Proper installation and validation of gas systems
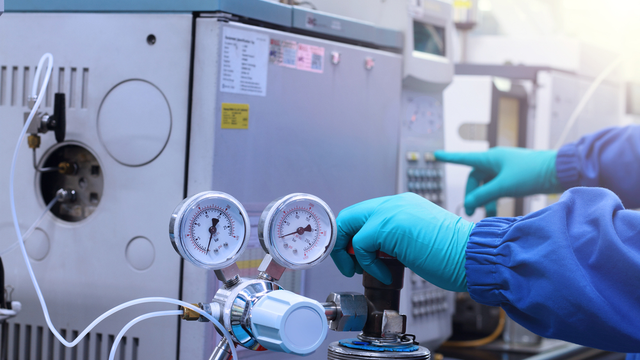
The Crucial Role of Gas Systems in Scientific Laboratories
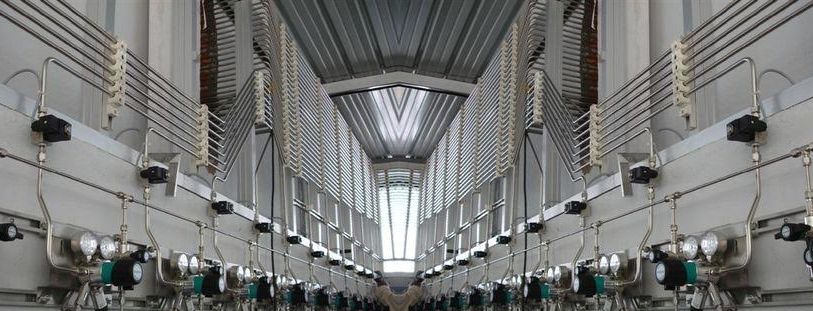
In the realm of scientific research, laboratories serve as the epicenter of innovation, where groundbreaking discoveries are made and advancements in various fields are propelled forward. These laboratories are often equipped with sophisticated instruments and technologies, many of which rely on the precise and reliable delivery of gases. From the delicate analysis of samples in chromatography to the intricate processes of cell culture and material synthesis, gas systems play a pivotal role in ensuring the accuracy, efficiency, and safety of scientific endeavors.
The importance of gas systems in laboratories cannot be overstated. These systems are responsible for supplying a wide range of gases, including nitrogen, oxygen, helium, argon, and hydrogen, which are essential for a multitude of applications. The integrity and functionality of these gas systems are paramount, as any malfunction or failure can have serious consequences, ranging from compromised experimental results to potential safety hazards.
The use of gases in laboratories presents a unique set of challenges, particularly in terms of safety. Gases can be flammable, toxic, or corrosive, and their improper handling or storage can lead to accidents, injuries, or even fatalities. Therefore, it is imperative that gas systems are installed, validated, and maintained according to the highest safety standards.
The installation and validation of gas systems are critical steps in ensuring their safe and reliable operation. Proper installation involves the careful selection and placement of components, such as gas cylinders, regulators, manifolds, and piping, to minimize the risk of leaks, spills, or other hazards. Validation, on the other hand, involves a comprehensive assessment of the system's performance and compliance with established safety protocols.
The process of validating a gas system typically involves a series of tests and inspections to verify that the system meets the required specifications and operates within acceptable safety limits. These tests may include leak detection, pressure testing, flow rate verification, and purity analysis. The validation process also involves documenting the results of these tests and ensuring that the system is properly labeled and maintained.
The importance of proper installation and validation of gas systems cannot be overemphasized. These processes are essential for ensuring the safety of laboratory personnel, protecting the integrity of research data, and minimizing the risk of accidents or incidents. By adhering to established guidelines and best practices, laboratories can create a safe and reliable environment for conducting scientific research.
This article will delve into the intricacies of proper installation and validation of gas systems, providing a comprehensive guide for laboratory technicians, project managers, procurement managers, and C-suites in the scientific industry. We will explore the key considerations, best practices, and regulatory requirements for ensuring the safe and efficient operation of gas systems in laboratories.
The article will also address the importance of ongoing maintenance and inspection programs to ensure that gas systems remain in compliance with safety standards and continue to operate reliably over time. By understanding the principles and procedures outlined in this article, stakeholders in the scientific industry can contribute to a safer and more productive laboratory environment.
The Importance of Gas Piping & Distribution Systems
Gas piping & distribution systems are the backbone of any laboratory that utilizes gases for its operations. These systems are responsible for transporting gases from their source, typically gas cylinders, to the various points of use within the laboratory. The design, installation, and maintenance of these systems are crucial for ensuring the safe and reliable delivery of gases to laboratory equipment and instruments.
The complexity of gas piping & distribution systems can vary depending on the size and requirements of the laboratory. However, all systems share the common goal of providing a safe and efficient means of delivering gases to their intended destinations. The design of these systems must take into account factors such as the types of gases being used, the flow rates required, the pressure requirements, and the potential hazards associated with the gases.
The materials used in gas piping & distribution systems are also critical for ensuring safety and reliability. The pipes, fittings, and valves must be compatible with the gases being transported and must be able to withstand the pressures and temperatures involved. The use of high-quality materials and components is essential for preventing leaks, corrosion, and other problems that could compromise the integrity of the system.
In addition to the physical components of the system, the installation and maintenance of gas piping & distribution systems are equally important. Proper installation involves ensuring that the pipes are properly routed, supported, and connected, and that all fittings and valves are properly installed and tested. Regular maintenance involves inspecting the system for leaks, corrosion, and other problems, and performing necessary repairs or replacements.
The importance of gas piping & distribution systems cannot be overstated. These systems are essential for ensuring the safe and reliable delivery of gases to laboratory equipment and instruments, which are critical for conducting research and development activities. By understanding the principles and best practices for designing, installing, and maintaining these systems, laboratories can create a safe and efficient environment for their operations.
The following sections will delve into the specific aspects of gas piping & distribution systems, including the different types of systems, the materials used, the installation process, and the importance of maintenance and inspection. By providing a comprehensive overview of these topics, this article aims to equip laboratory personnel with the knowledge and skills necessary to ensure the safe and reliable operation of gas piping & distribution systems.
The Crucial Role of Gas Piping & Distribution Systems in Laboratory Operations
In the realm of scientific research and development, laboratories serve as the bedrock of innovation, where groundbreaking discoveries and technological advancements are made. These specialized environments rely on a complex interplay of sophisticated equipment, intricate processes, and essential utilities, among which gas piping & distribution systems play a pivotal role. Gas systems are indispensable for a wide array of laboratory applications, ranging from analytical chemistry and life sciences to materials science and pharmaceutical research. They provide a reliable and controlled supply of gases, such as nitrogen, oxygen, hydrogen, helium, and argon, which are essential for various analytical instruments, experimental setups, and process control.
The proper installation and validation of gas piping & distribution systems are paramount to ensuring the safety, accuracy, and reliability of laboratory operations. A well-designed and meticulously implemented gas system not only guarantees the consistent delivery of high-purity gases but also mitigates potential hazards associated with gas leaks, contamination, and pressure fluctuations. This article delves into the intricacies of gas piping & distribution systems, exploring the critical aspects of installation, validation, and ongoing maintenance, emphasizing the importance of adhering to industry best practices and regulatory guidelines.
Understanding the Importance of Gas Piping & Distribution Systems
Gas piping & distribution systems are the backbone of many laboratory operations, providing a reliable and controlled supply of gases essential for various applications. These systems are typically designed to deliver gases from cylinders or bulk storage tanks to various points of use within the laboratory, ensuring the safe and efficient distribution of these critical resources. The importance of properly installed and validated gas systems cannot be overstated, as they directly impact the following aspects of laboratory operations:
- Safety: Gas leaks can pose significant safety hazards, potentially leading to explosions, fires, or asphyxiation. A well-designed and properly installed gas system minimizes the risk of leaks by incorporating robust materials, leak-tight fittings, and pressure relief devices. Regular inspections and maintenance further enhance safety by identifying and addressing potential issues before they escalate.
- Accuracy and Reliability: The purity and flow rate of gases are critical for many laboratory applications. A properly validated gas system ensures the consistent delivery of gases at the required purity and flow rate, minimizing variations that could compromise experimental results or instrument performance. This is particularly important for sensitive analytical techniques, such as gas chromatography and mass spectrometry, where even slight variations in gas composition can significantly affect data accuracy.
- Efficiency: A well-designed gas system optimizes gas flow and minimizes pressure drops, ensuring efficient delivery of gases to various points of use. This reduces gas consumption and minimizes downtime associated with gas supply interruptions, contributing to overall laboratory efficiency and cost savings.
- Compliance: Regulatory bodies, such as OSHA and NFPA, have established stringent guidelines for the installation and operation of gas systems in laboratories. Adhering to these regulations ensures compliance and minimizes the risk of fines or penalties. Proper documentation of installation, validation, and maintenance activities is essential for demonstrating compliance and ensuring accountability.
Key Considerations for Gas Piping & Distribution System Installation
The installation of a gas piping & distribution system is a complex process that requires careful planning, meticulous execution, and adherence to industry best practices. Several key considerations must be addressed to ensure the system's safety, reliability, and compliance:
1. System Design and Planning
The design and planning phase is crucial for establishing a robust and efficient gas system. This involves a thorough assessment of the laboratory's specific requirements, including the types and quantities of gases needed, the locations of gas outlets, and the desired flow rates. The design should also consider the potential for future expansion and modifications to accommodate evolving research needs. Key aspects of system design include:
- Gas Selection: The choice of gases depends on the specific applications within the laboratory. Common laboratory gases include nitrogen, oxygen, hydrogen, helium, argon, and carbon dioxide. Each gas has unique properties and safety considerations, requiring careful selection based on the intended use.
- Gas Purity: The purity of gases is critical for many laboratory applications, particularly for analytical instruments and sensitive experiments. The design should specify the required purity levels for each gas, ensuring that the system can deliver gases meeting those standards.
- Flow Rates: The flow rates required for different applications vary widely. The design should consider the maximum flow rates needed for each gas outlet, ensuring that the system can deliver the required volumes without excessive pressure drops.
- Pressure Regulation: Gas cylinders and bulk storage tanks typically operate at high pressures. The design should incorporate appropriate pressure regulators to reduce the pressure to safe and usable levels for laboratory applications. Pressure regulators should be selected based on the gas type, pressure range, and flow rate requirements.
- Piping Materials: The choice of piping materials is critical for ensuring the system's safety and reliability. Common materials include copper, stainless steel, and polyethylene. The selection should consider the gas type, pressure, and environmental conditions to ensure compatibility and prevent corrosion or degradation.
- Fittings and Connections: Fittings and connections should be leak-tight and compatible with the piping materials. The design should specify the types of fittings and connections to be used, ensuring that they meet industry standards and safety requirements.
- Gas Detection and Alarm Systems: The design should incorporate gas detection and alarm systems to monitor for leaks and provide timely warnings in case of emergencies. Gas detectors should be selected based on the specific gases used and the sensitivity required for each application.
- Emergency Shut-off Valves: Emergency shut-off valves should be installed at strategic locations within the system to allow for rapid isolation of gas flow in case of leaks or emergencies. These valves should be easily accessible and clearly marked for quick identification and operation.
2. Installation and Commissioning
Once the system design is finalized, the installation and commissioning phase begins. This involves the physical installation of the piping, fittings, regulators, and other components, followed by a series of tests and checks to ensure the system's functionality and safety. Key aspects of installation and commissioning include:
- Installation by Qualified Personnel: The installation of gas piping & distribution systems should be performed by qualified and experienced personnel who are familiar with industry best practices and safety regulations. This ensures that the system is installed correctly and meets all applicable standards.
- Leak Testing: After installation, the system must be thoroughly leak-tested to ensure that all connections are leak-tight. Leak testing can be performed using various methods, such as soap bubble testing, electronic leak detectors, or pressure decay testing. The specific method used should be appropriate for the gas type and pressure range.
- Pressure Testing: Pressure testing is conducted to verify the system's ability to withstand the operating pressures. The system is pressurized to a specified level, and the pressure is monitored for any drops or leaks. Pressure testing is essential for ensuring the system's structural integrity and preventing catastrophic failures.
- Flow Rate Calibration: Flow rate calibration is performed to verify that the system can deliver the required flow rates to each gas outlet. This involves measuring the flow rate at each outlet and adjusting the regulators or other components to achieve the desired flow rates.
- Gas Purity Verification: Gas purity verification is conducted to ensure that the system delivers gases at the required purity levels. This involves sampling the gas at various points in the system and analyzing the purity using appropriate analytical techniques. Gas purity verification is essential for ensuring the accuracy and reliability of laboratory experiments.
- Documentation: All installation, testing, and commissioning activities should be thoroughly documented. This documentation should include details of the system design, installation procedures, test results, and any modifications or repairs made. Comprehensive documentation is essential for demonstrating compliance, tracking system performance, and facilitating future maintenance or troubleshooting.
Validation of Gas Piping & Distribution Systems
Validation is a critical step in ensuring the safety, reliability, and compliance of gas piping & distribution systems. It involves a comprehensive assessment of the system's performance against predefined criteria and specifications. Validation ensures that the system meets the intended purpose and operates within acceptable limits. Key aspects of gas system validation include:
1. Validation Protocol Development
The first step in validation is to develop a comprehensive protocol that outlines the specific tests and procedures to be performed. The protocol should be tailored to the specific requirements of the gas system, taking into account the types of gases used, the pressure ranges, the flow rates, and the intended applications. The protocol should also specify the acceptance criteria for each test, defining the acceptable limits for performance parameters such as pressure, flow rate, and gas purity.
2. Performance Testing
Performance testing involves evaluating the system's ability to deliver gases at the required purity, pressure, and flow rates. This typically involves a series of tests, including:
- Pressure Testing: Pressure testing is conducted to verify that the system can withstand the operating pressures without leaks or failures. The system is pressurized to a specified level, and the pressure is monitored for any drops or leaks. Pressure testing is essential for ensuring the system's structural integrity and preventing catastrophic failures.
- Flow Rate Testing: Flow rate testing is performed to verify that the system can deliver the required flow rates to each gas outlet. This involves measuring the flow rate at each outlet and comparing the results to the specified flow rates. Flow rate testing ensures that the system can meet the demands of various laboratory applications.
- Gas Purity Testing: Gas purity testing is conducted to ensure that the system delivers gases at the required purity levels. This involves sampling the gas at various points in the system and analyzing the purity using appropriate analytical techniques. Gas purity testing is essential for ensuring the accuracy and reliability of laboratory experiments.
3. Documentation and Reporting
All validation activities should be thoroughly documented, including the validation protocol, test results, and any deviations from the protocol. This documentation should be reviewed and approved by qualified personnel to ensure accuracy and completeness. A comprehensive validation report should be prepared, summarizing the test results and conclusions. The report should also include any recommendations for corrective actions or improvements to the system.
Ongoing Maintenance and Monitoring
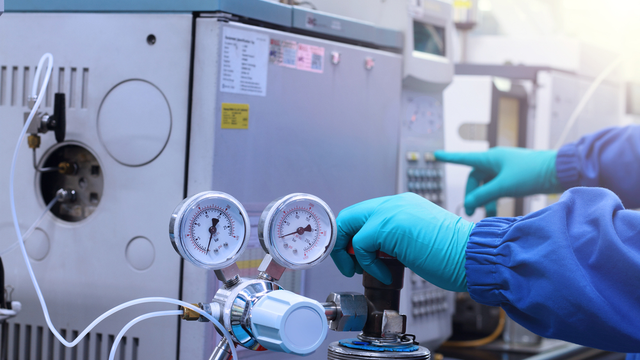
Once a gas piping & distribution system is installed and validated, it is essential to implement a comprehensive maintenance and monitoring program to ensure its continued safety, reliability, and compliance. This program should include regular inspections, preventive maintenance, and corrective actions to address any issues that arise. Key aspects of ongoing maintenance and monitoring include:
1. Regular Inspections
Regular inspections are crucial for identifying potential problems before they escalate into major issues. Inspections should be conducted at least annually, or more frequently if required by regulatory guidelines or based on the system's usage and operating conditions. Inspections should include visual checks for leaks, corrosion, damage, or other signs of deterioration. The condition of pressure regulators, valves, and other components should also be assessed.
2. Preventive Maintenance
Preventive maintenance involves performing routine tasks to maintain the system's functionality and prevent failures. This may include tasks such as:
- Leak Testing: Regular leak testing is essential for identifying and addressing leaks before they become safety hazards. Leak testing can be performed using various methods, such as soap bubble testing, electronic leak detectors, or pressure decay testing.
- Pressure Regulator Calibration: Pressure regulators should be calibrated regularly to ensure that they are delivering the correct pressures. Calibration involves adjusting the regulator to deliver a specific pressure and verifying the accuracy of the adjustment.
- Valve Lubrication: Valves should be lubricated regularly to prevent sticking or seizing. Lubrication helps to ensure smooth operation and prevents wear and tear on the valve components.
- Gas Cylinder Inspection: Gas cylinders should be inspected regularly for damage, corrosion, or other signs of deterioration. Cylinders should be replaced if they show signs of damage or if they have reached their expiration date.
3. Corrective Actions
Corrective actions are taken to address any issues identified during inspections or maintenance activities. This may involve repairing leaks, replacing damaged components, or adjusting system settings. Corrective actions should be documented and reviewed to ensure that they are effective and that the system is restored to a safe and operational state.
4. Monitoring Systems
Monitoring systems can be used to continuously track the performance of the gas piping & distribution system. These systems can monitor pressure, flow rate, gas purity, and other parameters, providing real-time data that can be used to identify potential problems and ensure the system's safe and reliable operation. Monitoring systems can also provide alerts in case of leaks, pressure fluctuations, or other anomalies, allowing for prompt corrective actions.
Best Practices for Gas Piping & Distribution Systems
Adhering to industry best practices is essential for ensuring the safety, reliability, and compliance of gas piping & distribution systems. These best practices are based on years of experience and research, and they have been proven to minimize risks and optimize system performance. Key best practices include:
1. Design and Installation
- Use Qualified Personnel: The design and installation of gas systems should be performed by qualified and experienced personnel who are familiar with industry best practices and safety regulations.
- Follow Industry Standards: The design and installation should adhere to relevant industry standards, such as NFPA, ASME, and ANSI. These standards provide guidelines for materials, construction, testing, and safety requirements.
- Use High-Quality Materials: The system should be constructed using high-quality materials that are compatible with the gases being used and the operating conditions. Materials should be resistant to corrosion, degradation, and leaks.
- Properly Size Piping: The piping should be properly sized to ensure adequate flow rates and minimize pressure drops. Oversized piping can lead to excessive pressure drops, while undersized piping can restrict flow and cause pressure fluctuations.
- Use Leak-Tight Fittings: All fittings and connections should be leak-tight and compatible with the piping materials. Fittings should be properly installed and tightened to ensure a secure seal.
- Install Pressure Relief Devices: Pressure relief devices should be installed to protect the system from overpressure conditions. These devices should be properly sized and located to ensure effective operation.
- Use Gas Detection Systems: Gas detection systems should be installed to monitor for leaks and provide timely warnings in case of emergencies. Detectors should be selected based on the specific gases used and the sensitivity required for each application.
- Install Emergency Shut-off Valves: Emergency shut-off valves should be installed at strategic locations within the system to allow for rapid isolation of gas flow in case of leaks or emergencies. These valves should be easily accessible and clearly marked for quick identification and operation.
2. Validation and Maintenance
- Develop a Comprehensive Validation Protocol: A comprehensive validation protocol should be developed to outline the specific tests and procedures to be performed. The protocol should be tailored to the specific requirements of the gas system and should specify the acceptance criteria for each test.
- Perform Regular Inspections: Regular inspections should be conducted to identify potential problems before they escalate into major issues. Inspections should include visual checks for leaks, corrosion, damage, or other signs of deterioration.
- Implement a Preventive Maintenance Program: A preventive maintenance program should be implemented to perform routine tasks to maintain the system's functionality and prevent failures. This may include tasks such as leak testing, pressure regulator calibration, valve lubrication, and gas cylinder inspection.
- Document All Activities: All validation, inspection, and maintenance activities should be thoroughly documented. This documentation should include details of the system design, installation procedures, test results, and any modifications or repairs made.
3. Safety and Compliance
- Follow Safety Regulations: All gas system operations should comply with relevant safety regulations, such as OSHA and NFPA. These regulations provide guidelines for handling gases, preventing leaks, and responding to emergencies.
- Train Personnel: All personnel who work with gas systems should be properly trained on safety procedures, emergency response, and the operation of the system. Training should be conducted by qualified instructors and should be documented.
- Provide Emergency Equipment: Emergency equipment, such as fire extinguishers, gas masks, and first aid kits, should be readily available in case of emergencies. This equipment should be regularly inspected and maintained to ensure its functionality.
- Develop Emergency Response Plans: Emergency response plans should be developed and practiced to ensure that personnel know how to respond to leaks, fires, or other emergencies. Plans should include procedures for evacuating the area, contacting emergency services, and providing first aid.
Conclusion
Proper installation, validation, and ongoing maintenance of gas piping & distribution systems are essential for ensuring the safety, accuracy, and reliability of laboratory operations. By adhering to industry best practices and regulatory guidelines, laboratories can minimize risks, optimize system performance, and ensure the continued success of their research and development activities. A well-designed and meticulously implemented gas system not only guarantees the consistent delivery of high-purity gases but also mitigates potential hazards associated with gas leaks, contamination, and pressure fluctuations. This article has provided a comprehensive overview of the critical aspects of gas piping & distribution systems, emphasizing the importance of a proactive approach to safety, compliance, and ongoing maintenance.
Ensuring a Safe and Compliant Gas System: A Recap
The journey towards a safe and compliant gas system is a multifaceted one, demanding meticulous attention to detail at every stage. From the initial planning and design to the final validation and ongoing maintenance, each step plays a crucial role in ensuring the integrity and reliability of your gas infrastructure. This article has delved into the critical aspects of proper installation and validation, highlighting the importance of adhering to established standards and best practices.
We've explored the significance of a comprehensive risk assessment, emphasizing the need to identify potential hazards and implement appropriate mitigation strategies. The importance of selecting the right materials and components, ensuring their compatibility and suitability for the specific application, has been underscored. The article has also emphasized the crucial role of proper installation techniques, including the use of qualified personnel, adherence to manufacturer's instructions, and thorough leak testing.
Validation, a cornerstone of ensuring system integrity, has been discussed in detail. We've explored the various validation methods, including pressure testing, leak detection, and functional testing, highlighting their specific purposes and the importance of documenting the results. The article has also emphasized the need for ongoing maintenance and periodic re-validation, ensuring the system remains compliant and operates safely over its lifespan.
Beyond the technical aspects, we've also touched upon the importance of clear communication and documentation. Maintaining accurate records of system design, installation, validation, and maintenance is crucial for ensuring accountability, facilitating future troubleshooting, and demonstrating compliance to regulatory bodies.
By adhering to the principles outlined in this article, you can significantly enhance the safety, reliability, and compliance of your gas system. Remember, a well-designed, properly installed, and regularly validated gas system is not just a technical requirement; it's a commitment to the safety and well-being of your personnel, the integrity of your research, and the overall success of your scientific endeavors.
Moving Forward: A Call to Action
The journey towards a safe and compliant gas system doesn't end with this article. It's an ongoing process that requires continuous vigilance and proactive action. As you embark on this journey, IT Tech stands ready to be your trusted partner, providing the expertise, products, and services you need to achieve your goals.
Our comprehensive portfolio of Gas Piping & Distribution Systems encompasses a wide range of high-quality consumables and equipment, designed to meet the specific needs of your laboratory. From high-purity gas cylinders and regulators to specialized fittings and tubing, we offer a complete solution for your gas infrastructure.
Beyond our product offerings, IT Tech provides expert technical support and guidance, ensuring you have the knowledge and resources to design, install, and maintain a safe and compliant gas system. Our team of experienced professionals can assist you with:
- System design and engineering
- Installation and commissioning
- Validation and qualification
- Maintenance and repair
- Regulatory compliance support
We understand that every laboratory has unique requirements. That's why we offer customized solutions tailored to your specific needs, ensuring optimal performance and compliance.
Don't wait for a potential incident to occur. Take proactive steps today to ensure the safety and reliability of your gas system. Contact IT Tech today to discuss your specific requirements and explore how we can help you achieve your goals.
Submit an enquiry and let IT Tech be your partner in building a safe and compliant gas system for your laboratory.
Subscribe to our newsletter
Stay updated with IT-Tech Insights
Related posts
Check out other IT- Tech Scientific Resources
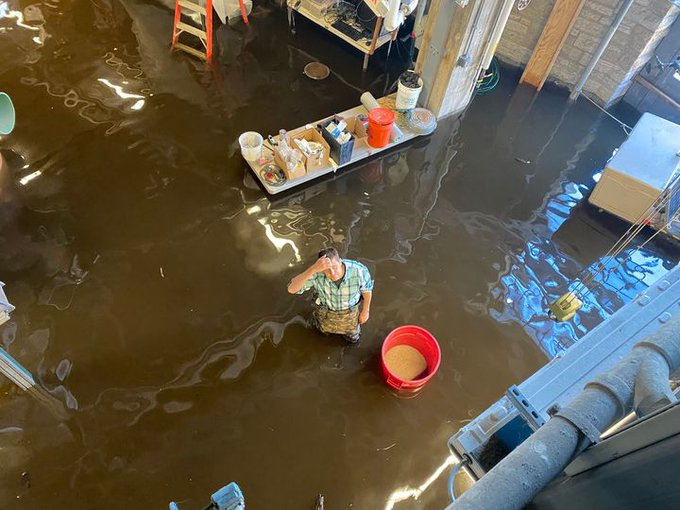
Troubleshooting lab drainage and flooding
Lab drainage and flooding can disrupt operations, damage equipment, and pose safety risks. This article offers a step-by-step approach to troubleshooting these issues, covering common causes like clogged drains, faulty plumbing, and improper disposal practices. We explore preventative measures such as regular maintenance, proper waste disposal, and implementing leak detection systems. By understanding the root causes and implementing effective solutions, labs can minimize downtime, protect valuable equipment, and maintain a safe working environment. This guide is essential for lab managers, technicians, and anyone involved in ensuring the smooth operation of laboratory facilities.
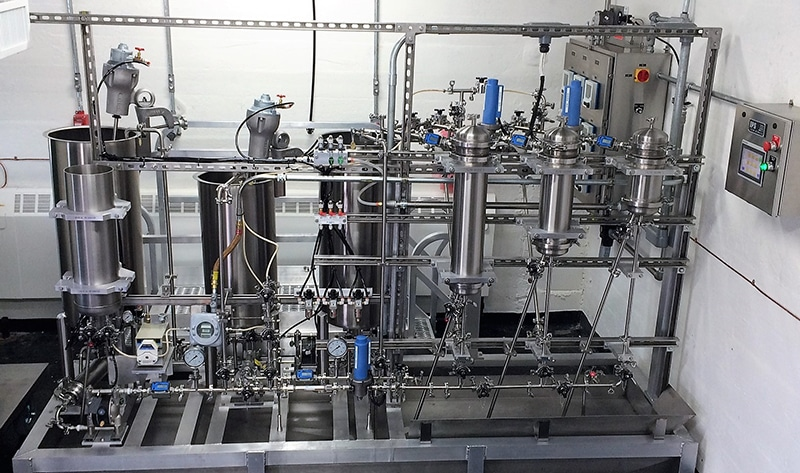
Comparing lab wastewater treatment methods
This article provides a comprehensive comparison of various lab wastewater treatment methods, including chemical, biological, and physical techniques. We delve into the advantages and disadvantages of each method, considering factors such as efficiency, cost, and environmental impact. The article also discusses the importance of complying with regulations and ensuring the safety of lab wastewater discharge. By understanding the different treatment options, researchers can make informed decisions about the most suitable method for their specific needs and contribute to responsible waste management practices.
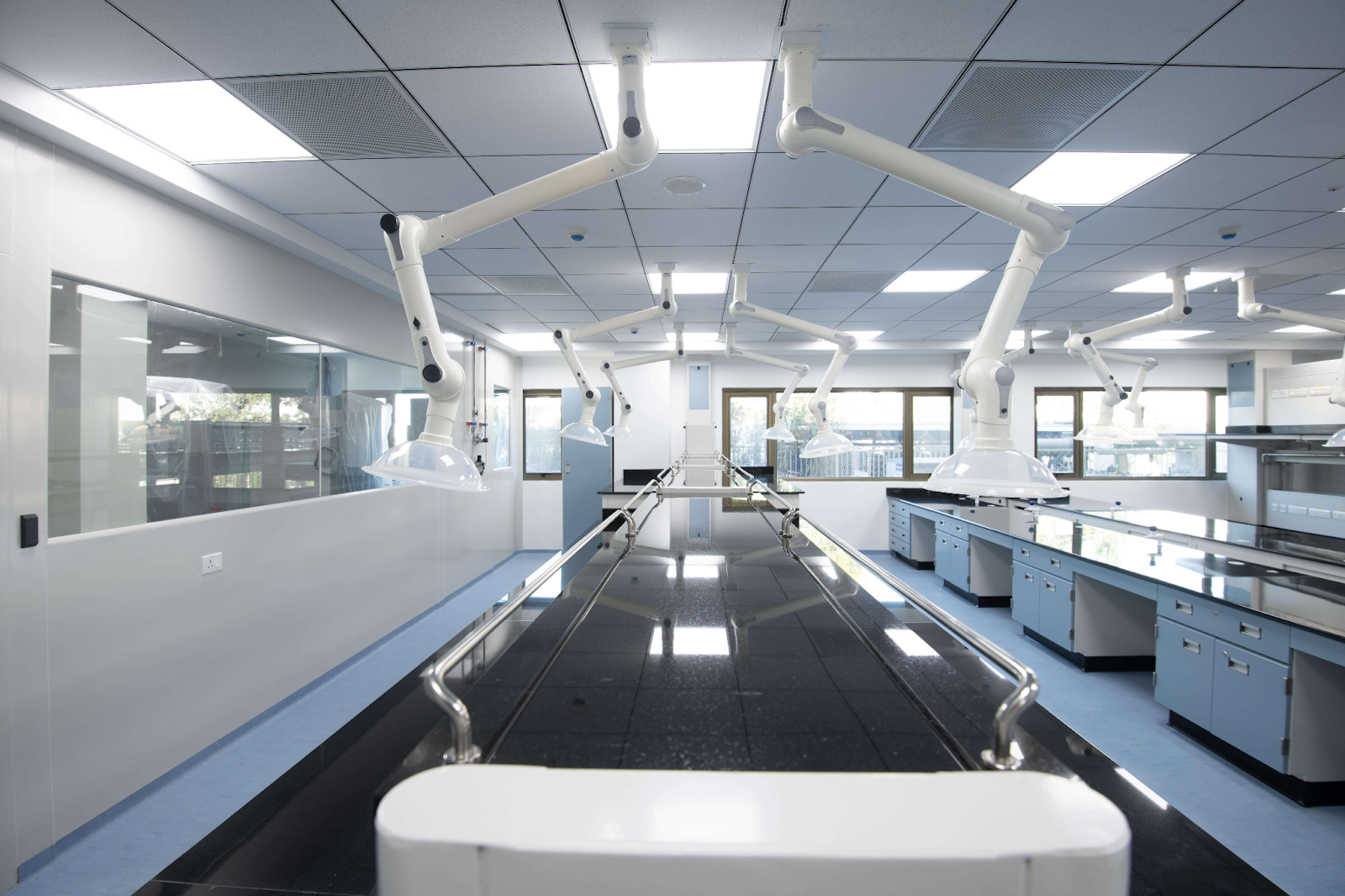
Selecting HVAC capacity for lab space
Maintaining a controlled environment is essential for accurate and reliable research in a laboratory setting. HVAC systems play a vital role in regulating temperature, humidity, and air quality, impacting the success of experiments and the safety of personnel. This article explores the factors to consider when selecting the appropriate HVAC capacity for your lab space. Key considerations include the size of the lab, the types of experiments conducted, the number of personnel, and the specific environmental requirements for sensitive equipment and materials. By carefully evaluating these factors, you can ensure that your lab has the right HVAC system to support your research needs and maintain a safe and productive environment.