Resolving vacuum system failures
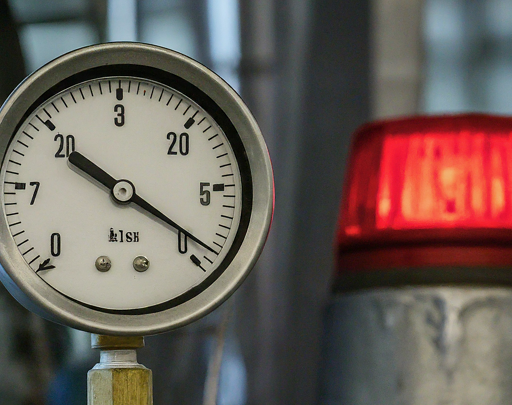
A Deep Dive into Vacuum System Failures: A Comprehensive Guide for Lab Professionals
In the realm of scientific research and development, vacuum systems are indispensable tools, playing a pivotal role in a wide array of applications. From material science and nanotechnology to pharmaceutical research and biotechnology, vacuum systems are essential for creating controlled environments, manipulating materials, and conducting precise experiments. However, the intricate nature of these systems makes them susceptible to failures, which can significantly disrupt research progress, incur substantial financial losses, and even compromise the safety of lab personnel.
The consequences of vacuum system failures can be far-reaching, impacting not only the immediate research project but also the overall efficiency and productivity of the laboratory. Downtime associated with system repairs can lead to delays in experiments, missed deadlines, and compromised data integrity. Moreover, the financial implications of system failures can be significant, encompassing repair costs, replacement parts, and lost research funding. In extreme cases, vacuum system failures can pose safety hazards, leading to potential injuries or even environmental contamination.
The complexity of vacuum systems, coupled with the diverse range of applications they serve, makes troubleshooting and resolving failures a challenging task. A comprehensive understanding of the underlying principles of vacuum technology, the various components involved, and the common causes of failures is crucial for effective troubleshooting. This article aims to provide a comprehensive guide for lab technicians, project managers, procurement managers, and C-suites in the scientific industry, equipping them with the knowledge and tools necessary to identify, diagnose, and resolve vacuum system failures efficiently and effectively.
This guide will delve into the intricacies of vacuum systems, exploring the fundamental principles of vacuum generation, the different types of vacuum pumps and their applications, and the common causes of system failures. We will examine the role of proper maintenance and preventative measures in minimizing the risk of failures. Furthermore, we will provide practical troubleshooting strategies, covering the identification of symptoms, the use of diagnostic tools, and the implementation of effective repair techniques. By equipping lab professionals with this knowledge, we aim to empower them to address vacuum system failures proactively, minimizing downtime, reducing costs, and ensuring the smooth operation of research activities.
The importance of reliable vacuum systems in scientific research cannot be overstated. Their role extends beyond the confines of individual laboratories, impacting the advancement of knowledge, the development of new technologies, and the improvement of public health. By addressing vacuum system failures effectively, we contribute to the overall progress of scientific research, ensuring the continued advancement of knowledge and innovation in various fields, including Public Health Engineering, where the development of new vaccines, treatments, and diagnostic tools relies heavily on the use of vacuum systems.
This article serves as a valuable resource for lab professionals seeking to enhance their understanding of vacuum systems and their troubleshooting capabilities. By equipping them with the knowledge and tools necessary to address system failures effectively, we aim to contribute to the smooth operation of research activities, the advancement of scientific knowledge, and the improvement of public health outcomes.
Understanding Vacuum System Failures: A Comprehensive Guide for Lab Professionals
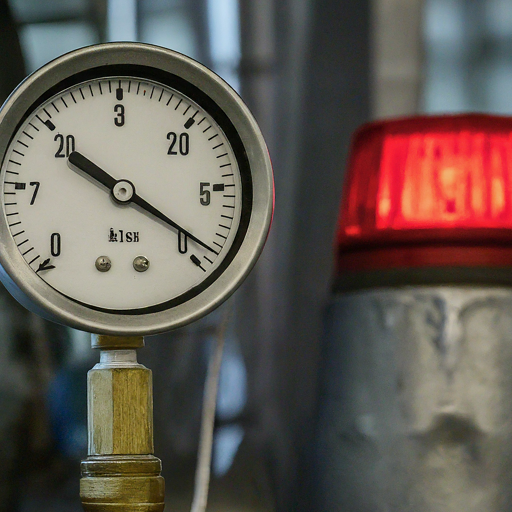
Vacuum systems are indispensable tools in a wide range of scientific disciplines, from chemistry and biology to materials science and engineering. They play a crucial role in various applications, including sample preparation, analytical techniques, and process control. However, these systems are complex and prone to failures, which can significantly disrupt research activities, delay experiments, and compromise data integrity. This article aims to provide a comprehensive guide for lab technicians, project managers, procurement managers, and C-suites in the scientific industry to understand the common causes of vacuum system failures, troubleshoot these issues effectively, and implement preventive measures to ensure optimal performance and longevity.
The Importance of Vacuum Systems in Scientific Research
Vacuum systems are essential for a variety of scientific applications, particularly in research and development. They create a controlled environment with reduced pressure, which allows for various processes and experiments to be conducted with greater precision and accuracy. Here are some key applications of vacuum systems in scientific research:
- Sample Preparation: Vacuum systems are widely used in sample preparation techniques, such as drying, degassing, and concentration. For instance, in analytical chemistry, vacuum drying is employed to remove solvents from samples before analysis. In materials science, vacuum degassing is used to remove trapped gases from materials, improving their properties.
- Analytical Techniques: Many analytical techniques rely on vacuum systems to create a controlled environment for measurements. For example, in mass spectrometry, vacuum is used to create a high-vacuum environment that allows for the separation and identification of ions. In electron microscopy, vacuum is essential to prevent scattering of electrons, ensuring high-resolution imaging.
- Process Control: Vacuum systems are used in various industrial processes, such as thin-film deposition, semiconductor manufacturing, and pharmaceutical production. They provide a controlled environment for precise control of process parameters, ensuring product quality and consistency.
- Public Health Engineering: Vacuum systems play a vital role in public health engineering, particularly in water treatment and wastewater management. They are used in filtration systems to remove contaminants from water, ensuring safe drinking water for communities. In wastewater treatment, vacuum systems are employed in aeration processes to enhance the removal of organic matter and pathogens.
Common Causes of Vacuum System Failures
Vacuum system failures can arise from a variety of factors, ranging from mechanical issues to environmental conditions. Understanding these causes is crucial for effective troubleshooting and preventive maintenance. Here are some common causes of vacuum system failures:
Mechanical Issues
- Pump Failure: Vacuum pumps are the heart of any vacuum system, and their failure can lead to a complete loss of vacuum. Common pump failures include mechanical wear and tear, contamination, and electrical malfunctions. Regular maintenance and inspection of pumps are essential to prevent these issues.
- Leakage: Leaks in the vacuum system can significantly reduce the system's performance and lead to a loss of vacuum. Leaks can occur at various points, including seals, connections, and chambers. Identifying and repairing leaks promptly is crucial for maintaining system integrity.
- Valve Malfunction: Valves play a critical role in controlling the flow of gases within the vacuum system. Malfunctioning valves can lead to improper vacuum levels, contamination, and system instability. Regular inspection and maintenance of valves are essential to ensure their proper operation.
- System Contamination: Contamination of the vacuum system can lead to reduced performance and premature failure. Sources of contamination include dust, particles, and vapors from the surrounding environment or from the samples being processed. Proper filtration and cleaning procedures are essential to minimize contamination.
Environmental Factors
- Temperature Fluctuations: Extreme temperature fluctuations can affect the performance of vacuum systems, particularly the pumps and seals. Maintaining a stable temperature environment is crucial for optimal system operation.
- Humidity: High humidity levels can lead to condensation within the vacuum system, which can cause corrosion, contamination, and pump failure. Maintaining a low humidity environment is essential for preventing these issues.
- Vibration: Excessive vibration can damage the vacuum system components, particularly the pumps and seals. Isolating the vacuum system from sources of vibration is crucial for its longevity.
Troubleshooting Vacuum System Failures
Troubleshooting vacuum system failures requires a systematic approach that involves identifying the symptoms, isolating the cause, and implementing appropriate solutions. Here are some steps involved in troubleshooting vacuum system failures:
1. Identify the Symptoms
The first step in troubleshooting is to identify the symptoms of the vacuum system failure. This involves observing the system's behavior and noting any deviations from normal operation. Some common symptoms of vacuum system failures include:
- Slow Vacuum Rate: If the vacuum system is taking longer than usual to reach the desired pressure, it could indicate a leak, pump malfunction, or system contamination.
- Vacuum Loss: If the vacuum system is unable to maintain the desired pressure, it could indicate a leak, pump failure, or valve malfunction.
- Unusual Noises: Unusual noises from the vacuum system, such as rattling, grinding, or hissing, could indicate mechanical issues, leaks, or pump problems.
- System Instability: Fluctuations in vacuum pressure or erratic system behavior could indicate leaks, valve malfunctions, or contamination.
2. Isolate the Cause
Once the symptoms have been identified, the next step is to isolate the cause of the failure. This involves systematically checking different components of the vacuum system to identify the source of the problem. Some common methods for isolating the cause include:
- Leak Detection: Leaks can be detected using various methods, such as a leak detector, a pressure gauge, or a soap solution. The leak detector is a sensitive instrument that can detect even small leaks. The pressure gauge can be used to monitor pressure changes over time, indicating a leak. The soap solution can be applied to suspected leak points, and the formation of bubbles indicates a leak.
- Pump Inspection: Inspecting the vacuum pump for signs of wear and tear, contamination, or electrical malfunctions can help identify the cause of pump failure. This includes checking the pump oil level, inspecting the pump bearings, and testing the pump motor.
- Valve Testing: Testing the valves for proper operation can help identify malfunctions. This involves checking the valve seals, testing the valve actuator, and ensuring the valve is opening and closing correctly.
- System Cleaning: Cleaning the vacuum system can help remove contamination and improve performance. This involves removing dust, particles, and vapors from the system using appropriate cleaning procedures.
3. Implement Solutions
Once the cause of the vacuum system failure has been identified, the next step is to implement appropriate solutions. These solutions may involve repairing or replacing faulty components, addressing environmental issues, or implementing preventive maintenance procedures. Some common solutions for vacuum system failures include:
- Repair or Replace Faulty Components: If the cause of the failure is a faulty component, such as a pump, valve, or seal, it may need to be repaired or replaced. Repairing faulty components can be cost-effective, but replacing them may be necessary if the damage is extensive or the component is beyond repair.
- Address Environmental Issues: If the cause of the failure is an environmental issue, such as temperature fluctuations, humidity, or vibration, steps need to be taken to address these issues. This may involve installing temperature control systems, dehumidifiers, or vibration isolation systems.
- Implement Preventive Maintenance: Implementing a regular preventive maintenance program can help prevent vacuum system failures. This program should include regular inspection and cleaning of the system components, as well as replacement of worn or damaged parts. Preventive maintenance can significantly extend the life of the vacuum system and reduce the risk of unexpected failures.
Preventive Maintenance for Vacuum Systems
Preventive maintenance is crucial for ensuring the optimal performance and longevity of vacuum systems. A well-structured maintenance program can help identify potential problems before they become major issues, reducing downtime and minimizing repair costs. Here are some key aspects of a preventive maintenance program for vacuum systems:
1. Regular Inspections
Regular inspections of the vacuum system components are essential for identifying potential problems early on. This includes inspecting the pumps, valves, seals, chambers, and connections for signs of wear and tear, contamination, or damage. The frequency of inspections should be based on the system's usage and the manufacturer's recommendations.
2. Cleaning and Maintenance
Regular cleaning and maintenance of the vacuum system components are crucial for preventing contamination and ensuring optimal performance. This includes cleaning the pumps, valves, chambers, and connections using appropriate cleaning procedures. The frequency of cleaning should be based on the system's usage and the type of materials being processed.
3. Oil Changes
Vacuum pumps require regular oil changes to maintain their performance and prevent damage. The frequency of oil changes should be based on the pump's usage and the manufacturer's recommendations. It is essential to use the correct type of oil for the pump to ensure optimal lubrication and prevent contamination.
4. Calibration and Testing
Regular calibration and testing of the vacuum system components are essential for ensuring accuracy and reliability. This includes calibrating the pressure gauges, testing the valves, and verifying the pump's performance. The frequency of calibration and testing should be based on the system's usage and the manufacturer's recommendations.
5. Documentation
Maintaining accurate documentation of all maintenance activities is essential for tracking the system's history and identifying trends. This documentation should include the date of each maintenance activity, the components inspected or serviced, any issues identified, and the actions taken to resolve them. This documentation can be used to optimize the maintenance program and ensure the system's long-term reliability.
Conclusion
Vacuum systems are essential tools in scientific research and development, but they are complex and prone to failures. Understanding the common causes of vacuum system failures, troubleshooting these issues effectively, and implementing preventive measures are crucial for ensuring optimal performance and longevity. By following the guidelines outlined in this article, lab technicians, project managers, procurement managers, and C-suites in the scientific industry can minimize downtime, reduce repair costs, and ensure the reliable operation of their vacuum systems.
Preventative Maintenance: The Cornerstone of Vacuum System Longevity
The importance of preventative maintenance in ensuring the optimal performance and longevity of your vacuum system cannot be overstated. A well-maintained vacuum system not only operates efficiently but also minimizes the risk of costly breakdowns and downtime. By implementing a comprehensive preventative maintenance program, you can proactively address potential issues before they escalate into major problems, ensuring the smooth and reliable operation of your critical equipment.
Regular inspections, cleaning, and lubrication are essential components of a robust preventative maintenance program. These activities help identify potential problems early on, allowing for timely repairs and minimizing the risk of catastrophic failures. By addressing minor issues before they become major ones, you can significantly extend the lifespan of your vacuum system and reduce the overall cost of ownership.
In addition to routine maintenance, it is crucial to establish a system for tracking and documenting all maintenance activities. This documentation serves as a valuable record of the system's history, providing insights into its performance and identifying any recurring issues. By analyzing this data, you can optimize your maintenance schedule and ensure that your vacuum system receives the attention it needs to operate at peak performance.
Furthermore, investing in high-quality vacuum system components and consumables is essential for maintaining optimal performance. Using genuine parts and consumables from reputable manufacturers ensures compatibility and reliability, minimizing the risk of premature failures and downtime. IT Tech, a leading provider of lab consumables and equipment, offers a wide range of high-quality vacuum system components and consumables, designed to meet the specific needs of your laboratory.
By prioritizing preventative maintenance, you can significantly improve the reliability and longevity of your vacuum system, ensuring its smooth operation and minimizing the risk of costly breakdowns. IT Tech's comprehensive range of products and services, coupled with our expert technical support, can help you establish a robust preventative maintenance program that keeps your vacuum system running at peak performance.
To learn more about IT Tech's comprehensive range of vacuum system components and consumables, and to discuss your specific needs, please submit an enquiry through our website. Our team of experts is ready to assist you in optimizing your vacuum system performance and ensuring its long-term reliability.
Subscribe to our newsletter
Stay updated with IT-Tech Insights
Related posts
Check out other IT- Tech Scientific Resources
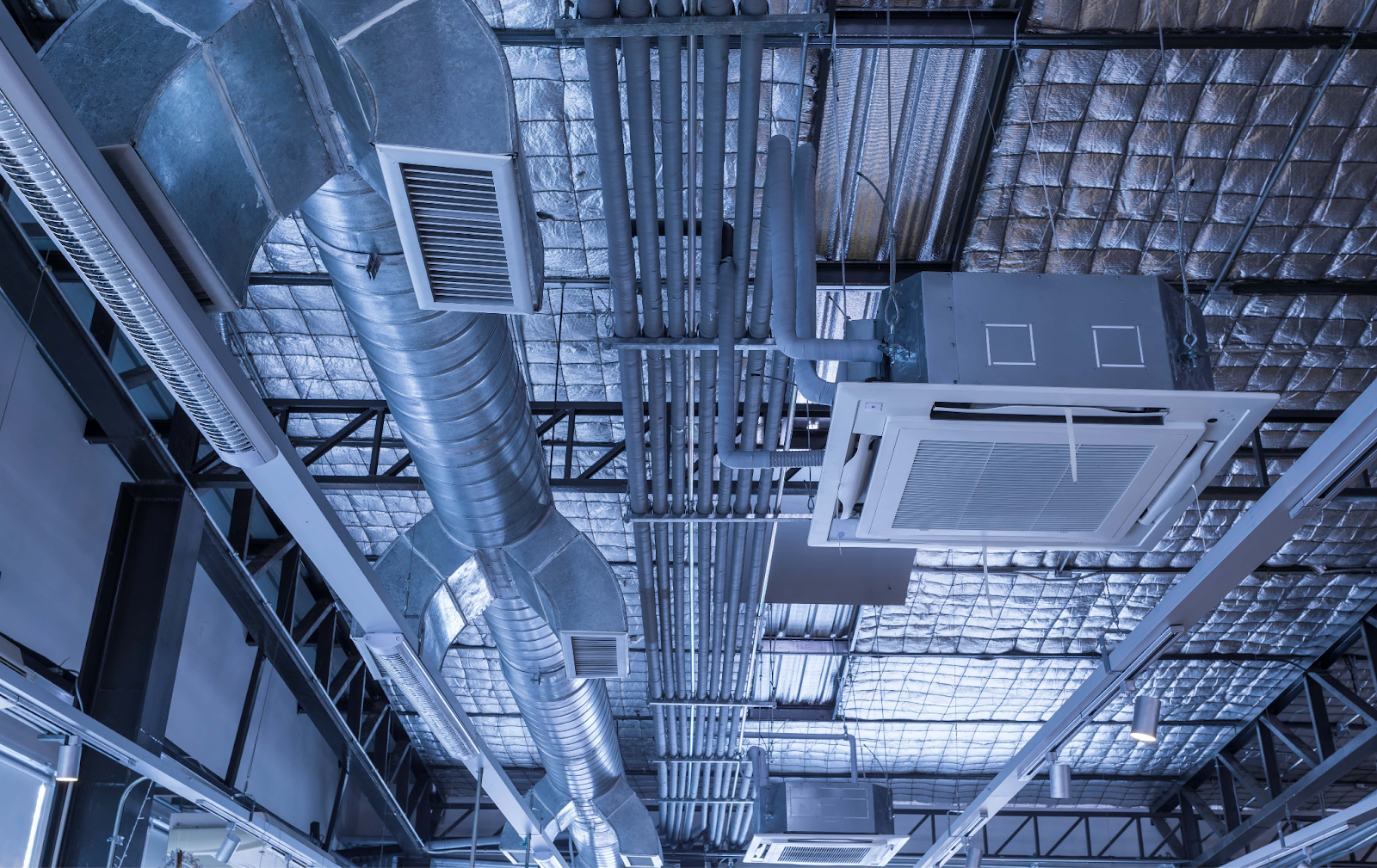
Choosing HVAC controls for lab environments
Maintaining a controlled environment is essential for research labs. HVAC systems play a critical role in regulating temperature, humidity, and air quality, impacting experiment accuracy and safety. This article guides you through key considerations when selecting HVAC controls for your lab. Factors like lab size, equipment sensitivity, and budget are crucial. We explore different HVAC system types, including VAV systems, fan coil units, and dedicated outdoor air systems, highlighting their advantages and disadvantages. By understanding these factors, you can choose the most suitable HVAC system to ensure optimal lab conditions and support your research endeavors.
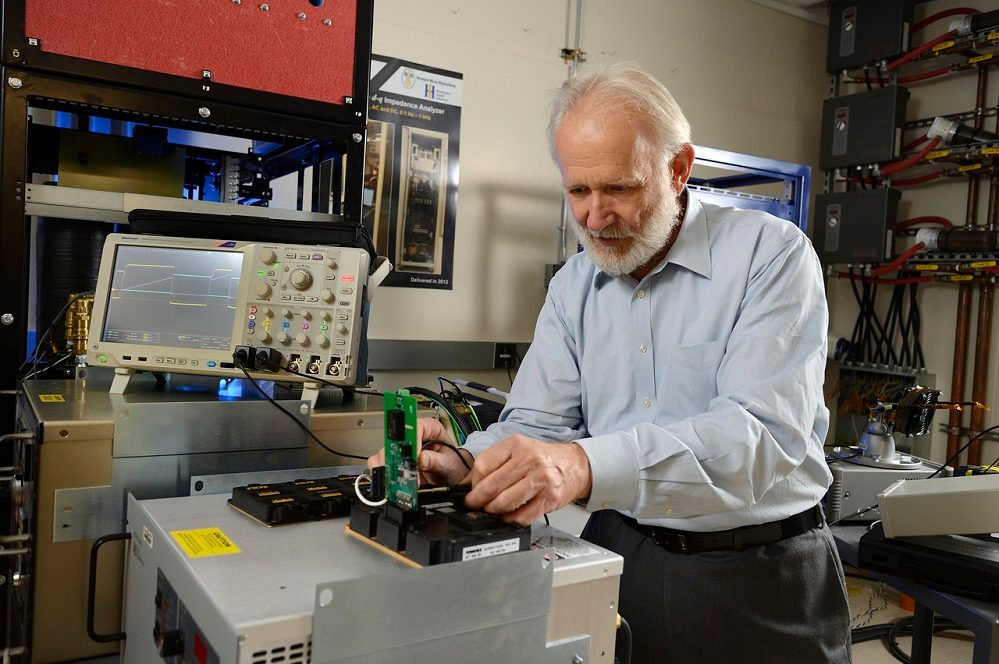
Resolving wiring and grounding issues
Electrical issues can disrupt your lab's workflow and compromise safety. This article focuses on troubleshooting wiring and grounding problems, common culprits behind electrical malfunctions. We'll cover identifying signs of faulty wiring, diagnosing grounding issues, and implementing safe and effective solutions. Whether you're dealing with intermittent power outages, electrical shocks, or equipment malfunctions, this guide will equip you with the knowledge to resolve these problems efficiently and ensure a safe and reliable lab environment.
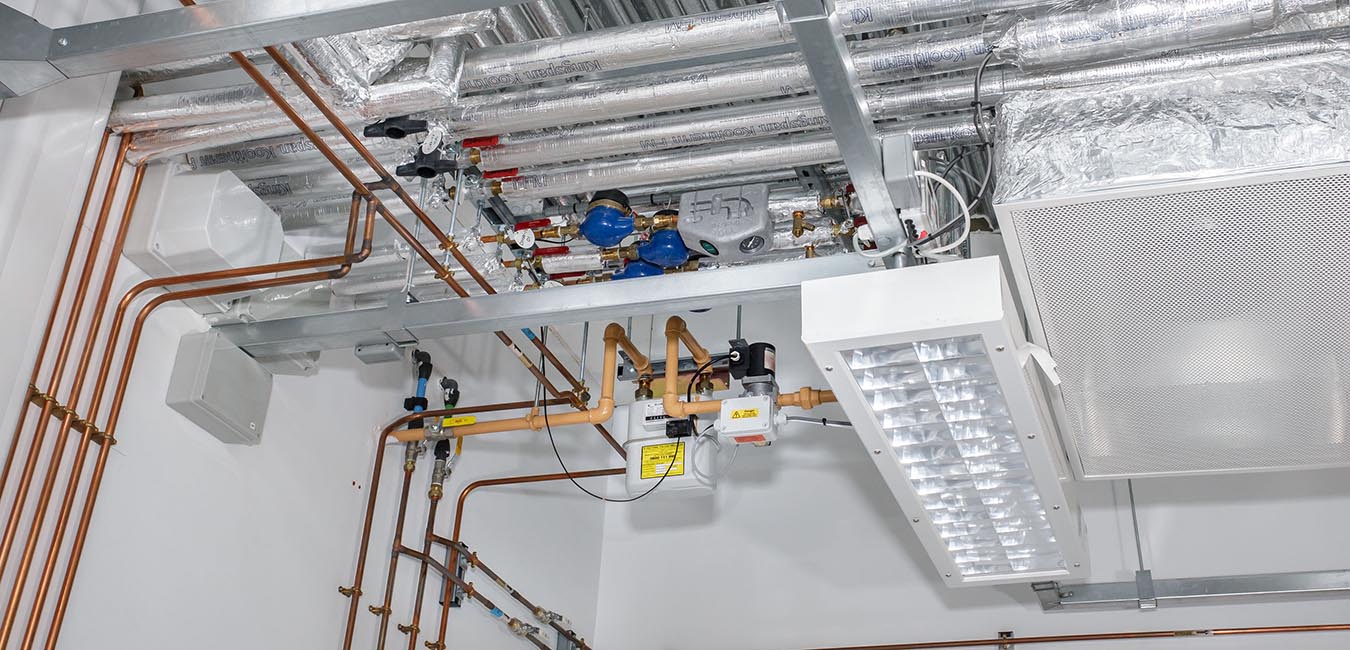
Proper installation of lab plumbing systems
Properly installed lab plumbing systems are crucial for maintaining a safe and efficient laboratory environment. This training module covers essential aspects of lab plumbing installation, including selecting the right materials, understanding code requirements, and ensuring proper connections and drainage. We'll also discuss best practices for minimizing contamination risks and maximizing system longevity. This comprehensive guide is designed to equip Public Health Engineering professionals with the knowledge and skills needed to install and maintain reliable lab plumbing systems.