early, before they become major issues, and it can help to prevent accidents and ensure the safety of personnel.
1. Pressure Monitoring: Tracking System Performance
Pressure monitoring is an important aspect of ongoing monitoring. This involves regularly checking the pressure gauges on the gas cylinders, regulators, and manifolds to ensure that the pressure is within the acceptable range. Pressure monitoring helps to identify problems such as leaks, blockages, or malfunctions in the system.
The frequency of pressure monitoring will depend on the specific system and the level of risk associated with its operation. However, it is generally recommended that pressure monitoring be conducted at least daily, or more frequently if the system is used heavily or if there is a high risk of leaks.
2. Flow Rate Monitoring: Ensuring Adequate Supply
Flow rate monitoring is another important aspect of ongoing monitoring. This involves checking the flow rate of gas to the laboratory equipment to ensure that it is sufficient for the application. Flow rate monitoring helps to identify problems such as leaks, blockages, or malfunctions in the system that may be restricting the flow of gas.
The frequency of flow rate monitoring will depend on the specific system and the level of risk associated with its operation. However, it is generally recommended that flow rate monitoring be conducted at least daily, or more frequently if the system is used heavily or if there is a high risk of leaks.
3. Visual Inspections: Identifying Potential Problems
Visual inspections are a simple but effective way to monitor the gas piping & distribution system. This involves regularly inspecting the system for signs of wear and tear, leaks, corrosion, damage, and other potential problems. Visual inspections should be conducted on a regular schedule, with the frequency depending on the specific system and the level of risk associated with its operation.
During visual inspections, technicians should look for signs of leaks, such as bubbles in soap solution, hissing sounds, or the smell of gas. They should also look for signs of corrosion, damage, or other problems that could compromise the integrity of the system.
The Importance of Documentation and Training
Comprehensive documentation and training are essential for ensuring the safe and efficient operation of gas piping & distribution systems. Documentation provides a record of the system's design, installation, maintenance, and any repairs or modifications. Training ensures that personnel are familiar with the system, its operation, and the safety procedures involved.
1. System Documentation: A Comprehensive Record
System documentation should include a detailed description of the gas piping & distribution system, including its design, installation, and any modifications. It should also include a record of all maintenance activities, including inspections, pressure testing, leak detection, and repairs. This documentation should be readily available to all personnel who work with the system.
Documentation is essential for ensuring that the system is properly maintained and that any problems are addressed promptly. It also provides a valuable resource for troubleshooting and for planning future maintenance activities.
2. Training Programs: Equipping Personnel with Knowledge
Training programs should be developed to ensure that all personnel who work with the gas piping & distribution system are familiar with its operation and the safety procedures involved. Training should cover topics such as the system's design, installation, maintenance, and emergency procedures.
Training programs should be tailored to the specific needs of the personnel involved, and they should be conducted on a regular basis to ensure that personnel stay up-to-date on the latest safety procedures and best practices. Training should also include hands-on experience with the system, to ensure that personnel are comfortable operating and maintaining it.
Safety Considerations for Gas Piping & Distribution Systems
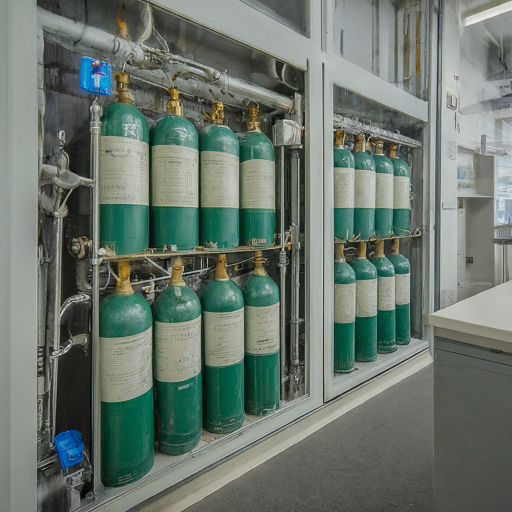
Gas piping & distribution systems pose a number of safety hazards, and it is essential to take steps to mitigate these risks. These hazards can include leaks, fires, explosions, and asphyxiation. It is important to follow all safety procedures and to be aware of the potential hazards associated with these systems.
1. Leak Detection and Prevention: Minimizing Risk
Leaks are a common problem in gas piping & distribution systems, and they can pose a significant safety hazard. Leaks can occur in any part of the system, and they can be caused by a variety of factors, including corrosion, damage, or improper installation.
Leak detection and prevention are essential for ensuring the safety of personnel and the laboratory. This involves regularly inspecting the system for signs of leaks, using leak detection equipment, and taking steps to prevent leaks from occurring in the first place. This may involve using high-quality materials, properly installing the system, and regularly maintaining the components.
2. Fire and Explosion Prevention: Reducing Ignition Sources
Fires and explosions can occur in laboratories where flammable gases are used. These hazards can be caused by a variety of factors, including leaks, ignition sources, and improper ventilation.
Fire and explosion prevention is essential for ensuring the safety of personnel and the laboratory. This involves taking steps to prevent leaks, eliminating ignition sources, and ensuring adequate ventilation. This may involve using explosion-proof equipment, properly storing flammable gases, and providing adequate ventilation in the laboratory.
3. Asphyxiation Prevention: Ensuring Adequate Ventilation
Asphyxiation can occur in laboratories where gases are used, particularly if the gases are heavier than air and can displace oxygen. This hazard can be caused by leaks, poor ventilation, or the accumulation of gases in confined spaces.
Asphyxiation prevention is essential for ensuring the safety of personnel. This involves ensuring adequate ventilation in the laboratory, using gas detectors to monitor for leaks, and providing emergency procedures for dealing with asphyxiation events.
4. Emergency Procedures: Preparing for the Unexpected
Emergency procedures should be developed for dealing with accidents or incidents involving gas piping & distribution systems. These procedures should include steps for evacuating the laboratory, shutting off the gas supply, and contacting emergency services.
Emergency procedures should be clearly communicated to all personnel who work with the gas piping & distribution system, and they should be practiced regularly to ensure that personnel are familiar with them. Emergency procedures should also be posted in a prominent location in the laboratory.
Conclusion
Gas piping & distribution systems are essential infrastructure in laboratories, providing a reliable and controlled supply of gases that are vital for a wide range of applications. However, these systems also pose a number of safety hazards, and it is essential to take steps to mitigate these risks. A comprehensive maintenance program, including preventative maintenance, corrective maintenance, and ongoing monitoring, is essential for ensuring the long-term reliability and safety of these systems. Proper documentation and training are also crucial for ensuring that personnel are familiar with the system, its operation, and the safety procedures involved.
By following the best practices outlined in this article, laboratories can ensure that their gas piping & distribution systems operate safely and efficiently, supporting the critical research and development activities that drive innovation and progress.
Products You may Like
Check out other IT- Tech product that suit your taste
Subscribe to our newsletter
Stay updated with IT-Tech Insights
Related posts
Check out other IT- Tech Scientific Resources
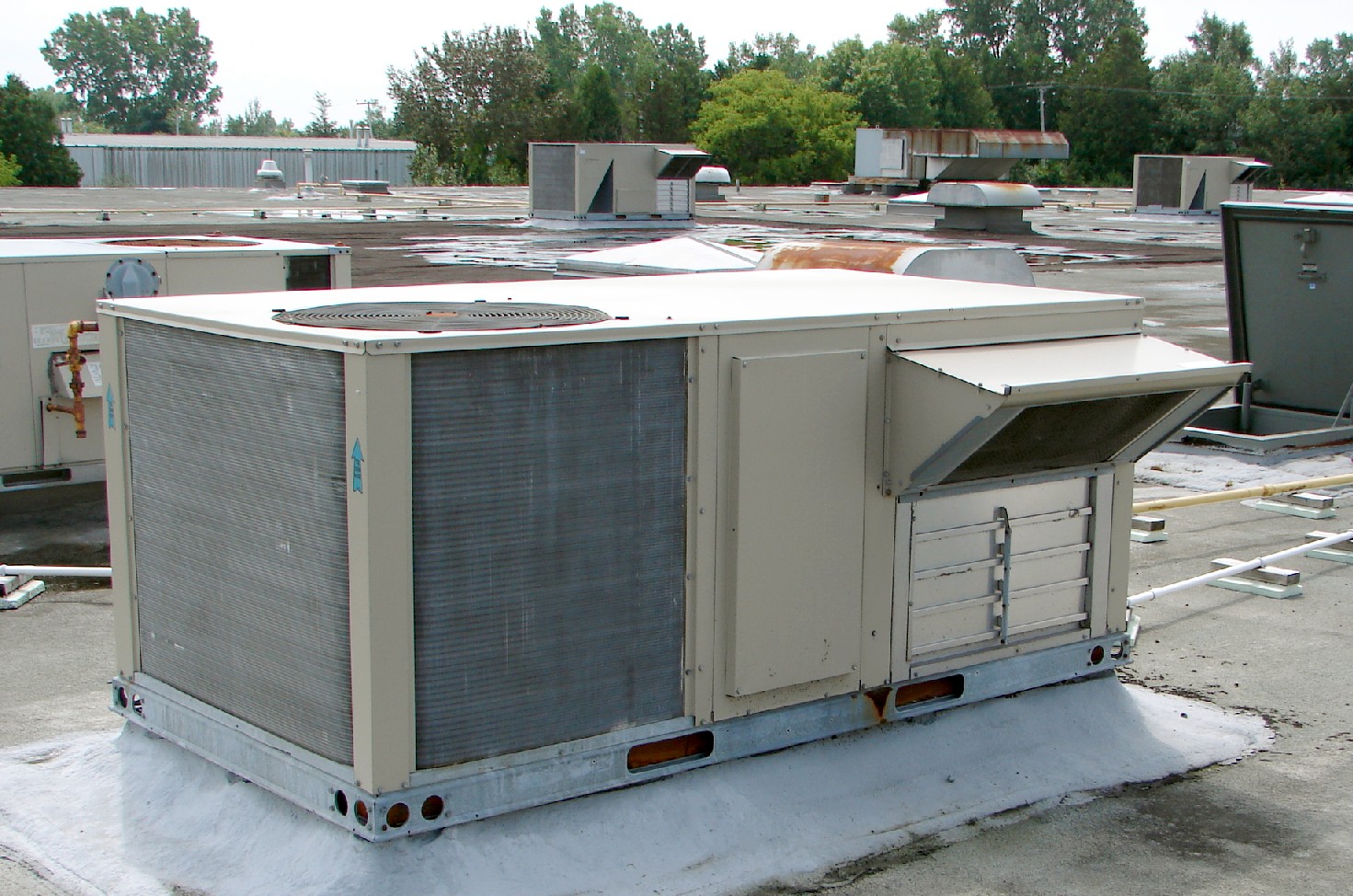
Conventional vs specialized HVAC units
This article delves into the distinctions between conventional and specialized HVAC units, focusing on their suitability for different research environments. Conventional HVAC systems are generally cost-effective and suitable for standard lab operations. Specialized units, on the other hand, offer precise temperature and humidity control, making them ideal for sensitive research applications. The article discusses factors to consider when selecting an HVAC system, including the type of research conducted, the required temperature and humidity ranges, and the budget. It aims to provide researchers with a comprehensive understanding of the available options and help them make informed decisions for their lab's HVAC needs.
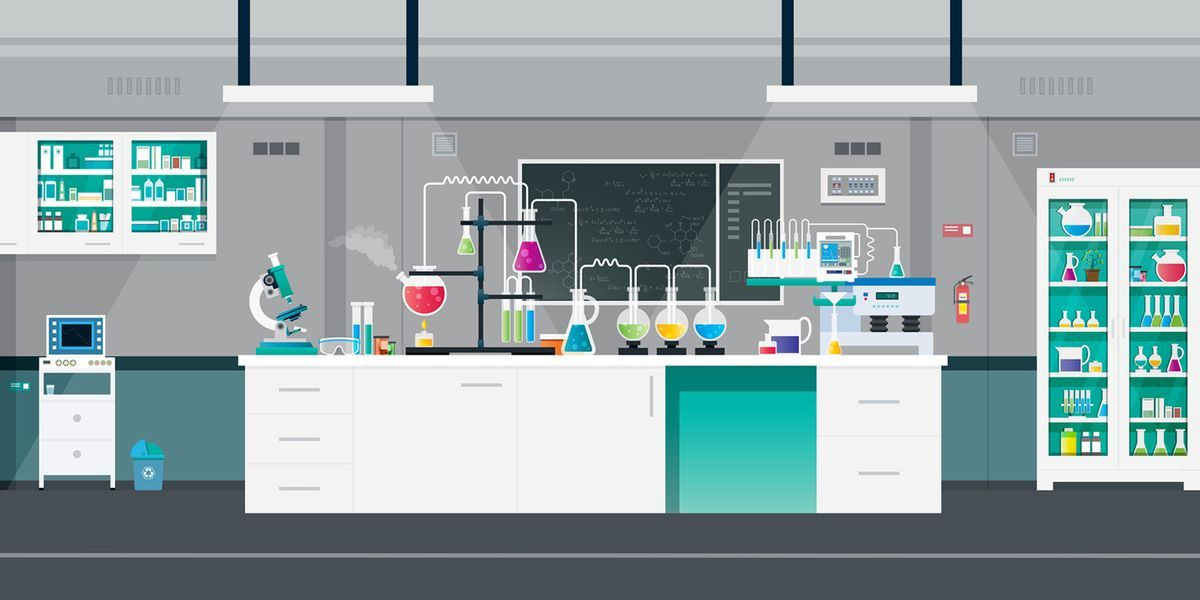
Resolving lab furniture and casework issues
Laboratory furniture and casework play a crucial role in the functionality and safety of any research facility. Over time, these elements can experience wear and tear, leading to various issues. This article offers a comprehensive guide to troubleshooting common problems, covering everything from drawer malfunctions to unstable work surfaces. By understanding the root causes and implementing effective solutions, you can ensure your lab furniture remains in optimal condition, promoting a productive and secure research environment. From identifying potential hazards to optimizing storage solutions, this guide empowers you to address issues proactively and maintain a high standard of laboratory operations.
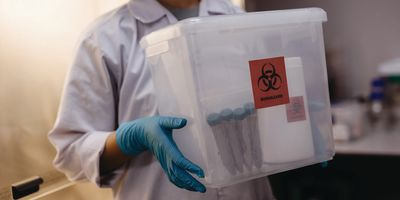
Resolving contamination in lab gas supply
Contamination in lab gas supply can be a major headache for researchers. It can lead to inaccurate results, wasted time and resources, and even compromise the safety of your lab. This article will guide you through the process of troubleshooting and resolving contamination issues in your gas supply system. We'll cover common sources of contamination, how to identify them, and effective solutions to ensure reliable and pure gas delivery for your experiments. From checking gas cylinders and regulators to inspecting tubing and fittings, we'll provide practical tips and best practices to maintain the integrity of your Gas Piping & Distribution Systems.