Troubleshooting false fire alarms
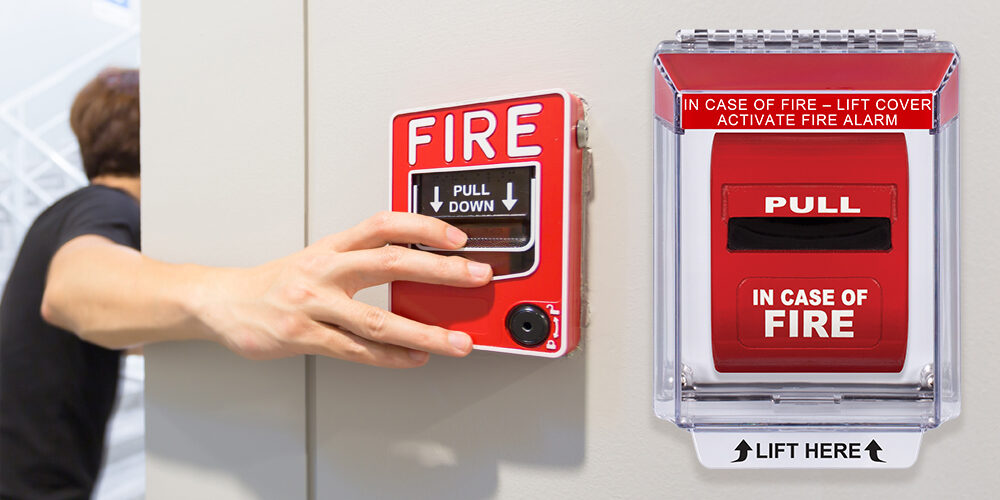
The Silent Disruptor: False Fire Alarms in Labs
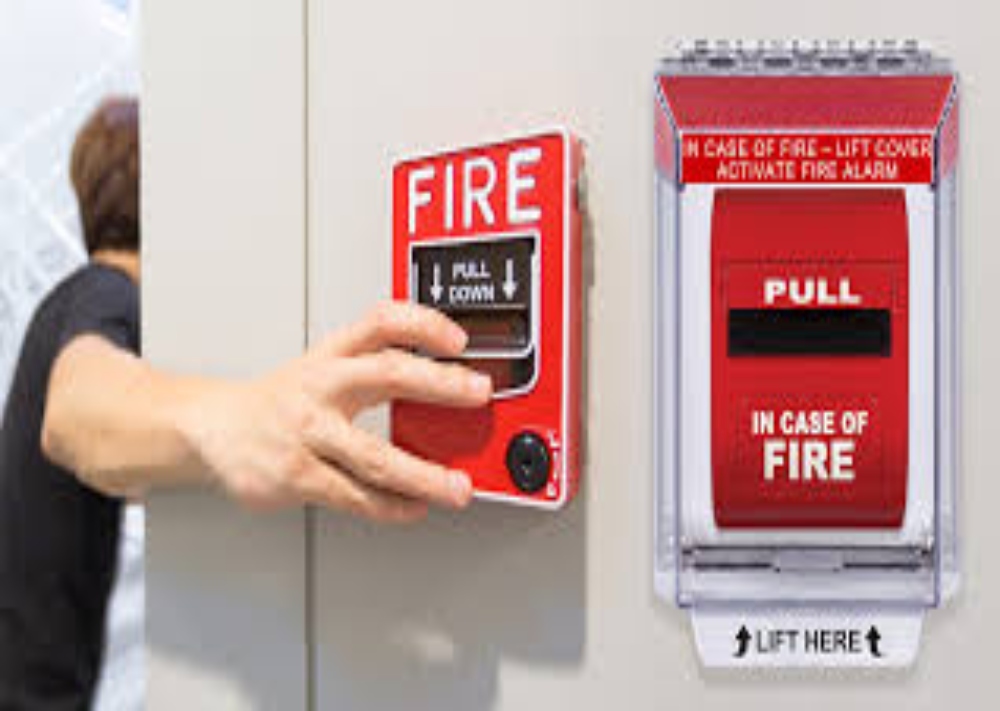
In the meticulously controlled environment of a laboratory, every element is meticulously calibrated for precision and accuracy. From the delicate pipettes to the sophisticated equipment, each component plays a crucial role in the pursuit of scientific discovery. However, amidst this symphony of scientific precision, a silent disruptor lurks – the false fire alarm. These unwelcome interruptions, while seemingly innocuous, can wreak havoc on the delicate balance of a laboratory's operations, disrupting experiments, jeopardizing valuable samples, and ultimately hindering the progress of research.
The consequences of a false fire alarm extend far beyond the immediate inconvenience. The evacuation of a laboratory, often mandated by safety protocols, can lead to the interruption of critical experiments, potentially jeopardizing weeks or even months of meticulous work. Valuable samples, carefully cultivated and nurtured, may be left unattended, risking degradation or contamination. The disruption of the laboratory's workflow can also lead to delays in research projects, impacting timelines and potentially jeopardizing funding opportunities.
Beyond the immediate impact on research, false fire alarms can also have a significant psychological effect on laboratory personnel. The constant threat of a false alarm can create a sense of unease and anxiety, impacting morale and productivity. The disruption of the laboratory's routine can also lead to a sense of frustration and resentment, particularly among researchers who have invested significant time and effort in their projects.
The root causes of false fire alarms in laboratories are often multifaceted, ranging from faulty sensors and equipment malfunctions to human error and environmental factors. Identifying the underlying causes is crucial for developing effective strategies to mitigate the risk of these disruptive events. This article delves into the intricacies of false fire alarms in laboratories, exploring the various contributing factors, analyzing the impact on research operations, and providing practical solutions to minimize their occurrence. By understanding the dynamics of false fire alarms and implementing proactive measures, laboratories can create a safer and more efficient environment, ensuring the smooth flow of research and the pursuit of scientific breakthroughs.
The quest to eliminate false fire alarms in laboratories is not merely a matter of convenience but a critical step towards optimizing research efficiency and ensuring the safety of personnel and valuable assets. By addressing the root causes, implementing preventative measures, and fostering a culture of awareness, laboratories can minimize the disruptive impact of false fire alarms and create a more conducive environment for scientific progress.
False Fire Alarms: A Persistent Problem in Laboratories
False fire alarms are a common occurrence in laboratories, disrupting research activities, causing unnecessary evacuations, and potentially leading to significant financial losses. These alarms can be triggered by a variety of factors, including faulty equipment, environmental conditions, and human error. While fire safety is paramount in any laboratory setting, the frequency of false alarms can lead to complacency and a diminished sense of urgency when a genuine fire emergency arises. This article delves into the complexities of false fire alarms in laboratories, exploring the underlying causes, the impact on research operations, and strategies for effective troubleshooting and prevention.
Understanding the Causes of False Fire Alarms
False fire alarms in laboratories can be attributed to a multitude of factors, each requiring a distinct approach to mitigation. A comprehensive understanding of these causes is crucial for developing effective troubleshooting strategies and implementing preventative measures. The following sections provide a detailed analysis of the most common causes of false fire alarms in laboratory environments.
1. Faulty Fire Detection Systems
The primary culprit behind false fire alarms is often malfunctioning fire detection systems. These systems rely on various technologies, including smoke detectors, heat detectors, and flame detectors, to detect the presence of fire. However, these systems can be susceptible to errors, leading to false alarms. Some common causes of faulty fire detection systems include:
- Dust and Debris Accumulation: Smoke detectors, particularly ionization detectors, are sensitive to dust and debris. Accumulation of these particles can trigger the alarm, even in the absence of fire. Regular cleaning and maintenance of smoke detectors are essential to prevent false alarms caused by dust and debris.
- Environmental Factors: Extreme temperatures, humidity, and air currents can affect the performance of fire detection systems. For instance, high humidity can cause condensation on smoke detector sensors, leading to false alarms. Similarly, strong air currents can disrupt the airflow patterns around heat detectors, triggering a false alarm.
- Electrical Malfunctions: Electrical faults in the wiring or circuitry of fire detection systems can also lead to false alarms. These faults can cause the system to malfunction, triggering an alarm even when no fire is present. Regular inspections and maintenance of electrical components are crucial to prevent electrical malfunctions.
- Aging Equipment: Fire detection systems, like any other equipment, deteriorate over time. Aging components can become less reliable, increasing the likelihood of false alarms. Regular replacement of aging components is essential to maintain the integrity of the fire detection system.
2. Laboratory-Specific Hazards
Laboratories present unique challenges for fire detection systems due to the presence of specialized equipment and chemicals. These factors can contribute to false alarms in ways that are not typically encountered in other environments. Some common laboratory-specific hazards include:
- Chemical Fumes and Vapors: Certain chemicals, particularly those with volatile organic compounds (VOCs), can trigger smoke detectors. These chemicals can release fumes or vapors that resemble smoke, leading to false alarms. Proper ventilation and the use of fume hoods are essential to minimize the release of chemical fumes and vapors.
- Dust and Particulate Matter: Laboratories often generate significant amounts of dust and particulate matter, particularly during experiments involving powders or other fine materials. These particles can accumulate on smoke detector sensors, triggering false alarms. Regular cleaning and maintenance of laboratory spaces are crucial to minimize dust and particulate matter accumulation.
- High-Temperature Equipment: Laboratories frequently utilize high-temperature equipment, such as ovens, furnaces, and autoclaves. The heat generated by these devices can trigger heat detectors, leading to false alarms. Proper installation and maintenance of high-temperature equipment are essential to prevent false alarms.
- Compressed Gases: Laboratories often use compressed gases, such as nitrogen, oxygen, and helium. Leaks in compressed gas lines can release gases that can trigger fire detection systems. Regular inspections and maintenance of compressed gas lines are crucial to prevent leaks.
3. Human Error
Human error can also contribute to false fire alarms in laboratories. These errors can range from accidental activation of fire alarms to improper handling of equipment and materials. Some common human errors include:
- Accidental Activation: Fire alarms can be accidentally activated by bumping into them, dropping objects on them, or even by strong air currents. Proper placement and protection of fire alarms are essential to minimize accidental activation.
- Improper Handling of Equipment: Improper handling of laboratory equipment, such as ovens or furnaces, can lead to overheating or malfunction, triggering fire alarms. Proper training and adherence to safety protocols are essential to prevent improper handling of equipment.
- Inadequate Training: Insufficient training on fire safety procedures can lead to mistakes that trigger false alarms. Comprehensive training programs that cover the operation of fire detection systems, evacuation procedures, and the proper handling of equipment and materials are essential for laboratory personnel.
- Lack of Awareness: A lack of awareness of the potential causes of false alarms can lead to complacency and a diminished sense of urgency when a genuine fire emergency arises. Regular fire drills and safety training are crucial to maintain awareness and preparedness.
The Impact of False Fire Alarms on Laboratory Operations
False fire alarms have a significant impact on laboratory operations, disrupting research activities, causing unnecessary evacuations, and potentially leading to financial losses. The following sections explore the specific consequences of false alarms in laboratory settings.
1. Disruption of Research Activities
False fire alarms can disrupt research activities, causing delays, interruptions, and potential loss of data. When a fire alarm sounds, laboratory personnel are required to evacuate the building, leaving experiments running, equipment unattended, and sensitive materials exposed. This can lead to:
- Experiment Interruption: Ongoing experiments can be interrupted, requiring restarting and potentially compromising the integrity of the data collected. This can lead to delays in research progress and increased costs associated with repeating experiments.
- Equipment Damage: Unattended equipment, such as incubators, centrifuges, or lasers, can be damaged during evacuations. This can result in costly repairs or replacements, further disrupting research activities.
- Loss of Data: Sensitive data, such as cell cultures, biological samples, or experimental results, can be lost during evacuations. This can be a significant setback for research projects, requiring time and resources to recreate the lost data.
2. Unnecessary Evacuations
False fire alarms trigger unnecessary evacuations, disrupting the workflow of laboratory personnel and causing inconvenience and stress. These evacuations can be time-consuming, requiring everyone to leave the building and wait for the all-clear signal. This can lead to:
- Loss of Productivity: Evacuations disrupt the workflow of laboratory personnel, reducing productivity and delaying research progress. This can be particularly problematic for time-sensitive experiments or projects with tight deadlines.
- Increased Stress: Frequent false alarms can lead to increased stress and anxiety among laboratory personnel. This can affect their focus, concentration, and overall well-being, potentially impacting their performance.
- Safety Concerns: While evacuations are essential in genuine fire emergencies, frequent false alarms can lead to complacency and a diminished sense of urgency when a real fire occurs. This can compromise safety and increase the risk of injury or loss of life.
3. Financial Losses
False fire alarms can result in significant financial losses for laboratories. These losses can stem from the disruption of research activities, the cost of repairs or replacements for damaged equipment, and the potential for legal liabilities. Some common financial consequences of false alarms include:
- Research Delays and Costs: False alarms can lead to delays in research projects, increasing the overall cost of research. This can include the cost of repeating experiments, extending project timelines, and potentially losing funding opportunities.
- Equipment Damage and Repairs: False alarms can cause damage to laboratory equipment, requiring costly repairs or replacements. This can include damage to incubators, centrifuges, lasers, and other specialized equipment.
- Legal Liabilities: False alarms can lead to legal liabilities, particularly if they result in injuries or property damage. This can include lawsuits from employees, visitors, or neighboring businesses.
Troubleshooting False Fire Alarms: A Step-by-Step Approach
Troubleshooting false fire alarms in laboratories requires a systematic and comprehensive approach. This involves identifying the root cause of the alarm, addressing the underlying issue, and implementing preventative measures to minimize future occurrences. The following steps provide a detailed guide to troubleshooting false fire alarms in laboratory settings.
1. Identify the Triggering Event
The first step in troubleshooting a false fire alarm is to identify the triggering event. This involves determining what caused the alarm to activate, whether it was a malfunctioning fire detection system, a laboratory-specific hazard, or human error. This can be achieved by:
- Reviewing Alarm Logs: Fire detection systems typically record alarm events, including the time, date, and location of the alarm. Reviewing these logs can provide valuable insights into the triggering event.
- Inspecting the Alarm System: A visual inspection of the fire detection system can help identify any obvious signs of malfunction, such as dust accumulation, loose wiring, or damaged components.
- Interviewing Witnesses: Interviewing laboratory personnel who were present during the alarm can provide valuable information about the triggering event, including any unusual activities or conditions that may have contributed to the alarm.
2. Investigate the Root Cause
Once the triggering event has been identified, the next step is to investigate the root cause of the alarm. This involves determining the underlying factor that led to the triggering event, whether it was a faulty component, a hazardous condition, or human error. This can be achieved by:
- Testing the Fire Detection System: Testing the fire detection system can help identify any malfunctions or sensitivities that may be contributing to false alarms. This can include testing smoke detectors, heat detectors, and flame detectors.
- Analyzing Environmental Conditions: Analyzing the environmental conditions in the laboratory, such as temperature, humidity, and air currents, can help identify any factors that may be affecting the performance of the fire detection system.
- Reviewing Safety Procedures: Reviewing laboratory safety procedures can help identify any potential hazards or human errors that may be contributing to false alarms. This can include reviewing procedures for handling chemicals, operating equipment, and responding to fire alarms.
3. Implement Corrective Actions
Once the root cause of the false alarm has been identified, the next step is to implement corrective actions to address the underlying issue. This may involve repairing or replacing faulty components, modifying environmental conditions, or improving safety procedures. Some common corrective actions include:
- Repair or Replace Faulty Components: If the root cause of the false alarm is a faulty component in the fire detection system, such as a smoke detector or heat detector, the component should be repaired or replaced. This ensures that the system is functioning properly and minimizes the risk of future false alarms.
- Modify Environmental Conditions: If the root cause of the false alarm is related to environmental conditions, such as high humidity or strong air currents, steps should be taken to modify these conditions. This may involve improving ventilation, installing air filters, or adjusting the temperature and humidity controls.
- Improve Safety Procedures: If the root cause of the false alarm is related to human error, steps should be taken to improve safety procedures. This may involve providing additional training on fire safety procedures, implementing stricter protocols for handling chemicals and equipment, or improving communication and coordination among laboratory personnel.
4. Prevent Future Occurrences
Once corrective actions have been implemented, it is essential to take steps to prevent future occurrences of false alarms. This involves implementing preventative measures to address the underlying causes of the alarms and minimize the risk of future incidents. Some common preventative measures include:
- Regular Maintenance and Inspections: Regular maintenance and inspections of fire detection systems are crucial to ensure their proper functioning and minimize the risk of false alarms. This should include cleaning smoke detectors, testing heat detectors, and inspecting electrical wiring and circuitry.
- Environmental Monitoring: Monitoring environmental conditions in the laboratory, such as temperature, humidity, and air currents, can help identify any potential issues that may affect the performance of the fire detection system. This can involve installing sensors to monitor these conditions and alerting personnel to any deviations from acceptable ranges.
- Employee Training and Awareness: Providing employees with comprehensive training on fire safety procedures, including the operation of fire detection systems, evacuation procedures, and the proper handling of chemicals and equipment, can help minimize human error and prevent false alarms. Regular fire drills and safety training sessions can reinforce these procedures and maintain awareness among employees.
Conclusion: A Comprehensive Approach to Fire Safety in Laboratories
False fire alarms are a persistent problem in laboratories, disrupting research activities, causing unnecessary evacuations, and potentially leading to significant financial losses. By understanding the underlying causes of false alarms, implementing effective troubleshooting strategies, and taking preventative measures, laboratories can minimize the occurrence of these incidents and ensure a safe and productive research environment. A comprehensive approach to fire safety in laboratories involves a combination of technical solutions, operational procedures, and employee training, all working together to create a culture of safety and minimize the risk of fire emergencies.
Prevent Future Disruptions
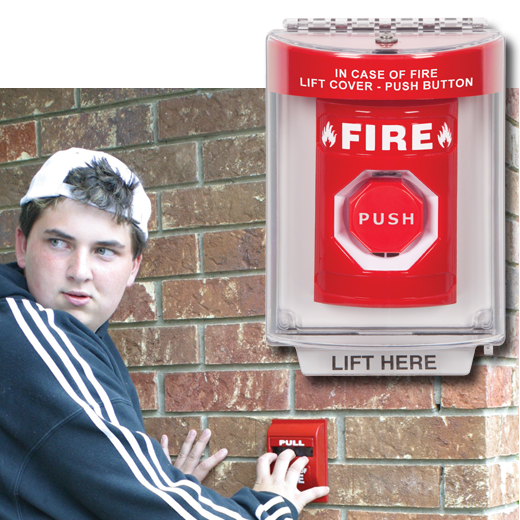
The relentless pursuit of scientific discovery often hinges on the seamless operation of laboratories. However, the specter of false fire alarms can disrupt this delicate balance, leading to costly downtime, compromised experiments, and a ripple effect of frustration throughout the research ecosystem. While the initial response to a false alarm might be a sigh of relief, the underlying causes demand attention. Addressing these issues is not merely about restoring normalcy; it's about safeguarding the integrity of research, optimizing resource allocation, and ensuring the safety of personnel. This is where a proactive approach to fire alarm maintenance and troubleshooting becomes paramount.
The journey towards preventing future disruptions begins with a comprehensive understanding of the potential culprits behind false alarms. Faulty sensors, environmental factors, and even routine maintenance practices can all contribute to these unwelcome events. By meticulously investigating the root cause of each false alarm, laboratories can identify patterns, pinpoint recurring issues, and implement targeted solutions. This process involves a collaborative effort between lab technicians, project managers, and procurement teams, ensuring that the right expertise is brought to bear on the problem.
Beyond the immediate troubleshooting, a long-term strategy for fire alarm maintenance is essential. Regular inspections, calibration, and cleaning of sensors are crucial for maintaining their accuracy and responsiveness. This proactive approach not only minimizes the risk of false alarms but also ensures the reliability of the fire fighting system in the event of a genuine emergency. Furthermore, laboratories should consider implementing a comprehensive training program for personnel, equipping them with the knowledge and skills to respond appropriately to fire alarms, whether real or false.
The impact of false fire alarms extends beyond the immediate disruption. The loss of valuable research time, the potential for damage to sensitive equipment, and the disruption to workflow can have significant financial and scientific consequences. By taking a proactive approach to fire alarm maintenance and troubleshooting, laboratories can mitigate these risks, ensuring a more stable and productive research environment.
IT Tech understands the critical role that reliable fire fighting systems play in the scientific community. Our comprehensive range of lab consumables and equipment includes a wide selection of fire alarm components, sensors, and maintenance tools. We are committed to providing our clients with the highest quality products and expert support, empowering them to build robust and reliable fire safety systems. To learn more about our offerings and how we can help you prevent future disruptions, we encourage you to submit an enquiry today.
IT Tech: Your Partner in Scientific Excellence.
Products You may Like
Check out other IT- Tech product that suit your taste
Subscribe to our newsletter
Stay updated with IT-Tech Insights
Related posts
Check out other IT- Tech Scientific Resources
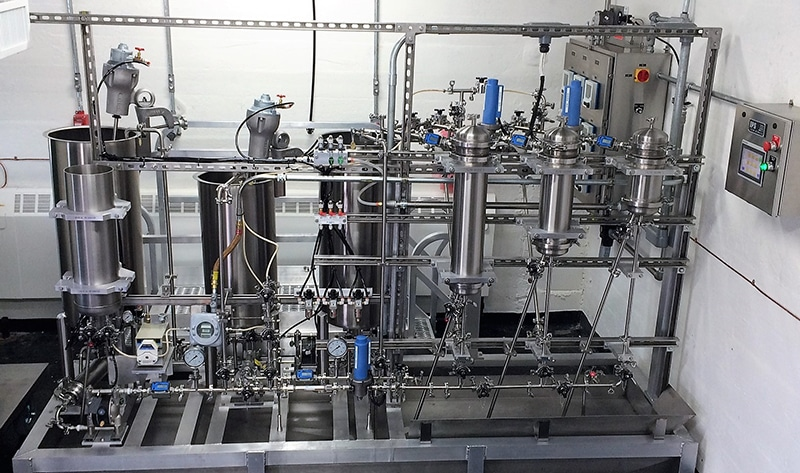
Comparing lab wastewater treatment methods
This article provides a comprehensive comparison of various lab wastewater treatment methods, including chemical, biological, and physical techniques. We delve into the advantages and disadvantages of each method, considering factors such as efficiency, cost, and environmental impact. The article also discusses the importance of complying with regulations and ensuring the safety of lab wastewater discharge. By understanding the different treatment options, researchers can make informed decisions about the most suitable method for their specific needs and contribute to responsible waste management practices.
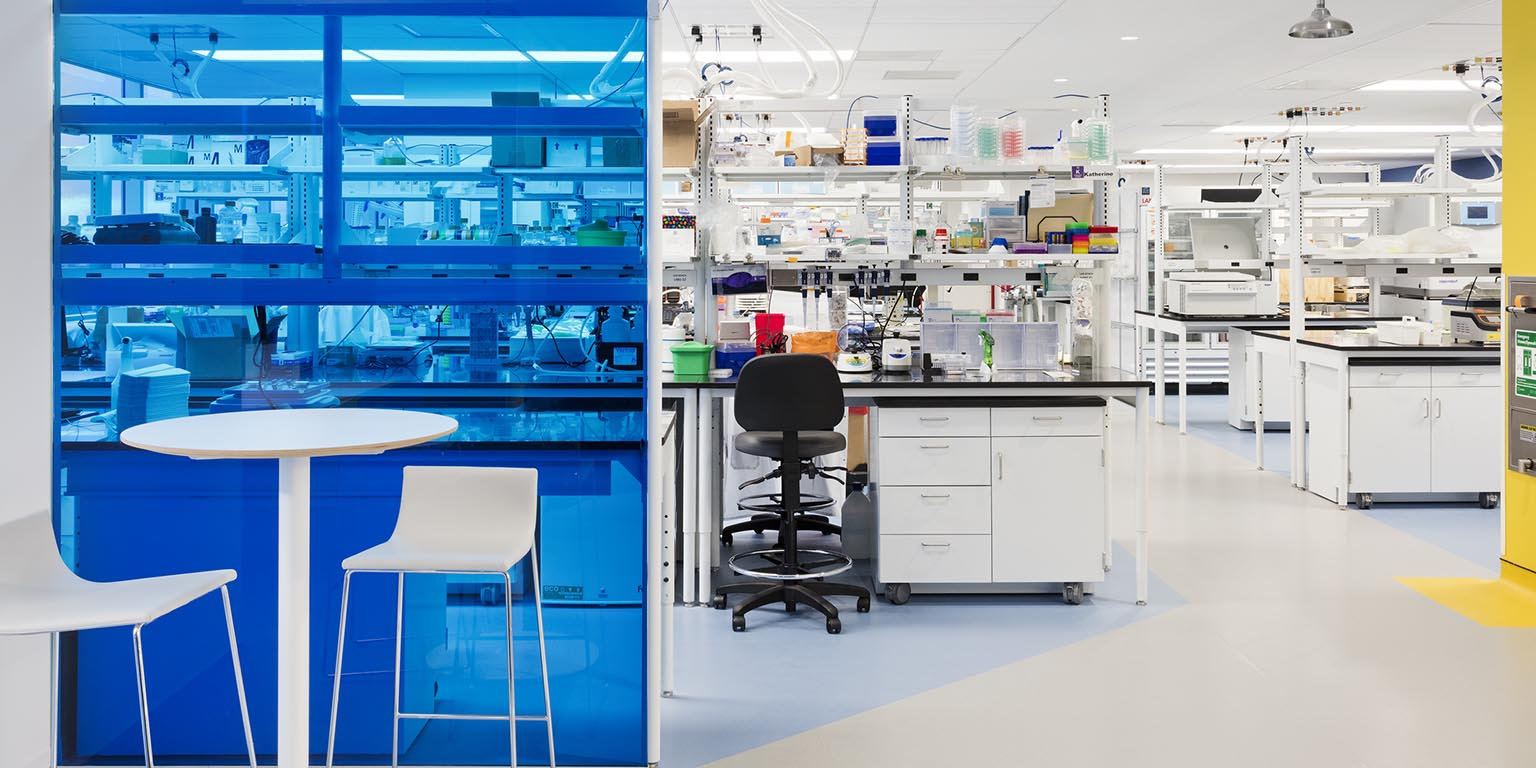
Selecting finishes and furniture for lab ergonomics
Selecting the right finishes and furniture for your lab is crucial for creating a comfortable and productive workspace. Ergonomics plays a vital role in minimizing fatigue and maximizing efficiency. This article explores key considerations for lab design, including choosing the right work surfaces, seating, and storage solutions. We'll also discuss the importance of lighting, ventilation, and noise control in creating a safe and comfortable environment for your researchers.
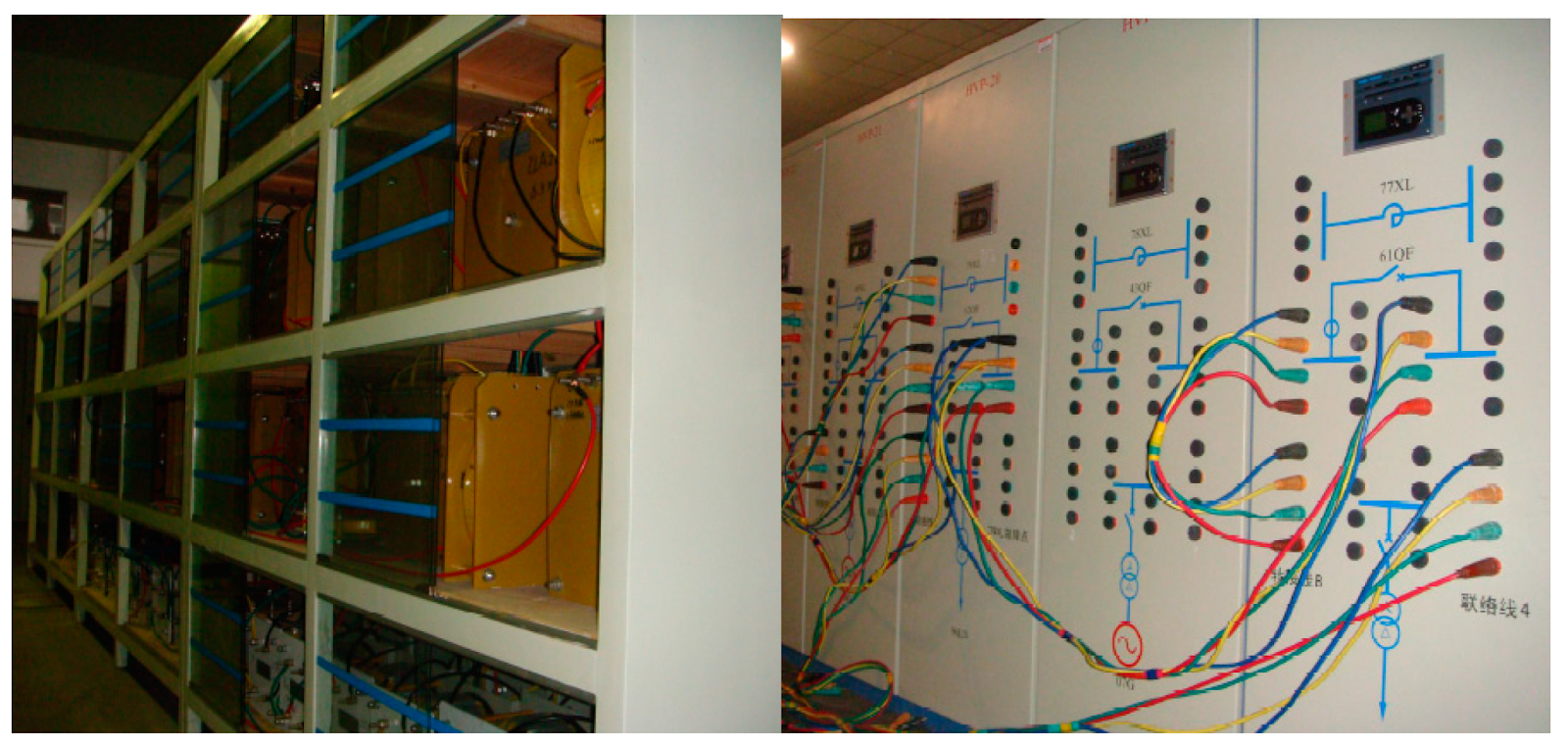
Introduction to electrical design for labs
Designing a lab's electrical system is crucial for ensuring safety, efficiency, and optimal performance. This article covers fundamental concepts, including power distribution, grounding, and safety protocols. We'll explore factors like voltage requirements, circuit protection, and the importance of proper wiring. Understanding these principles is essential for creating a lab environment that meets the demands of research and experimentation.