Unlocking Full Potential: Advanced Uses for Fermentors
.png)
Fermentors, also known as bioreactors, are essential tools in bioprocessing, enabling the growth of microbial, animal, or plant cells under controlled conditions. While basic fermentors provide rudimentary control over parameters like temperature, pH, and oxygen levels, advanced fermentor systems offer much greater precision and flexibility, unlocking a myriad of novel applications across various industries.
Sensor Integration
Advanced fermentors integrate a plethora of sensors to monitor crucial parameters in real-time, providing valuable data for precise control and optimization. Optical density sensors track cell growth and biomass levels, while flow sensors and online gas analyzers monitor gas flow rates and analyze outgoing gas composition. Nutrient and metabolite analysis through sampling ports offers insights into microbial metabolism, aiding in process optimization. Foam, level, and pressure sensors ensure safe operation and help maintain optimal conditions within the fermentor.
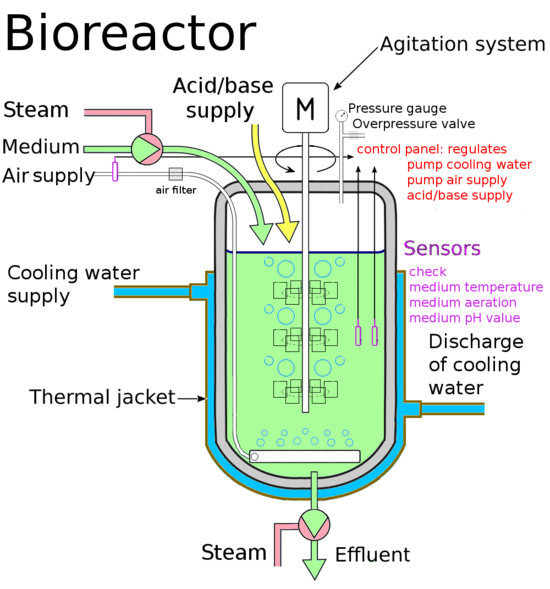
Optimizing Fermentor Design Through Sensor Integration
Key to unlocking the full potential of fermentors is integrating sensors that provide real-time data on multiple parameters. Basic fermentor setups may only monitor temperature, pH, and dissolved oxygen. More advanced systems incorporate additional sensors such as:
- Optical density sensors to monitor cell growth and biomass levels
- Flow sensors on incoming gas lines
- Online gas analyzers to measure outgoing CO2 and O2 levels
- Nutrient and metabolite analysis through sampling ports
- Foam, level, and pressure sensors
Integrating these extra sensors enables much tighter regulation of conditions through feedback control. If CO2 levels spike, indicating accelerated microbial respiration, the fermentor can automatically adjust aeration rates. Optical density measurements allow automated induction of gene expression at specific cell densities. The additional data also provides valuable insight into microbial metabolism for process optimization.
Achieving Precise Environmental Control
Basic fermentors provide relatively crude environmental control - for example by bubbling filtered air through the growth medium. Advanced fermentors allow independent control over multiple parameters:
- Temperature - Integrated heating/cooling jackets and coils maintain temperatures within 0.1°C.
- pH - Automatic acid/base addition using peristaltic pumps keeps pH within 0.01 units.
- Dissolved Oxygen - Agitation speed and gas mix (O2, N2, air) are adjusted to control DO levels.
- Nutrients - Peristaltic pumps add concentrated media stocks to maintain nutrient levels.
- Foam Control - Sensors detect foam build up and trigger automated addition of anti-foam agents.
- Gas Mixing - Mass flow controllers blend up to 4 gases (air, O2, N2, CO2) in precise ratios.
This level of control is critical for processes like mammalian cell culture where cells are extremely sensitive to environmental changes. The advanced control systems help maintain optimal steady-state growth conditions.
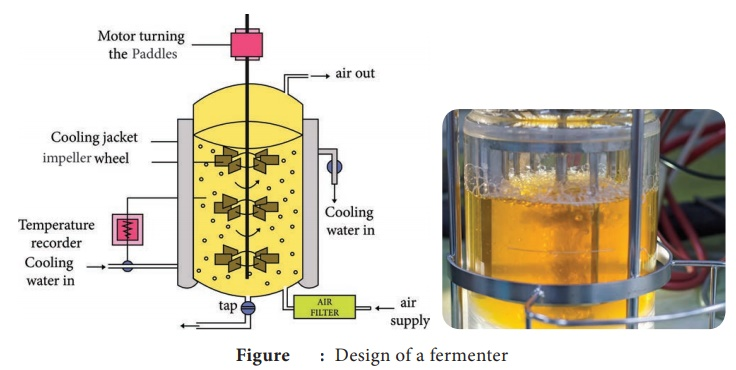
Improving Mixing and Mass Transfer
Sufficient mixing and mass transfer are essential in fermentors to keep cells suspended, prevent localized concentration gradients, and ensure uniform distribution of nutrients, gases, and metabolites.
Advanced fermentor vessels are designed to enhance mixing and mass transfer. Features may include:
- Baffles - Vertical plates on interior vessel walls promote tangential flow and turbulence.
- Impellers - Specialized impeller designs (e.g. Rushton, marine) provide axial and radial mixing.
- Spargers - Gas injection through porous spargers generates small bubbles to improve gas-liquid mass transfer.
- Perfusion Systems - Media is continuously circulated through external perfusion loops to enhance nutrient delivery.
- Rocking Motion - Rocking bioreactors provide wave-induced mixing for shear sensitive cultures.
These design elements allow much higher cell densities to be achieved compared to shake flasks or simple stirred tanks. The controlled mixing also results in more consistent growth conditions throughout the vessel.
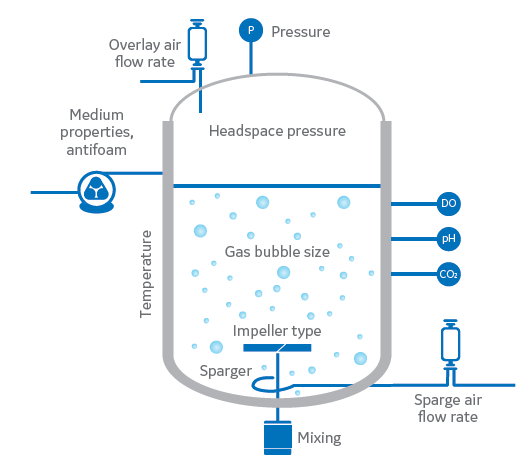
Supporting Sensitive or Shear-Prone Cultures
Standard agitation and aeration used in fermentors can damage or lyse sensitive cultures like animal cells or plant tissues. Advanced fermentors allow users to optimize conditions to support the growth of shear-sensitive cells. Strategies include:
- Low-shear Impellers - Wide-blade impellers like marine propellers minimize damage.
- Perfusion Systems - Circulating media through an external loop minimizes mechanical stress.
- Airlift Fermentors - Bubbling gas through a draught tube reduces agitation requirements.
- Encapsulation - Cell immobilization in alginate beads protects from shear.
- Rocking Motion - Rocking bioreactors provide gentler wave-induced mixing.
For plant and algal cultures, specialized photobioreactors are used. These optimize lighting conditions while still providing mixing, gas exchange, and process control.
Overall, the advanced control and hardware options available in state-of-the-art fermentors allow almost any type of microbial, plant, or animal culture to be grown successfully.
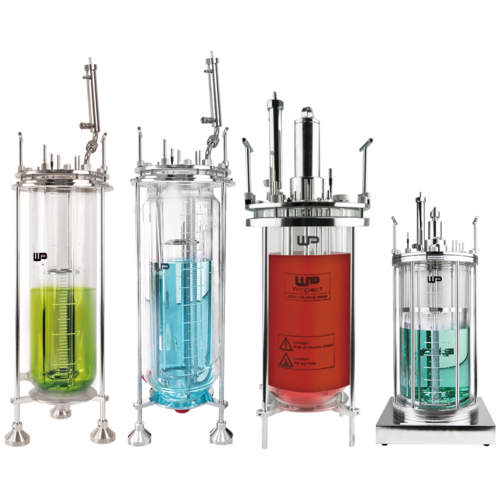
Facilitating Continuous Processing
In addition to batch culture, advanced fermentors enable continuous fermentation processes. This involves constant addition of fresh media and removal of culture broth to reach a steady-state growth condition. Benefits include:
- Increased productivity through constant harvesting of product
- Continuous bioprocessing reduces downtime
- Tighter control over environmental parameters
- Easier scale-up by maintaining constant conditions
- Potential for cell recycle and reduced media usage
Continuous fermentation can be achieved using specialized chemostat fermentors or by continuous peripheral harvesting and media addition to regular fermentors. This operational mode is especially suited to the production of commodities like biofuels and solvents.
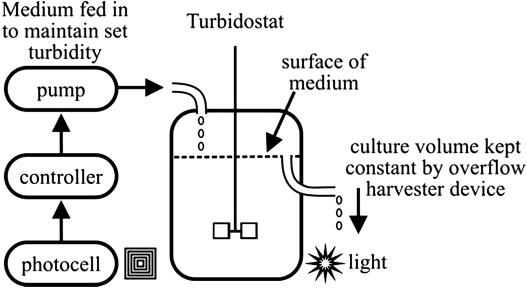
Scaling Up from Laboratory to Industrial Volumes
Once a fermentation process has been optimized in lab-scale fermentors, the next step is scale up to produce industrially relevant volumes. Advances in fermentor engineering enable reliable linear scale up from bench volumes to thousands of liters. Strategies include:
- Maintaining constant power draw per unit volume across vessel sizes
- Keeping a constant ratio between impeller diameter and tank diameter
- Preserving mixing time and mass transfer coefficients
- Monitoring differences in oxygen transfer at larger volumes
- Adjusting feeding and sampling strategies to avoid concentration gradients
With proper bioreactor equations and experience, cultures can typically be scaled up 10,000 fold or greater. This enables the economical production of commodity chemicals along with lower volume, higher value biologics like recombinant proteins and antibodies.
Alternative Image 6: Scaling Up
Caption: Scale-up process from laboratory to industrial volumes using advanced fermentor technology.
Implementing Advanced Control Strategies
Sophisticated software control systems are vital for fully leveraging the capabilities of advanced fermentors. These automation systems allow users to:
- Create multi-stage DO, pH, and temperature profiles that shift dynamically based on process stage
- Trigger automated media, acid, base, and inducer additions
- Integrate control with online sensors and analyzers to enable feedback loops
- Configure cascading PID control loops for precise regulation of multiple parameters
- Implement advanced algorithms like fuzzy logic and neural networks for adaptive control
- Facilitate hands-off automated operation and data logging
These automation capabilities reduce manual work, improve process consistency, and allow extremely tight control over all aspects of a bioprocess. This level of control enables the development of highly optimized production strains and processes.
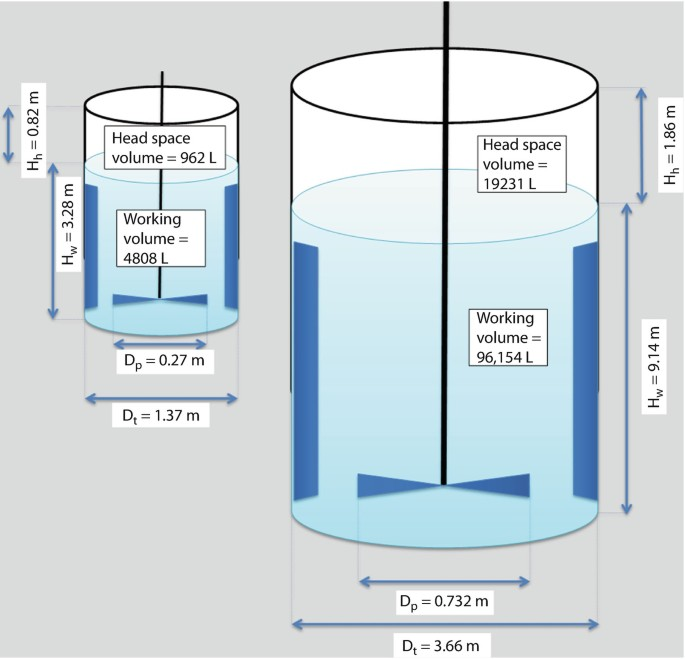
Conclusion
The full potential of fermentors is realized through integration of advanced sensors, precise environmental control, optimized hardware design, gentle handling of sensitive cultures, effective scale up, continuous processing capabilities, and intelligent automation strategies. State-of-the-art fermentors are highly flexible, configurable bioprocessing platforms. With appropriate expertise and experience, they can be adapted to suit virtually any microbial, plant, or animal-based production process.
To explore how advanced fermentors could benefit your laboratory or production goals, please [contact IT Tech] to speak with one of our bioprocessing experts. We offer a range of configurable pilot and production-scale fermentation systems along with process development services to help your biologics manufacturing or bioscience R&D reach the next level. Our team looks forward to helping you achieve your bioprocessing goals.
Products You may Like
Check out other IT- Tech product that suit your taste
Subscribe to our newsletter
Stay updated with IT-Tech Insights
Related posts
Check out other IT- Tech Scientific Resources
.png)
Integrating Bioreactors & Fermentors for Lab Efficiency
Discover expert tips and best practices for seamlessly integrating bioreactors and fermentors into your laboratory workflow. From selecting the right equipment to optimizing growth conditions, elevate your scientific endeavors with our comprehensive guide.
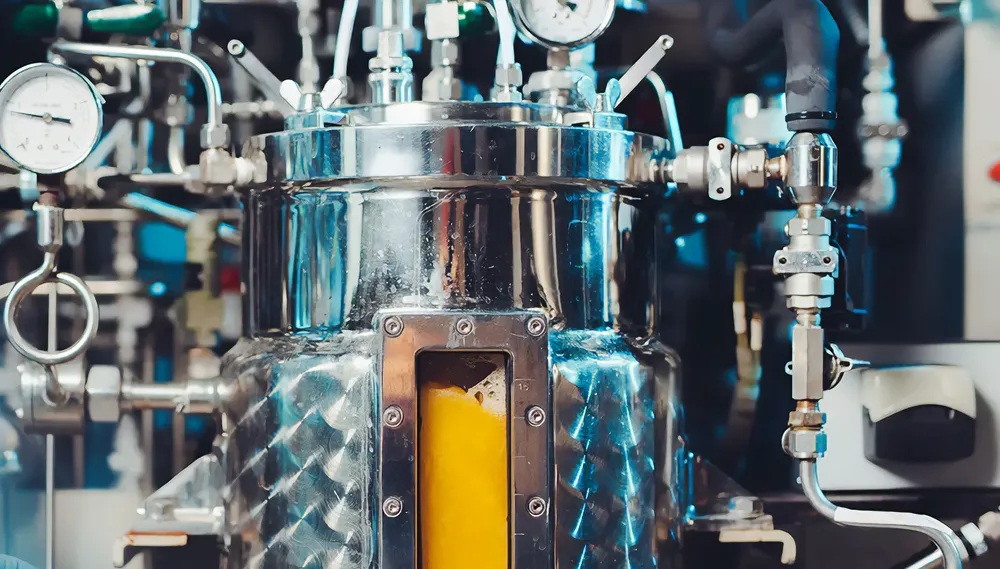
Transforming Scientific Discovery with Bioreactors and Fermentors
Explore the transformative potential of bioreactors and fermentors in driving cutting-edge research across biotechnology, pharmaceuticals, and more. Discover the latest advancements shaping the future of scientific innovation.
.png)
Making the Right Investment: A Detailed Analysis of Bioreactors
Discover the definitive guide to making informed investments in bioreactors. Explore the technical nuances, economic considerations, and supplier partnerships crucial for maximizing returns in bioprocessing. From single-use to stainless steel, gain insights to navigate the complexities and optimize your lab or production facility with expert advice and tailored solutions.